Cryogenic piping refers to the piping network that operates below -290C. This temperature represents the demarcation of embrittlement for carbon steel materials. However, various literature considers the piping systems operating below -1500C (-3000F) as cryogenic piping systems in the true sense. Industrial processing and transportation of propane, butane (LPG), methane (LNG), ethylene, nitrogen, ammonia, oxygen, etc. require the extensive use of a cryogenic piping system. These piping systems must be designed with special care to work in such low temperatures. In this article, we will explore more details about cryogenic piping.
Properties of Common Cryogenic Materials
Cryogenic materials are odorless, tasteless, and colorless when vaporized. Cryogenic liquids need to be carefully handled as they may cause skin burns and frostbite. Table-1 below lists the liquid temperatures and the liquid-to-gas expansion ratio of some of the common cryogenic materials:
Cryogenic Material | Liquid Temperature (0C) | Liquid-to-gas volume expansion ratio |
Oxygen | -183 | 1: 860 |
Nitrogen | -196 | 1: 696 |
Methane | -162 | 1: 579 |
Helium | -269 | 1: 757 |
Argon | -186 | 1: 847 |
Hydrogen | -253 | 1: 851 |
Fluorine | -187 | 1: 888 |
Why is Cryogenic Piping Challenging?
As the temperature gets extremely low during the operating condition, the material of the pipe faces different types of corrosion and deterioration issues as the chemical and physical properties of the material change. Normal piping systems can’t hold the processing gas in the form of liquid. Also, as can be seen from Table 1, cryogenic liquids generate a large volume of gases when vaporized. So, if they vaporize inside a sealed container, the container can burst due to the enormous pressure. As a result, this cryogenic piping requires a special type of materials, supports, and valves different than that of normal piping systems which makes the design of cryogenic piping systems highly critical and challenging. Some of the cryogenic piping system requirements are:
- Sufficient flexibility as with lower temperatures the material contracts creating huge thermal stresses which must be compensated using proper flexibility.
- All cryogenic lines are insulated to avoid heat gain from the environment and for safety. All these increase the weight of the pipe making the cryogenic systems more rigid.
- Specially designed long-stem, extended bonnet valves are used as Cryogenic Valves.
- The use of costly materials increases the project cost. So, every chance of optimization shall be used to minimize the project cost.
Cryogenic Piping Materials
With a decrease in temperature, materials become brittle, and impact test requirement as per code arises. Various parameters need to be considered for selecting cryogenic piping materials like
- Suitability for different fabrication techniques
- Corrosion resistance
- Resistance to oxidation and sulfidation
- Strength & ductility
- Suitable for the cleaning process
- Toughness, resistance to abrasion, erosion, galling, and sizing.
- Physical property characteristics
- Rigidity
- Impact Resistance, etc
Materials that have established themselves as suitable cryogenic piping materials are provided in Table 2 below:
Ferrous Materials | |
Cryogenic Piping Material | Lowest Temperature (0C) for Application |
SA-333 Grade 1 | -46 |
SA-333 Grade 7 | -73 |
SA-333 Grade 3 | -101 |
SA-333 Grade 8 | -196 |
Austenitic Stainless Steel (Grade 304, 304L, 321, 347) | -254 |
Austenitic Stainless Steel (Grade 316, 316L, 316 Ti, 316 Nb) | -196 |
Non-Ferrous Cryogenic Pipe Materials | |
Aluminum Alloy (1100, 3003, 5052, 5083, 6061, 5086) | -254 |
Copper Alloy (C10200/C12200), Copper Nickel Alloy (70600, C71500) | -198 |
Monel 400 | -198 |
Several non-metallic materials like Grafoil, Mineral wool, Fiberglass, Polyurethane, Styrofoam, Perlite, Viton, Glass reinforced Teflon, etc serve as various components in cryogenic piping applications.
Cryogenic Piping Standards and Cryogenic Piping Design Guide
ASME B31.3 is the main governing standard for designing cryogenic piping systems. The usual cryogenic piping design considerations are:
- Pipe Sizing is done using normal pressure drop criteria. A drop in pressure can create flashing of part of the liquid which may result in a two-phase flow. So, if a similar situation arises, the two-phase flow must be considered for sizing. However, for oxygen gas piping, the fluid velocity is also considered during pipe sizing.
- As the ambient temperature is hotter than the cryogenic liquid temperatures, there will be continuous heat leaks to the cryogenic pipeline and piping system which must be considered during the design.
- Extended stem valves are used to keep the operator at ambient temperature.
Cryogenic Piping Insulation
All frequent-use cryogenic piping and pipeline systems are insulated using any one of the following cryogenic insulation types:
- Expanded foams (For example, Foam glass, polyurethane)
- Powder Insulation (Example, Perlite)
- Vacuum Insulation
- Evacuated powder & fibrous insulation
- Opacified powder insulation
The main aim of the cryogenic piping insulation system is to create a vapor barrier to keep atmospheric moisture from leaking into the insulation space. This moisture permeates insulation and then condenses. Which significantly increases the corrosion changes in the lines. Also, build-up of water or ice may occur which in turn, results in lowered performance. Whenever the insulation has been compromised, the thermal efficiency is lost and energy consumption increases. So, high energy consumption can be reduced by using adequate insulation materials. the vapor barrier system must keep atmospheric moisture from entering the insulation space and freezing against the cryogenic lines.
Whenever a cold system is required, the entire system shall be fully insulated including the piping components, piping/tubing of instead instruments, drains, equipment nozzle, and supports. Cryogenic insulation is applied in multiple layers.
Cryogenic Piping Supports
As a matter of their extremely low temperature, extremely superior insulation properties, durability, and stable function are required for cryogenic pipe supporting devices. While designing the cryogenic supports we have to consider structural characteristics, design load, other requirements, and economical aspects for each shoe, guide, stop, and trunnion. We must clarify the behavior of cryogenic piping including pipe support, during normal operation they should also take warm-up and cool-down conditions into account. There are problems encountered in the system such as higher displacement due to the thermal expansion and contraction, pipe insulation, embrittlement of materials, icing around or between the supports, and rapid changes of phase due to large heat fluxes.
Cryogenic Pipe Supports shall meet the following requirements.
- Lighter weight
- High reliability in water & resistance to oil and corrosion
- High weather tightness
- They must have physical strength against compression, bending, and shearing
- Suitable for mass production
- Low water absorption
- Heat and flame resistance
- Must incorporate a molded heavy-density layer bonded with stainless steel.
Cold insulation supports are usually made from:
- High-Density polyurethane foam
- Phenolic foam insulation
- Polyisocyanurate or PIR
Supports shall meet the design requirements in respect of compressive strength under sustained load, thermal conductivity, coefficient of friction, service temperature, and flammability. Even considering the unexpected thermal bowing and fluctuations of flow rate pipe, the support span for cryogenic piping shall be much shorter than that of hot insulated piping, support shall be immediately adjacent to any change in direction of piping.
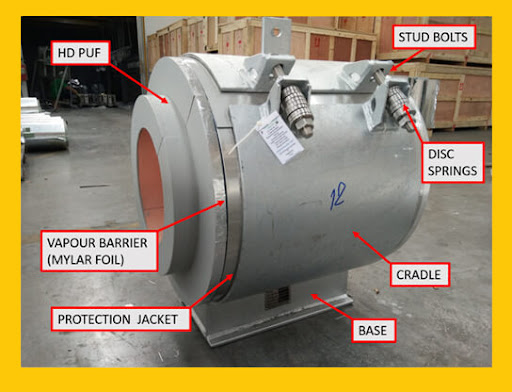
Cryogenic supports will be equipped with advanced temperature-resistant technology that protects pipes in extreme cold. Cold climates are critical for pipe supports they aren’t built to withstand the elements. Worse yet, pipes are fragile in frigid environments, and ice formation can wear down both pipes and supports, also must be designed to support pipes in temperatures as low as -320°F. They will encapsulate the fragile insulation used in these piping systems.
To stop the thermal transfer from the interior of pipes to surrounding structures they must be nonconductive. Foam-insulated cores are given to some shoes to naturally keep pipes from sudden temperature changes of heat transfer. By keeping heat inside pipes, can save energy and stop the ice formation that can destroy pipes. A cold shoe is a support used for cryogenic applications where the heat transferred to the surface is not relevant and can be used for temperatures right down to -300˚ Fahrenheit.
Cryogenic Piping Stress Analysis
Cryogenic pipelines are a special case where the operating temperature used is extremely lower than the installed ambient temperatures. There should be a degree of rigor that is relevant for the safety of operations and potential hazards and therefore accurate flexibility analysis is very important to manage thermal forces, stresses, and displacements. Some of the Cryogenic piping stress analysis considerations are provided below:
- Cryogenic piping systems may have a thermal-bowing effect. So it must be considered. Click here to know more about the use of pipe thermal bowing effect.
- If it’s vacuum-insulated piping the two pipes having different displacements are to be considered and connected. The main pipe which is at cryogenic temperature contracts and the jacketed pipe usually at a temperature bit above ambient expands.
- Equipment nozzle loads are usually qualified using Finite Element Analysis or FEA.
- Expansion bellow or Flexible hoses may be required in the analysis.
- Cryogenic pipe systems behave completely opposite to high-temperature piping systems. Due to the contraction of the cryogenic piping system, the supports that are usually lifted off in high-temperature piping carry the load in cryogenic-temperature piping.
LNG Piping and Cold Box Piping systems are typical examples of cryogenic piping systems.
This post will be very useful to us. I like your blog and helpful to me. nice thoughts for your great work.
Good starter for cryogenic piping.
PLEASE PROVIDE A BRIEF ABOUT COLD BOX.
This is really an awesome article. Thank you for sharing this.It is worth reading for everyone.
It is very informative post. Thanks for sharing…
A pretty good article to get basic understanding of cryogenic piping. Do you have any knowledge regarding Super Insulation (MLI)?