A fracture can be defined as the separation of the material into two or more parts. Failure of material can involve any of the two mechanisms; ductile fracture or brittle fracture. Both these fracture mechanisms in metal are distinct and different from each other. In this article, we will explore both of these failure mechanisms in detail.
What is Brittle Fracture or Brittle Failure?
Brittle fracture is the sudden and rapid metal failure in which the material shows little or no plastic strain. This is characterized by quick failure without any warning. The generated cracks propagate rapidly and the material collapses all of a sudden.
Brittle Fracture is a condition that occurs when a material is subjected to temperatures that make it less resilient, and therefore more brittle. The potential for material to become brittle depends on the type of material that is subjected to these low temperatures. Some materials, such as carbon and low alloy steels will become brittle at low temperatures and therefore susceptible to damage ranging from cracking to shattering or disintegration of equipment.
When a material becomes brittle, the consequences can be very serious. If the brittle material is subjected to an impact or an equivalent shock (ex. rapid pressurization) the combination could potentially lead to a catastrophic failure under certain conditions.
What is Ductile Fracture or Ductile Failure?
Ductile fracture is the material failure that exhibits substantial plastic deformation prior to fracture. The ductile fracture process is slow and gives enough warnings before final separation. Normally, a large amount of plastic flow is concentrated near the fracture faces.
The ductile fracture occurs over a period of time and normally occurs after yield stress, whereas brittle fracture is fast and can occur at lower stress levels than a ductile fracture. That is why Ductile fracture is considered better than brittle fracture. Refer to Fig. 1 below that explains both fracture mechanisms. The area under the stress-strain curve represents the absorbed energy before failure. Clearly, the required energy in brittle failure is quite less than the ductile failure.
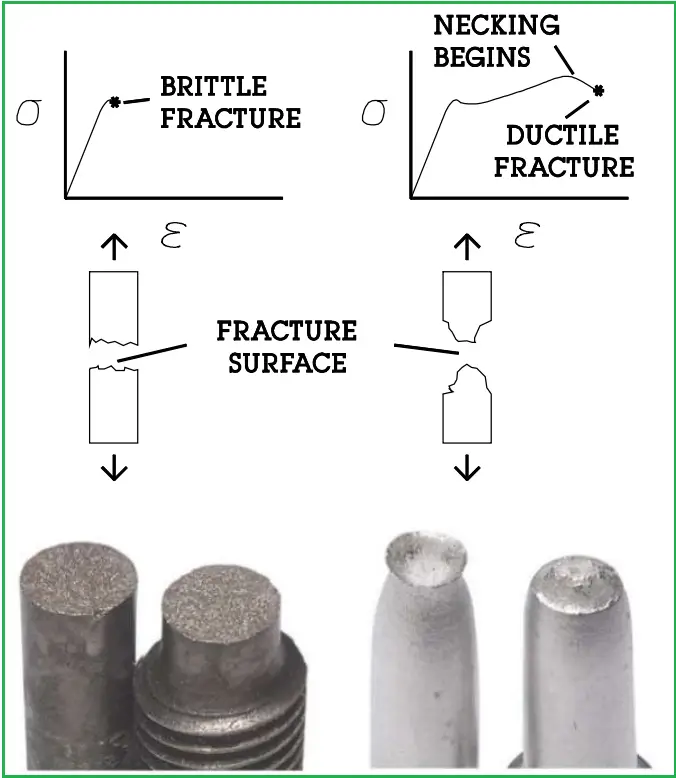
Brittle Fracture Mechanism
The mechanism of brittle fracture shown above is known as Brittle cleavage fracture. This occurs in metals with a high strain-hardening rate and relatively low cleavage strength.
Ductile materials under some conditions can become brittle if the conditions are changed. Such a condition is the effect of temperature. Many materials of industrial use exhibit ductile fracture at ambient and elevated temperatures and brittle fracture at low temperatures. The transition temperature below which a material is brittle and above which it is ductile is known as the Nil-Ductility Transition (NDT) temperature. This temperature is not constant but varies depending on prior mechanical and heat treatment and the nature and amounts of impurity elements. It is determined by the Izod or Charpy Impact tests. At temperature above the NDT temperature, some plastic deformation will occur before the fracture
With an increase in ductility, NDT decreases. So it is always preferred to increase ductility. The parameters that impact ductility are:
- Grain Size: small grain sizes increase ductility and grain size is controlled by heat treatment.
- Alloying Element: The addition of alloying elements can decrease grain size and thus decrease brittleness shifting the NDT to a lower temperature.
Cyclic stresses should be avoided for brittle materials. So, systems having thermal and pressure cycles should not be designed from brittle materials.
Causes of Brittle Fracture
The main concern with a brittle fracture or brittle failure is that under certain conditions failure occurs at stresses well below the yield strength. Such conditions are the presence of a flaw or crack. Brittle fractures are normally initiated by defects present in the manufactured product or fabricated structure or by defects that develop during service. These are basically stress concentrators and may take the form of.
- Notches- discontinuities caused by abrupt changes in the direction of a free surface, often fracture initiators. Examples: sharp fillets, corners, holes, threads, splines, keyways, dents, gouges, or scratches.
- Laps, folds, flakes, large inclusions, forging bursts, laminations, and undesirable grain.
- Segregation, inclusions, undesirable microstructures, porosity, tears, cracks, or surface discontinuities are introduced during melting, deoxidation, grain refining, and casting operations.
- Cracks resulting from machining, quenching, fatigue, hydrogen embrittlement, liquid metal embrittlement, or stress corrosion.
- Residual stresses.
Brittle fracture normally occurs because of the propagation of such cracks at great speed. Smaller grain size, higher temperature, and lower stress tend to mitigate crack initiation. On the contrary, larger grain sizes, lower temperatures, and higher stress favor crack propagation. There is a stress level known as the lower fracture propagation stress below which a crack will not propagate at any temperature. With the increase in temperature, higher stress is required for a crack to propagate. A crack arrest curve defines the relationship between the temperature and the stress required for a crack to propagate.
Fracture Toughness
The amount of stress required to propagate a preexisting crack is indicated by the Fracture Toughness which depends on various factors mentioned below:
- Metal composition
- Metal temperature
- The extent of deformations to the crystal structure
- Metal grain size
- Metal crystalline form
- Flaw size
Refer to Fig. 2 below that represents fracture initiation curves for steel for various flaw sizes at various stresses and temperatures.
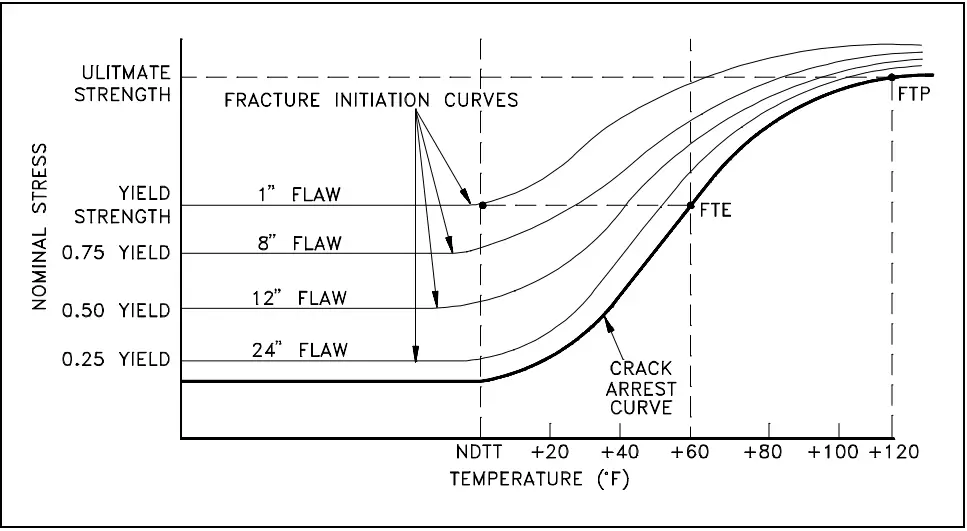
From the above curve, it is evident that to avoid brittle fracture operating temperature should be maintained above NDT temperature. Maintaining the operating temperature above FTE temperature (NDT + 60°F for steel) will ensure greater safety.
Griffith’s Theory of Brittle Fracture
Consider a thin plate of length l having a thru-crack of length 2c, as shown in Fig 3. The upper curve shows the force-deflection curve for a non-extending crack of length 2c. For a non-extending crack of length 2(c + Δc), the curve will be the lower curve. The area between these two curves represents the energy released to extend the crack from 2c to 2(c + Δc).
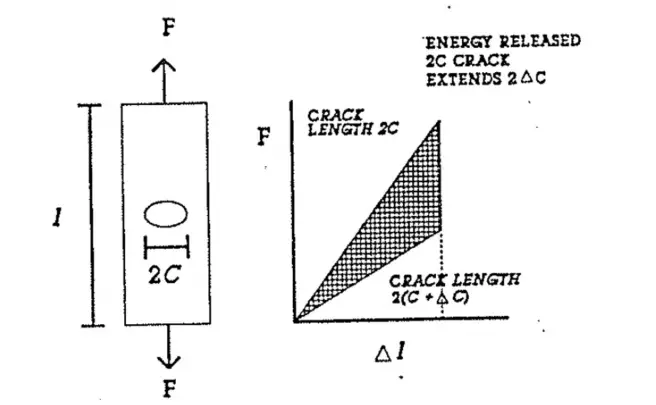
Using elasticity theory Griffith showed that the energy released per unit thickness during a crack growth of 2Δc is

Thus, the critical stress is inversely proportional to c½. Hence, the smaller the flaw, the greater the value of σc. The Griffith theory is good for every brittle material like glass, in which failure occurs without any plastic deformation. When there is some plastic deformation associated with
the crack extension, we must add the plastic work γp expended in making the surface to the surface energy term γs to obtain σc as shown below:
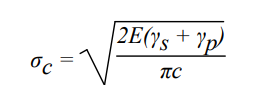
The above equation forms the starting point of modern fracture mechanics.
Mechanism of Ductile Fracture
Ductile fracture or ductile failure (Fig. 4) normally occurs following the below-mentioned steps:
(a) Necking
(b) Formation of microvoids
(c) Coalescence of microvoids to form a crack
(d) Crack propagation by shear deformation
(e) Fracture
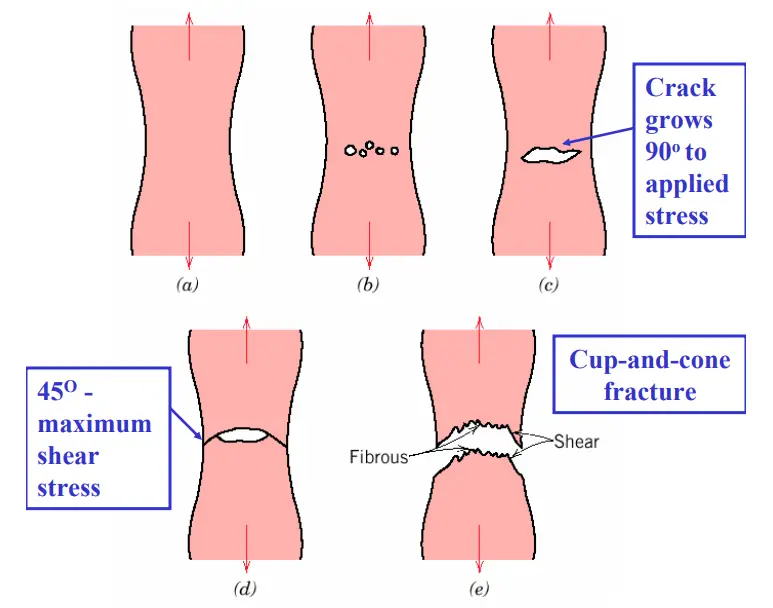
Brittle Fracture vs Ductile Fracture
From the above discussions, it is clear that the brittle fracture and ductile fracture mechanism is completely different. The major differences between brittle and ductile fracture are provided below:
Brittle Fracture / Brittle Failure | Ductile Fracture / Ductile Failure |
Negligible plastic deformation | Considerable plastic deformation. |
Rapid and Quick Failure without any warning | Slow process with sufficient warnings |
Quick Crack propagation | Slow crack propagation |
Brittle fracture can occur below the yield strength | Ductile Failure normally occurs above yield strength. |
In brittle fractures, the crack propagation is perpendicular to the applied stress. | Crack propagation is at 45 Degrees to the applied stress. |
Cleavage failure | Cup cone failure |
Less energy requirement to failure | The energy required to fail is substantially high |
It May Break into several pieces | Broke into two pieces |
I really like your website, I have to say that all info that you are present it’s really useful.
Zoran Tunic Piping Material Corrosion Engineer.
Very well explanation Anup.
Thanks for sharing.
Yes I have read completely its good work
Nice explanation
Overall very useful and concise, however I disagree with the statement that smaller grain size increases ductility, I believe it should increase toughness. Grain boundaries should interfere with dislocation movement within the grains.
Toughness is strength and ductility… So as smaller grain size increases ductility, it as well increases the toughness of the material.