What is Induction Bending?
Induction Bending is a precisely controlled and efficient piping bending technique. Local heating using high-frequency induced electrical power is applied during the induction bending process. Pipes, tubes, and even structural shapes (channels, W & H sections) can be bent efficiently in an induction bending machine. Induction bending is also known as hot bending, incremental bending, or high-frequency bending. For bigger pipe diameters, when cold bending methods are limited, Induction bending of pipe is the most preferable option. Around the pipe to be bent, an induction coil is placed that heats the pipe circumference in the range of 850 – 1100 degrees Celsius.
Induction Bending (Hot Bending) Process
The following steps are performed for the induction bending of the pipe or pipeline system:
- The pre-inspected pipe or pipeline to be bent is placed in the machine bed and clamped hydraulically.
- Around the pipe, induction heating coils and cooling coils are mounted. To ensure uniform heating, the induction coil can be adjusted with a 3-plane movement.
- By adjusting the radius arm and front clamp, the required bend radius can be fixed. There is one pointer to display the correct degree of turning.
- Arc lengths are marked on the pipe. The pipe can be moved slowly whilst the bending force is applied by a fixed radius arm arrangement.
- Once everything is set as required, hydraulic pressure, water level, and switches are inspected and then the induction bending operation is started.
- Upon reaching the required temperature range, the pipe is pushed forward slowly at a speed of 10-40 mm/min, and the operation is stopped when the specified bend angle and pre-determined arc length are reached.
- Just beyond the induction coil, the heated pipe material is quenched using a water spray on the outside surface of the pipe.
- In the next step, the induction bend is removed and sent for inspection and measurement of tolerances.
- The final step for the induction bends is the use of post-bend heat treatments for stress relieving, normalizing, etc.
Fig. 1 below shows a typical induction bending process.
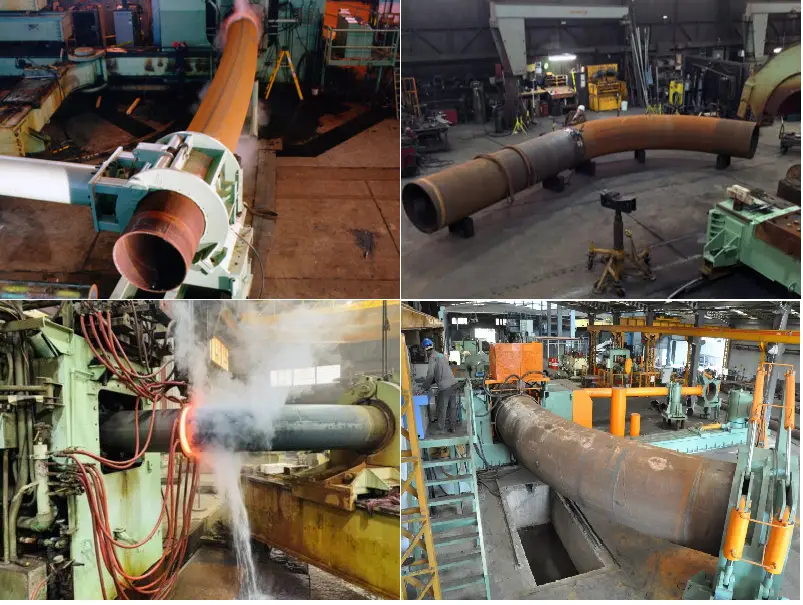
Induction bends are normally produced in standard bend angles (e.g. 45°, 90°, etc.). However, depending on the requirement they can be custom-made to specific bend angles. Compound out-of-plane bends in a single joint of pipe can also be produced. The bend radius for induction bending is specified as a function of the nominal pipe diameter (D) like 5D, 30D, 60D bends, etc. Fig. 2 below provides a schematic diagram of the induction bending mechanism.
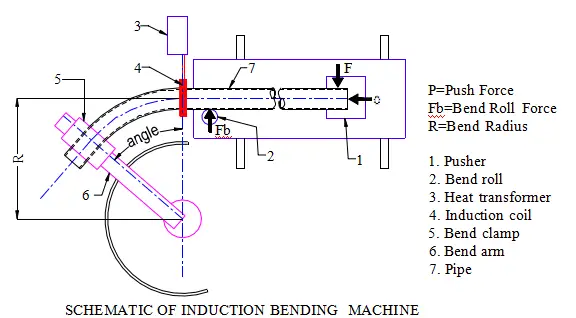
The important parameters that affect the induction bending process are:
- Pipe Diameter
- Surface Contamination
- Process Parameters like Temperature, Speed, Cooling rate, etc
- Bend Radius
- Bend Angle
- Process Interruptions
- Hardenability of the Pipe Material, etc.
Induction Bending Standards
As the complex induction bending process involves various steps for producing bends, it must be controlled precisely to produce quality items. Different codes and standards govern this process. The most conventional and widely used standards for induction bends are the
- ASME B16.49
- ISO 15590-1(en)
- Shell DEP 31.40.20.33
Advantages of Induction bending
The major advantages of induction bending are:
- Lower risk of wall thinning and deformation of the cross-section
- Thin-walled pipes can easily be bent.
- Less costly and available faster than traditional components.
- Uniform hardness and thickness.
- Smooth flow due to large radii reducing friction, wear, and pump energy.
- No pipe wrinkles.
- Only a straight pipe is required for induction bending.
- Precise bending radius and angle.
- Diverse bendings: square pipe, flat bar, I-beam, H-beam, channel section, etc.
Applications of Induction bends
The majority of the Induction bends are found in the pipeline systems for liquid and gas transportation. Additionally, they are found in applications requiring large diameter bends with precision and reliability and where the laminar smooth flow is required. Typical applications of induction bends include the following industries:
- Onshore and Offshore pipelines in the oil & gas sector
- The refinery, chemical, and petrochemical sector
- Powerplants
- Industrial equipment
- Infrastructure constructions and steel building constructions (a.o. bridges, construction, art objects, roller coasters)
- Offshore energy (a.o. J-tubes, S-jubes)
- Metallurgical industries
- Shipbuilding, etc.
Induction Bending Materials
The following pipe materials are normally used for forming by induction bending:
- Carbon steel
- Stainless steel, Duplex Stainless Steel, Super Duplex Stainless Steel
- Special steels, such as Inconel, S690QL, etc.
- Aluminum, Titanium, Monel, Copper, Clad Pipe, etc.
Induction (Hot) Bending vs. Cold Bending
The main differences between Induction bending or Hot bending and Cold Bending are listed below in a tabular format:
Induction Bending / Hot Bending | Cold Bending |
Heat Input is a must in induction or hot bending | Cold Bend does not need any added heat. |
Hot bending is a Slow Process | Cold bending is a Fast Process as no heating & cooling is involved |
Better control is achieved in Hot bending. | Cold bending does not provide precise control. |
Highly efficient complex types of machinery are used for hot bending. | The cold bending process uses Simple machines. |
The hot bending Process is efficient for larger pipe diameters | Not suitable for large pipe diameters. Cold bending is limited to smaller-diameter piping only. |
Induction bending is a Costly process | Cold bending is not expensive. |
In Hot bending usually no wrinkling on the pipe surface. | The is a High probability of wrinkling on the pipe surface during cold bending. |
The required force in hot bending is normally less. | The physical Force requirement in cold bending is comparatively more |
To get some more insight about hot bending and cold bending you can click here.
Sir: your knowledge is very informative and detailing is simple and intersting to the readers. Thankyou for sharing the knowledge and experience with netigens
you can achieve desired change of direction in small space in hot bending. Cold bending requires longer space as the angle changes gradually
ASEM B16.49 explicitly states induction bend made of carbon steel pipe.
What shall be standard guideline for induction bend made of Stainless steel?