Welding is a critical process in construction, providing strength and durability to structures ranging from skyscrapers to bridges. However, the integrity of welded joints directly impacts safety and performance. This is where welding inspectors come in. Their expertise ensures that welding practices meet regulatory standards, industry specifications, and project requirements. In this article, we will explore the vital role of welding inspectors, the skills and qualifications required, and the challenges they face in the construction industry.
What is Welding?
Welding is the process of joining materials, usually metals, through the application of heat, pressure, or both. It is vital in construction due to its ability to create strong, durable joints that can withstand the forces of nature and the weight of structures. Some of the widely used welding techniques are:
- MIG (Metal Inert Gas) Welding: Utilizes a continuous wire feed and an inert gas to shield the weld pool. It is popular for its speed and ease of use.
- TIG (Tungsten Inert Gas) Welding: Employs a non-consumable tungsten electrode and is known for producing high-quality, precise welds.
- Stick Welding (SMAW): Utilizes a consumable electrode coated in flux to protect the weld area. It is versatile and can be used in various positions.
- Flux-Cored Arc Welding (FCAW): Similar to MIG, but uses a tubular wire filled with flux to create a weld. It’s effective for thicker materials.
What is Welding Inspection?
Welding inspection is the systematic process of examining welded joints and associated materials to ensure compliance with specified standards, codes, and project requirements. This crucial practice helps identify defects or inconsistencies that could compromise the integrity and safety of the welded structure. Welding inspectors employ various techniques, including visual inspections and non-destructive testing (NDT), to assess the quality and reliability of welds.
What Is Inspected in Welding?
In welding inspection, various aspects of the welding process are evaluated to ensure quality. For example, in pipe welding, inspectors focus on several critical factors. They assess the preparation of the pipe edges, ensuring they are clean and properly aligned before welding begins. During the welding process, inspectors monitor the welder’s technique, looking for consistent bead appearance and proper penetration into the base materials. After welding, inspections may involve visual assessments for surface defects, such as cracks or undercuts, as well as NDT methods like radiographic testing to identify any internal flaws, ensuring the joint will withstand operational stresses without failure. The welding inspection process typically involves several stages:
- Preparation: Reviewing project specifications and welding procedures.
- Testing: Performing NDT as required and analyzing the results.
- On-Site Inspection: Observing welding operations and assessing compliance with approved procedures.
- Reporting: Documenting findings, including any discrepancies and recommendations for corrective actions.
Who are Welding Inspectors?
Welding Inspectors are qualified individuals who ensure the quality and structural soundness of welding joints used in buildings, chemical and petrochemical plants, vehicles, power and process facilities, equipment and machinery, oil & gas and steel industries, etc. With their vast knowledge, welding inspectors fulfill safety and quality requirements and comply with required codes, standards, and specifications. They possess extensive knowledge of overall welding technology, including welding discontinuities, welding processes, welding materials, and electrodes. They oversee the activities and duties of the welding staff.
Welding inspectors work closely with engineers, project managers, and welders to ensure that quality standards are met. Their input is crucial in decision-making processes regarding welding procedures and quality control.
Responsibilities of a Welding Inspector
The major duties of a welding inspector are multifaceted. Their responsibilities start much before the actual welding process starts.
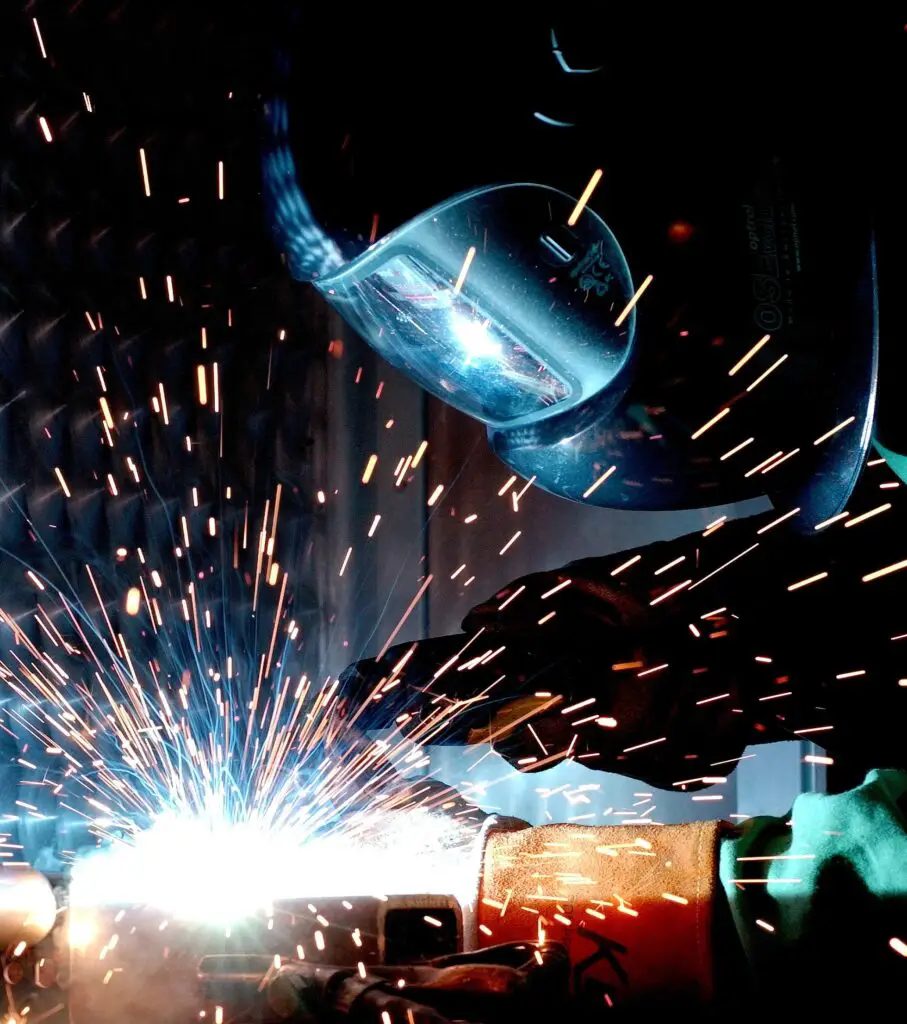
Duties of welding inspectors prior to the welding
- Issuing welding tickets to company workers.
- Review contract requirements and vendor/contractor compliance.
- Review and approve welding procedures.
- Review the welding methodology in the approved WPS (Welding Procedure Specification) and inspection requirements.
- Ensure that the material is as per the WPS/drawing and suitable for welding without any damage or contamination.
- Verify that the welding equipment is calibrated and in suitable condition to start welding.
- Check the welding preparations to ensure they are in accordance with WPS/drawings.
- Identify the qualifications of welders and the validity of their certificates.
- Check and verify the welding consumables.
- Verify that the base metal(s) and welding filler metal(s) are as per the specifications.
- Ensure that joint preparations, fit-ups, minimum preheat temperature, etc are in accordance with WPS/drawings.
- Inspect the Weld faces checking for any defects, contamination, and damage.
Responsibilities of welding inspectors during welding
- Ensure that the weather conditions are suitable for welding and comply with the code requirements.
- Monitor the overall welding work performed by the team and ensure the guidelines of WPS are followed to the core.
- Ensure the minimum preheat temperature is maintained during the welding operation.
- Welding Consumables, Welding parameters, etc are as per WPS.
- Ensure the Grinding, Cleaning, etc are performed following approved methods.
- Maintaining a clean and safe work area complying with safety requirements.
Roles of welding inspectors after the welding process
- Marking of Each weld with proper identification.
- Evaluate for suitability of inspection and inspect the completed welds as per the specified inspection procedures, standards, codes, and drawings and prepare an associated report.
- Ensure the correct weld dimensions.
- Verify the completion of all NDT.
- Assess the welding strength and quality and monitor the modifications or repair works.
- Prepare as-built drawings as per repair work or modifications.
- Monitor the PWHT process when required.
- Ensure all reports/records are completed and collated as required. All examinations must be documented following ISO 17637.
Other roles and responsibilities of a welding inspector
- Suggesting alternative welding techniques.
- Demonstrating correct welding procedures.
- Generating new welding techniques.
- Develop, implement, or oversee quality control programs and measures
- Ensuring welders adhere to state health and safety regulations.
Skills and Qualifications of Welding Inspectors
1. Technical Knowledge
A solid understanding of welding processes, materials, and equipment is crucial. Inspectors should be familiar with various welding techniques, such as MIG, TIG, and stick welding, and understand how different materials react to these methods.
2. Certification and Training
Most welding inspectors hold certifications from recognized organizations. The AWS offers the Certified Welding Inspector (CWI) credential, while other organizations provide similar certifications. Training typically involves both classroom education and hands-on experience.
3. Attention to Detail
Inspectors must possess a keen eye for detail. The ability to identify even minor defects can be crucial in preventing major structural failures.
4. Problem-Solving Skills
When issues arise, welding inspectors must think critically to identify the root cause and suggest practical solutions. This requires both technical expertise and creativity.
5. Strong Communication Skills
Effective communication is vital for conveying findings, making recommendations, and collaborating with various stakeholders in the construction process.
What is a Certified Welding Inspector?
A Certified Welding Inspector (CWI) is a professional who has demonstrated a thorough understanding of welding processes, techniques, and standards through a formal certification process, typically administered by organizations like the American Welding Society (AWS). CWIs are qualified to inspect welds and ensure compliance with applicable codes, specifications, and safety standards. Their expertise includes evaluating welding quality, conducting visual inspections, and performing non-destructive testing, making them essential for maintaining the integrity and safety of welded structures in various industries.
What are International Welding Inspection Certification Programs?
There are two kinds of internationally recognized certification programs for welding inspectors
CSWIP or Certificate Scheme for Welding Inspector Professionals:
The CSWIP scheme is a globally recognized certification program and it ensures and certifies the competence of welding inspectors as per ISO/IEC 17024. CSWIP is an international scheme approved by the United Kingdom Accreditation Service (UKAS).
It includes various levels of certification for different roles, such as welding inspectors, welding supervisors, and examiners. CSWIP certifications are widely accepted across industries, particularly in sectors like oil and gas, construction, and manufacturing. The program emphasizes the need for inspectors to possess both theoretical knowledge and practical skills, ensuring they can effectively evaluate welding processes and adhere to industry standards.
AWS CWI:
Similar to CSWIP, AWS CWI is also an international scheme where certificates of welding inspectors are approved by the American Welding Society (AWS).
The AWS CWI certification process includes a comprehensive examination covering welding processes, inspection techniques, and applicable codes and standards. This certification is highly regarded in the United States and many other countries, ensuring that certified inspectors can effectively evaluate weld quality, compliance, and safety. AWS CWIs are often required for projects in various industries, including construction, manufacturing, and aerospace, making this certification a valuable asset for professionals in the welding inspection field.
Welding Inspector professionals who are certified by any of the above two programs are called certified welding inspectors or CWI.
Both the above certificates are obtained through a rigorous exam pattern in various steps.
Comparison of AWS CWI and CSWIP
Here’s a table highlighting the major differences between AWS CWI (Certified Welding Inspector) and CSWIP (Certification Scheme for Welding and Inspection Personnel):
Criteria | AWS CWI | CSWIP |
---|---|---|
Governing Body | American Welding Society (AWS) | The Welding Institute (TWI) |
Geographical Focus | Primarily North America | International (widely recognized globally) |
Certification Levels | One main level for CWI, with additional specialized certifications (e.g., CWB, CWE) | Multiple levels, including Certified Welding Inspector, Supervisor, and Examiner |
Exam Structure | Written, practical, and visual exams | Written exams and practical assessments based on specific levels |
Industry Recognition | Highly regarded in the U.S. and recognized worldwide | Widely recognized in Europe and globally, especially in the oil and gas sectors |
Content Focus | Emphasis on American codes (e.g., AWS D1.1, ASME) | Focus on various international standards (e.g., ISO, EN) |
Recertification Requirements | Requires recertification every three years | Requires recertification every five years |
Training Options | Various AWS training programs and seminars | TWI training courses available, often more structured |
Practical Experience | Requires documented experience in welding and inspection | Requires documented experience, with specific hours based on level |
Additional Certifications | Offers a path to other specialized certifications | Offers different certifications at varying levels (e.g., Supervisors, Examiners) |
This table summarizes the key differences, helping professionals choose the certification that best fits their career goals and industry requirements.
Why you would like to be a CWI
Certified Welding Inspector or CWI is one of the best welding professions in the world. The top two reasons for anyone wishing to become a welding inspector are:
- Salary Range: A CWI is paid a handsome salary as compared to other engineering professions. A certified welding inspector earns in the range of $35 to $90 per hour. Within welding, this is the highest-paid job.
- Job Availability: Welding is such an engineering process that is required in various industries like oil and gas, refineries, chemical and petrochemical plants, power plants, steel industries, pharmaceutical industries, etc. So CWI has plenty of job opportunities in the world. CWI gets jobs in big companies like Shell, BP, etc. Most of the CWIs get a chance to travel the world for work purposes.
Other reasons for becoming a certified welding inspector are
- Career Advancement: Achieving CWI certification can significantly enhance career opportunities. It opens doors to advanced positions in welding inspection, quality assurance, and project management across various industries.
- Expertise and Knowledge: The process of obtaining CWI certification deepens understanding of welding processes, codes, and standards. This expertise not only boosts confidence but also enables inspectors to make informed decisions regarding weld quality.
- Impact on Safety: As a CWI, one plays a critical role in ensuring the safety and integrity of structures. This responsibility provides a sense of purpose, knowing that the work contributes to public safety and the reliability of essential infrastructure.
- Industry Demand: With the growing emphasis on quality assurance in construction and manufacturing, CWIs are in high demand. This demand translates into job security and potentially higher earning potential.
- Diverse Work Environment: Welding inspectors work in various settings, from construction sites to manufacturing plants. This variety keeps the job interesting and allows for continuous learning and growth.
- Networking Opportunities: Becoming a CWI connects individuals with a community of professionals in the welding and inspection fields, providing opportunities for collaboration, mentorship, and professional development.
How much does CSWIP Cost?
Depending on the country you reside, the fee for TWI (The Welding Institute) CSWIP 3.1 training and examination is approximately USD 2,000 to USD 3000.
Overall, candidates should budget approximately $2,500 to $4,000 when considering the full costs of training, exam fees, and materials. It’s advisable to check with specific training providers for the most accurate and up-to-date pricing.
How much does AWS CWI Cost?
The AWS CWI examination costs $1200 for AWS members and $1500 for non-AWS members.
The requirements (experience and education) for both the above courses are different. So check their websites prior to applying for any CWI courses.
Overall, candidates should budget approximately $2,000 to $4,000 to cover the complete costs of training, examination, and materials. It’s recommended to check with the AWS and specific training providers for the most accurate and up-to-date pricing.
Which is better, CSWIP or AWS CWI?
Determining whether CSWIP or AWS CWI is “better” largely depends on individual career goals and the specific industry context. If you’re primarily working in the United States or with American codes and standards, the AWS CWI may offer more relevant recognition and opportunities. On the other hand, CSWIP is highly regarded internationally, especially in sectors like oil and gas, making it a strong choice for those seeking global opportunities. Both certifications provide valuable knowledge and enhance credibility in the field of welding inspection, so the best option depends on your location, industry focus, and personal career aspirations. Ultimately, pursuing either certification can significantly bolster your qualifications as a welding inspector.
Jobs for Welding Inspectors
There are huge opportunities for certified welding inspectors in the construction industry. The jobs involve site work. Mostly all industries need welding inspectors. The major industries that recruit CWI professionals include the following
- Oil and Gas (Offshore and Onshore)
- Power Plants
- Pressure Vessels or Equipment manufacturing industries.
- Steel Industries
- Chemical and Petrochemical process plants
- Pharmaceutical Plants
- Refinery construction and modification
- Piping and Pipeline construction industries, etc
Few more welding articles for you.
Welding Galvanized Steel
Overview of Pipeline Welding
Welding Positions: Pipe Welding Positions
Welding Defects: Defects in Welding: Types of Welding Defects
Welding Inspector: CSWIP and AWS-CWI
General requirements for Field Welding
Underwater Welding & Inspection Overview
Methods for Welding Stainless Steel
Video Courses in Welding
To learn more about welding the following video courses you can refer to:
- Introduction to MIG Welding
- Understanding Welding Codes and Procedures
- The Basics of Gas Tungsten Arc Welding
- Certification in Welding Technology
- Understand Welding Symbols
- AWS-Certified Welding Inspector
Welding inspectors play a crucial role in the construction industry, ensuring that welded joints meet safety and quality standards. Their expertise not only protects the integrity of structures but also enhances overall project success. As the industry evolves, the demand for knowledgeable, detail-oriented welding inspectors will continue to grow, making it an exciting and rewarding career path for those with a passion for construction and quality assurance.
Informative blog.
Kindly publish more.
Thank You.
Great work Anup. Good material for Inspectors and over all knowledge for Engineers.