Vacuum insulated piping (VIP) is a type of insulated cryogenic piping system that is used to transport cryogenic liquids, such as liquefied natural gas (LNG), liquid nitrogen, or liquid oxygen, from one location to another. VIP is designed to minimize heat transfer, thereby maintaining the temperature of the cryogenic liquid as it is being transported. Vacuum Insulated Piping is also known as Vacuum jacketed Piping.
Vacuum Insulated Piping consists of two concentric pipes, an inner pipe that carries the cryogenic liquid and an outer pipe that serves as a vacuum jacket. The space between the two pipes is evacuated to create a vacuum, which significantly reduces heat transfer by convection and conduction. The vacuum jacket is typically made of stainless steel and has an outer protective layer made of a material such as polyethylene.
The vacuum jacket is designed to maintain a high level of vacuum over long distances, and the inner pipe is usually made of a material that is compatible with the cryogenic liquid being transported, such as stainless steel or copper. VIP is typically used for applications that require the transportation of cryogenic liquids over long distances, such as in LNG terminals or in industrial gas supply systems. In general, Vacuum Jacketed pipes are manufactured in sizes from 1/2 inches to 16 inches.
Applications of Vacuum Insulated Piping System
Vacuum-insulated piping systems are used in a variety of applications where the transportation of cryogenic liquids is required. Here are some common applications for Vacuum Insulated Piping systems:
- Liquefied Natural Gas (LNG) terminals: VIP systems are used in LNG terminals to transport LNG from storage tanks to tanker ships, railcars, or trucks. VIP is preferred in LNG terminals because of its high level of insulation, which reduces heat transfer and minimizes the loss of LNG due to evaporation.
- Industrial gas supply systems: VIP systems are used to transport cryogenic gases such as nitrogen, oxygen, and argon from production plants to customer sites. VIP ensures that the gases are maintained at the required temperature and pressure during transportation, which is essential for the safe and efficient operation of industrial processes. Vacuum-insulated pipes are suitable to carry Liquid Nitrogen, Liquid Hydrogen, Liquid Natural Gas, Liquid Oxygen, Liquid Carbon Dioxide, Liquid Argon, Liquid Helium, Liquid Neon, and other cryogenic fluids.
- Food and beverage industry: Vacuum Jacketed Piping systems are used to transport cryogenic liquids such as liquid nitrogen and liquid carbon dioxide in the food and beverage industry. These liquids are used for cooling and freezing food products and for the carbonation of beverages.
- Medical and pharmaceutical industry: Vacuum Insulated Piping systems are used in the transportation of cryogenic liquids used in medical and pharmaceutical applications, such as liquid nitrogen for cryopreservation and liquid oxygen for respiratory therapy.
- Aerospace industry: VIP systems are used in the aerospace industry for the transportation of cryogenic propellants used in rockets and spacecraft. VIP is preferred because of its high level of insulation, which ensures that the propellants are maintained at the required temperature and pressure during transportation.
Advantages of Vacuum Insulated Pipes
Vacuum insulated piping (VIP) offers several advantages over traditional insulated piping systems. Here are some of the main advantages of VIP:
- High thermal insulation: VIP provides excellent thermal insulation, which reduces heat transfer by conduction and convection. This means that the cryogenic liquid can be transported over long distances without significant loss due to evaporation.
- Cost-effective: VIP can be more cost-effective than traditional insulated piping systems because it requires less insulation material, which reduces the overall cost of the system.
- Reduced maintenance: VIP requires less maintenance than traditional insulated piping systems because it is designed to maintain a high level of vacuum over long periods of time, which reduces the need for frequent inspections and repairs.
- Improved safety: VIP reduces the risk of accidents and spills because it minimizes the loss of cryogenic liquid due to evaporation, which can be a safety hazard.
- Flexible design: VIP can be designed to meet specific project requirements, such as transport distance, flow rate, and pressure. It can also be customized to accommodate different types of cryogenic liquids and to operate under various environmental conditions.
- Reduced environmental impact: VIP can help reduce the environmental impact of transporting cryogenic liquids because it reduces the loss of liquid due to evaporation, which can contribute to greenhouse gas emissions and other environmental concerns.
Types of Vacuum Insulated Pipes
There are two main types of vacuum insulated pipes (VIP) based on their construction and design:
Flexible Vacuum Insulated Pipes (FVIP)
A Flexible Vacuum Insulated Pipe consists of an inner pipe that carries the cryogenic liquid and an outer vacuum jacket made of a flexible material such as polyethylene. The vacuum space between the inner and outer pipes is maintained by the flexibility of the outer jacket material. FVIP is suitable for applications that require flexibility and easy installation, such as transporting LNG between terminals or in distribution networks.
Rigid Vacuum Insulated Pipes (RVIP)
Rigid Vacuum Insulated Pipes consist of an inner pipe that carries the cryogenic liquid and an outer vacuum jacket made of a rigid material such as stainless steel. The vacuum space between the inner and outer pipes is maintained by the rigidity of the outer jacket material. RVIP is suitable for applications that require high thermal efficiency and long-distance transportation, such as in industrial gas supply systems or in the aerospace industry.
Both types of vacuum-insulated pipes have their own advantages and disadvantages, and the choice of the appropriate type depends on the specific requirements of the application. Refer to Fig. 1 which shows a typical example of flexible and rigid vacuum-insulated pipes.
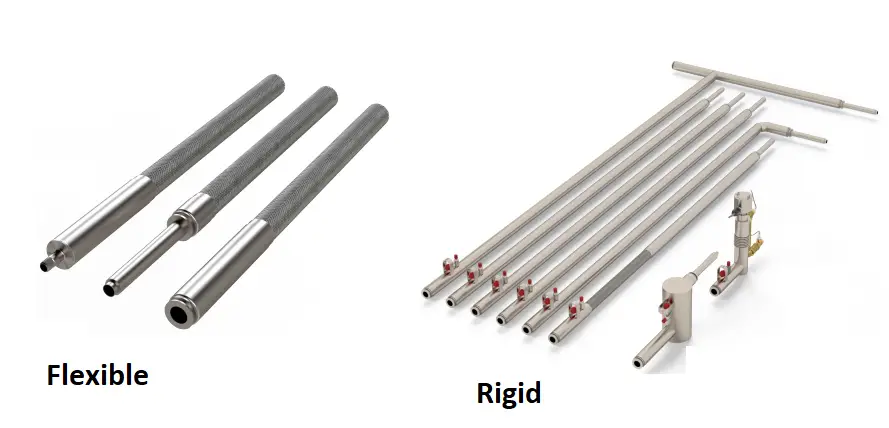
Specification of Vacuum Insulated Pipes
The specification of vacuum insulated pipes (VIP) depends on several factors such as the type of cryogenic fluid to be transported, the temperature range, pressure, flow rate, and distance of transportation. Here are some common specifications of VIP:
- Inner Pipe: The inner pipe is typically made of stainless steel or other corrosion-resistant materials and can have a diameter ranging from a few inches to several feet, depending on the application. The inner pipe is designed to withstand the cryogenic fluid’s low temperature and high pressure.
- Outer Jacket: The outer jacket is made of a material such as polyethylene or stainless steel and is designed to provide a vacuum space between the inner and outer pipes. The vacuum space provides high thermal insulation to reduce heat transfer.
- Insulation: The insulation layer is typically made of multiple layers of materials such as fiberglass, perlite, or aerogel. The insulation layer provides additional thermal insulation to reduce heat transfer.
- Fittings and Valves: VIP requires specialized fittings and valves designed to maintain the vacuum level and withstand the cryogenic fluid’s low temperature and high pressure.
- Vacuum Level: VIP requires a vacuum level of at least 10-5 torr to provide efficient thermal insulation.
- Testing: VIP must undergo rigorous testing to ensure that it meets the design specifications. This includes testing the vacuum level, insulation efficiency, and pressure resistance.
- Standards: VIP must meet industry standards such as ASME B31.3, which specifies the requirements for piping systems transporting cryogenic fluids.
Overall, the specification of VIP is critical to ensure that the system can safely and efficiently transport cryogenic fluids over long distances while minimizing heat loss and ensuring high thermal efficiency.
Fig. 2 below by Chart Industries shows the anatomy of a typical vacuum-insulated pipe with its components:
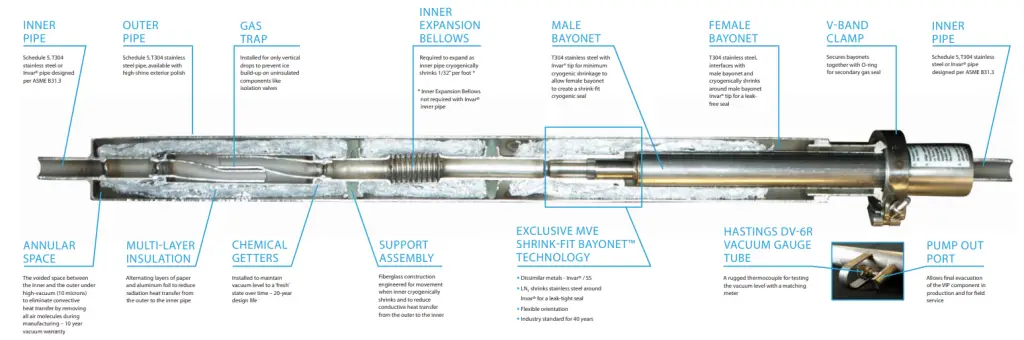
Differences between Vacuum Insulated Piping and Traditional Cryogenic Fluid Transfer Piping
The main differences between vacuum insulated piping (VIP) and traditional cryogenic fluid transfer piping are as follows:
- Insulation: Vacuum Insulated Pipes use a vacuum space between the inner and outer pipes to provide high thermal insulation, while traditional piping uses foam or fiberglass insulation. VIP insulation is more efficient than traditional insulation and can reduce heat transfer by conduction and convection by up to 90%.
- Heat loss: Vacuum Jacketed Pipes significantly reduce the heat loss during cryogenic fluid transportation, while traditional piping can lose a significant amount of cryogenic fluid due to evaporation.
- Maintenance: VIP requires less maintenance than traditional piping because it is designed to maintain a high vacuum level over long periods of time, while traditional piping requires regular maintenance to ensure that the insulation remains effective.
- Cost: VIP can be more expensive than traditional piping because it requires specialized materials and manufacturing processes to maintain a high vacuum level. However, the reduced heat loss and maintenance costs can make VIP more cost-effective over the long term.
- Flexibility: VIP can be more flexible than traditional piping because it can be designed to accommodate different types of cryogenic fluids and operate under various environmental conditions. Traditional piping is typically less flexible and may not be suitable for certain applications.
In summary, VIP provides higher thermal efficiency and reduced heat loss compared to traditional cryogenic fluid transfer piping. While VIP may be more expensive upfront, it can be more cost-effective in the long term due to reduced maintenance costs and improved safety.
Manufacturers of Vacuum Insulated Pipes
There are several established manufacturers of vacuum-insulated pipes (VIP) around the world. Here are some of the prominent manufacturers:
- Chart Industries: Chart Industries is a leading manufacturer of cryogenic equipment, including VIP systems. They offer a range of VIP systems for different applications, including LNG and industrial gases.
- Cryofab, Inc.: Cryofab, Inc. is a US-based manufacturer of cryogenic equipment, including VIP systems. They offer a range of VIP systems for different applications, including medical gases, LNG, and industrial gases.
- Cryostar: Cryostar is a French company that designs and manufactures cryogenic equipment, including VIP systems. They offer a range of VIP systems for different applications, including LNG and industrial gases.
- Technifab Products, Inc.: Technifab Products, Inc. is a US-based manufacturer of cryogenic equipment, including VIP systems. They offer a range of VIP systems for different applications, including LNG, industrial gases, and liquid nitrogen.
- Cryogenic Industries: Cryogenic Industries is a global manufacturer of cryogenic equipment, including VIP systems. They offer a range of VIP systems for different applications, including LNG, industrial gases, and liquid nitrogen.
- Kryo-Tech: Kryo-Tech is a German company that specializes in cryogenic equipment, including VIP systems. They offer a range of VIP systems for different applications, including LNG, industrial gases, and liquid nitrogen.
These are just a few examples of established manufacturers of VIP systems. There are many other manufacturers around the world, and it is important to choose a reputable manufacturer that can provide high-quality VIP systems that meet your specific requirements.
Good Evening,
Mr Kumar. I write from Bolivia. I really appreciate if you share more information about VACUUM INSOLATED PIPE. I work in a GNL Plant. And I need to read about this because I Have to do repar and mantenance VIP line. This is my first work about it.
Hi Mr Kumar,
Thanks for the great information on your site. I am currently designing a cryogenic vessel for storing nitrogen. I am designing a double-walled vessel and want to vacuum the space between the walls. Should I design a special distributed piping system with small holes for vacuuming, or can I use a simple pipe to connect to the vacuum pump?
Thank you in advance.