Steam piping is one of the high-temperature and high-pressure piping systems typically found in power plants and process plants. For power plants, the design code followed for steam piping in ASME B31.1 and they have more stringent requirements as compared to the steam piping in process plants which is designed based on the ASME B31.3 code. In this article, we will learn some of the basic design considerations followed in steam piping systems.
What is Steam Piping?
Steam piping is the piping network that carries steam for various purposes. Steam is widely used in power plants for power generation and in process plants for heating, tracing, utilities, etc. Due to very high temperatures and pressure, designing steam piping is always considered critical and careful attention must be given while designing a steam piping network.
Sometimes, local authorities control the design and approval of steam piping systems. For example, In India, the steam piping system needs approval from Indian Boiler Regulation or IBR. Fig. 1 below shows a typical steam piping network.
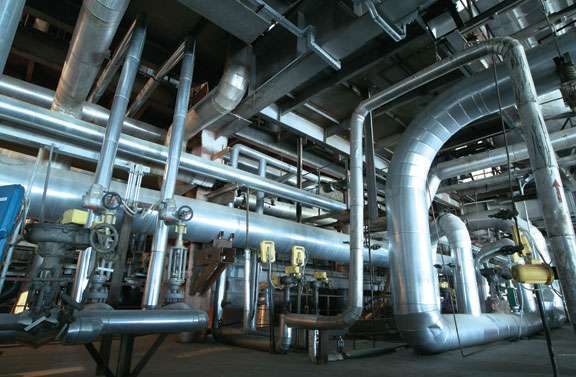
Components of a Steam Piping System
For safe and efficient working, every steam piping system consists of several components. Some of these components are:
Boiler:
The boiler is responsible for generating steam by heating water. The steam produced is then transferred to the piping system.
Steam Piping Network:
The piping network consists of a series of interconnected pipes that transport steam from the boiler to various points of use. These pipes are typically made of steel due to their strength and ability to withstand high temperatures and pressures.
Valves:
Valves are essential for controlling the flow of steam and isolating sections of the piping system for maintenance or repairs. Common valve types used in steam piping systems include gate valves, globe valves, and ball valves.
Fittings:
Fittings are used to connect and join different sections of piping, allowing for changes in direction, size, or branching. Examples of fittings used in steam piping systems include elbows, tees, reducers, and couplings.
Insulation:
Insulation is crucial for minimizing heat loss in the piping system, thereby maximizing energy efficiency. Insulating materials, such as mineral wool or foam, are applied to the exterior of the pipes to reduce heat transfer.
Steam Traps:
Steam traps are used to eliminate the condensate from the system and reduce the formation of a two-phase flow. Click here to learn more about steam traps and their design. A Strainer is usually installed in front of every steam trap to arrest rust, deposits, or construction fragments.
Steam Piping Design Consideration
Steam Pipe Sizing
Steam Pipe sizing is crucial for steam system design and is done by process engineers. Depending on the steam quality, pressure drop, flow rate, velocity, etc they perform various iterations to arrive at the most optimal size for the steam pipe. In general, Steam pipes of sizes NPS 1/2 up to NPS 24 are widely used.
Typically, for saturated steam, a velocity of 25 to 40 m/s is used, as above this, noise and erosion usually appear when the steam is wet. For longer supply lines, to avoid high-pressure drops, the velocity is limited to lower values.
Materials for Steam Piping
The common pipe material for steam piping networks is ASTM A106-Gr B. This material is used for steam piping when the pipe design temperature is up to 426 degrees C. When the design temperature exceeds 426 degrees (high-temperature superheated steam piping), allow steel materials to be used. Steam piping systems are often classified based on the pressure as follows:
- Low-Pressure Steam Piping System (LP Steam)
- Medium-Pressure Steam Piping System (MP Steam)
- High-Pressure Steam Piping System (HP Steam)
- High-High-Pressure Steam Piping System (HHP Steam)
The temperature and pressure both increase when we move from LP to MP to HP to HHP steam piping system. As the pressure increases the pipe thickness increases making the steam piping system more rigid. At the same time, as the temperature increases, the thermal expansion becomes larger and allowable stress reduces which calls for an increase in the number of expansion loops.
Slope:
The main steam line is generally installed with a slope of not less than 1:100 in the direction of the steam flow. This slope helps in moving the condensate towards drain points to remove the condensate from the steam pipe. Condensate drain points are usually provided at every 30-50 m interval. The steam trap line is installed at least 25 to 30 mm from the bottom of the pocket for steam mains up to 100 mm, and at least 50 mm for larger mains to allow space below for any dirt and scale to settle. Learn more about piping slope from here.
Branch Connections:
It is preferable to take a branch connection from the top of the main steam line. It will ensure dry steam enters the branch connection. When the branch connections are taken from the side or bottom, they will accept the condensate and debris from the steam main. This can cause wet and dirty steam to reach the equipment, which may affect the equipment’s performance in the long run.
Maintenance and Safety
Regular maintenance is essential to ensure the continued performance and safety of a steam piping system. Here are some key maintenance tasks:
Inspections: Regular visual inspections should be conducted to identify any signs of leaks, corrosion, or damage to the piping system. Non-destructive testing techniques can also be employed to detect internal defects.
Valve Maintenance: Valves should be periodically inspected, lubricated, and tested for proper operation. This ensures that they can be relied upon for controlling steam flow and isolating sections of the system when required.
Insulation Integrity: Insulation should be inspected regularly to ensure it remains intact and adequately covers the pipes. Damaged insulation should be repaired or replaced promptly to prevent heat loss and energy inefficiency.
Steam Trap Maintenance: Steam traps are used to remove condensate from the piping system. Regular maintenance and testing of steam traps are necessary to ensure proper functioning and prevent energy losses.
Its a nice information which is easy to understand.Thanks for knowledge. Keep writing 🥰
Dear sir pls give me steam piping size callculate formulas.
And pls sent STEAM trap fitting procedure
can you tell which are the standards that are referred here. i mean indian standards or asme or american standards. it helps to quote to customers.
if you pls add the visual…then it will be more effective to understand sir….keep rocking as always….