The application of composite structures starts in 1500 B.C., and their notable developments date back to 1940[1] here GFRPs were used to replace the traditional wood or metal structures in the marine industry. This application is mainly due to its corrosion-resistant properties, high stiffness-to-weight ratio, and increased fatigue life. These features have increased the value of GFRP, making it the primary consideration for the construction of boats, vessels, and ships. Besides this industry, other critical industries such as aerospace, defense, automotive, and petroleum expect an increased demand. Advanced composite materials were primarily developed for aerospace to enhance commercial and military aircraft[2]. The materials are still contributing a notable role in the current and potential future aerospace components. Presently, the Airbus A350 XWB and its American counterpart, the Boeing 787 Dreamliner, are constructed of more than 50% composite materials [3].
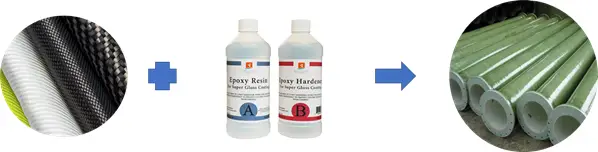
Composition of Composite Piping System
The Fiber-Reinforced Polymer (FRP) is fundamentally developed from three important raw materials namely:
- Fiber system: Natural (Basalt, Cotton, Flax, etc) or Synthetic (Glass, Carbon, Kevlar, etc).
- Matrix/Resin system: Epoxy, Vinylester, Polyester, etc.
- Hardener system: Aliphatic Amine, Aromatic Amine, Anhydride, etc.
Fabrication of Composite Piping System
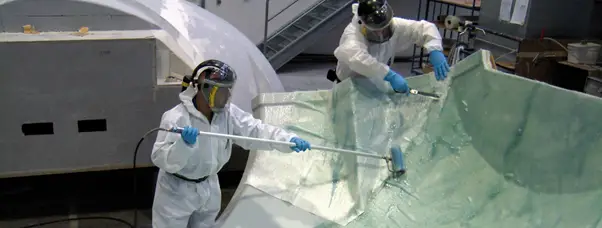
To fabricate FRP, hand layup is a well-known technique and has been used since the beginning of a composite structure. Despite the more flexible design and easy application, it is not suited for cylindrical FRP structures such as piping, pipeline, tubing, casing as well as a pressure vessel. Hence, a more optimized fabrication method is introduced namely filament winding. This method is either fully or semi-automated depending on the design of cylindrical structures.
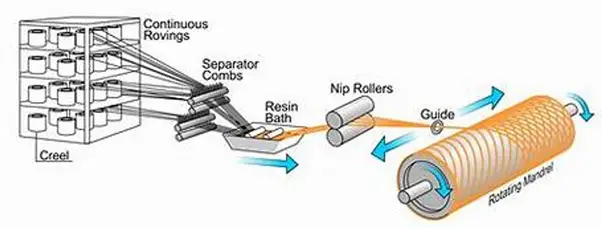
Filament wound composite tubes are widely used in the aerospace, automotive, marine, construction, and sporting industries. In general, fiber reinforcements in composite materials are used to enhance mechanical properties and environmental resistance when subjected to harsh conditions. Commercial synthetic continuous fibers such as carbon and E-glass made the composite tubes increasingly popular [1-4]. The carbon and glass fibers as reinforcements in composites have outstanding mechanical and thermal properties as well as durability. Though, the most common fiber reinforcement in resin, GFRP, has been widely used in the structural replacement or retrofitting of steel parts in recent years due to its excellent mechanical properties and chemical stability[4-6]. GFRP structures can withstand the hydrostatic forces by positioning the fibers in the tangential direction to increase the hoop strength, making the GFRP tubular structures anisotropically stronger than their metal counterparts. Nevertheless, CFRP is comparatively more costly than other types of FRPs. In order to reduce the cost of the material, thick GFRP is used to replace it [7, 8]. GFRP piping system is a more cost-effective alternative to corrosion-prone metallic piping and non-reinforced thermoplastics. The advancement of composite materials and complete acceptance of their application as a temporary repair mechanism can attribute to the pulling factors of using it as an alternative product to metal.
The increased application of composite materials drives a significant amount of research activities, particularly in the mechanics of composite and the prediction of failure under a range of loading conditions. Due to deterioration, especially without proper control and mitigation regimes, most metallic structures will require repair and maintenance within the service life. This issue will cause a series of unnecessary asset shutdowns that will affect the other equipment integrity and increase operating expenditure.
Advantages of Composite Piping System
The advantages of GFRP include the elimination of corrosion and corrosion-related costs. It has superior corrosion resistance compared to conventional carbon steel and removes the need for expensive mitigation requirements such as corrosion inhibitors and cathodic protection. Furthermore, it requires zero maintenance and inspection. Inspection costs for intelligent pigging and/or inspection to monitor carbon steel piping corrosion can be saved when applying GFFP systems. For firewater lines, sprinklers, and deluge systems, the internal corrosion of traditional piping like carbon steel can lead to blockage of the firewater sprinkler that compromises the system’s safe operation. Also, the GFRP system does not need external coatings for buried pipelines. For aboveground piping, an integrated U.V. stabilization package avoids the use of external coatings.
Moreover, it has a superior fluid flow performance due to greater internal diameter and no scaling and bore restriction issues. GFRP reduces pumping costs compared to carbon steel of the same nominal diameter due to the low friction, which exhibits low-pressure loss. Apart from this, the main reason for their popularity are the outstanding weight-specific stiffness and strength values which enable lighter structures and hence reduced energy consumption and suited for retrofit application in marine vessels. . It has a lower weight than steel counterparts; hence, the lower weight results in more straightforward and more cost-effective pipe handling. For offshore structures, weight-saving is crucial to limit total structure weight and reduce the required structural footprint. Lower weight promotes easier handling, reducing the need for lifting equipment, which reduces lifecycle and installation costs. However, these benefits are gained with higher material costs. By replacing the metallic piping system in the marine and offshore assets, the lower assembly costs can counterbalance the higher costs for the material.
Metallic vs Composite Piping System
Despite the advantages, fiberglass products have a number of complicating factors compared to those familiar with metal pipes. The properties of the material are different for the hoop and the axial direction, and the properties vary because they can be customized for each specific application. The anisotropic behavior of the materials is more difficult to design relative to its isotropic metallic counterpart. Efficient research philosophy in the design and fabrication will result in outstanding quality and performance of FRP piping systems which require no maintenance throughout the design life. As opposed to the metallic piping product, which is relatively easier to design and fabricate, more efforts are needed throughout the design life to tackle the corrosion issue, routine maintenance, asset shutdown, and risk of failure.
Few more related articles.
Overview of GRP Pipes
An Article on HYDROSTATIC FIELD TEST of GRP / GRE lines
Stress Analysis of GRP / GRE / FRP piping system using Caesar II
Basic Principles for an aboveground GRP piping system
Buried GRP/FRP pipe Laying and Installation Procedure
Stress Analysis of GRP / GRE / FRP Piping using START-PROF
References:
- [1] W. G. Roeseler, B. Sarh, M. U. Kismarton, J. Quinlivan, J. Sutter, and D. Roberts, “Composite structures: the first 100 years,” in 16th International Conference on Composite Materials, 2007, pp. 1-41: Japan Society for Composite Materials Kyoto, Japan.
- [2] C. Soutis, “Fiber-reinforced composites in aircraft construction,” Progress in Aerospace Sciences, vol. 41, no. 2, pp. 143-151, 2005/02/01/ 2005.
- [3] P. A. Toensmeier, “Advanced composites soar to new heights in Boeing 787,” Plastics Engineering, vol. 61, no. 8, pp. 8-8, 2005.
- [4] J. Cadei, T. Stratford, L. Hollaway, and W. Dcukett, Strengthening metallic structures using externally bonded fiber-reinforced polymers. Ciria, 2004.
- [5] X.-L. Zhao and L. Zhang, “State-of-the-art review on FRP strengthened steel structures,” Engineering Structures, vol. 29, no. 8, pp. 1808-1823, 2007/08/01/ 2007.
- [6] D. Schnerch, M. Dawood, S. Rizkalla, and E. Sumner, “Proposed design guidelines for the strengthening of steel bridges with FRP materials,” Construction and Building Materials, vol. 21, no. 5, pp. 1001-1010, 2007/05/01/ 2007.
- [7] A. A. El Damatty, M. Abushagur, and M. A. Youssef, “Rehabilitation of Composite Steel Bridges Using GFRP Plates,” Applied Composite Materials, vol. 12, no. 5, pp. 309-325, 2005/09/01 2005. [8] R. Rameshni, “Innovative hybrid FRP/steel splice details for modular bridge expansion joints,” 2011.