LPG (Liquefied Petroleum Gas) storage tanks or LPG Tanks are containers designed to store large quantities of propane or butane, which are commonly used as a source of fuel for heating and cooking in both residential and industrial applications. They are safe and efficient. LPG tanks are typically made of steel or another durable material that can withstand the high pressure and low temperatures required to store LPG in its liquid form. LPG is liquefied to maximize its storage efficiency inside the LPG Tanks.
LPG storage tanks come in various sizes, from small cylinders used for portable stoves and heaters to large tanks used for industrial purposes, such as powering forklifts and other heavy equipment. The capacity of LPG storage tanks can range from a few hundred liters to several thousand liters, depending on the specific application and the amount of LPG needed.
LPG tanks can be used in the form of LPG cylinders, LPG bulk tanks, Underground LPG storage tanks, etc. Flat-bottom cryogenic storage tanks are one variation of the most efficient LPG storage facility, having a capacity in the range of 1,000 to 30,000 m³.
LPG storage tanks must be designed and installed in compliance with strict safety regulations to prevent accidents and leaks. This includes regular inspection and maintenance to ensure that the tank is in good working condition and that any potential issues are addressed promptly.
Types of LPG Storage Tanks
There are several types of LPG storage tanks, each designed for specific applications and with varying capacities. Some of the most common types of LPG storage tanks include:
- Aboveground LPG storage tanks: These are large tanks that are installed above the ground and are typically used for storing LPG in bulk for commercial and industrial applications.
- Underground LPG storage tanks: These tanks are installed underground and are commonly used for storing LPG in residential areas where space is limited.
- Horizontal LPG storage tanks: These tanks are designed to be installed horizontally and are commonly used for storing LPG in industrial settings.
- Vertical LPG storage tanks: These tanks are designed to be installed vertically and are commonly used for storing LPG in residential areas and small commercial settings.
- Mounded LPG storage tanks: These tanks are installed on a concrete platform or mound and are commonly used for storing LPG in industrial settings.
- Propane cylinders: These are small portable tanks used for storing LPG for outdoor cooking and camping.
- Cylindrical Storage Tanks
- Spherical Storage Tanks
Each type of LPG storage tank has its own advantages and disadvantages, and the choice of the tank will depend on the specific application and the amount of LPG needed. Proper installation and maintenance are critical for ensuring the safe operation of LPG storage tanks.
Spherical or horizontal cylindrical type (bullet type) storage tanks are generally used to store LPG. The horizontal cylindrical types are usually used for small-capacity or underground installations and Spherical ones are used for higher capacities. The design of high-pressure LPG storage tanks is critical. Many parameters need to be considered during design. This article will provide basic information about the same.
Selection of LPG Storage Tank Types
A tank type will usually be selected considering the cost or the size of transportation. The spherical type is usually employed for sizes greater than 500 m3. The horizontal cylindrical type is usually used for sizes smaller than 100 m3. Both types will be applicable for volumes ranging from 100 to 500 m3. The type of this capacity range will be decided by the total weight. Where the tank is installed underground, the horizontal type shall be selected, even if the vessel capacity exceeds 100 m3.
LPG Storage Capacity
Definition of Capacity
- Nominal capacity- All this capacity can be used, defined as below in Fig. 1. This capacity is usually used as a tank name.
- Geometrical capacity- Volume inside a vessel which is called “a water volume” in NFPA.
- Storage capacity- The volume from the tank bottom to the maximum design level. This volume varies depending on the operating temperature.
- Net Working capacity- Volume between HLL and LLL or HHLL and LLLL
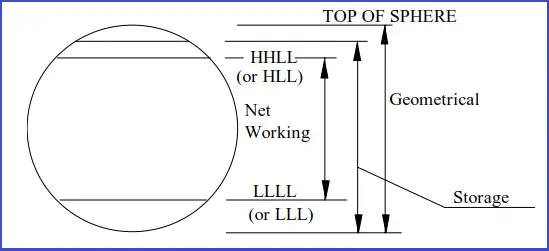
LPG Liquid Level
(1) Maximum liquid level (maximum Storage Capacity)
Many countries specify a maximum LPG liquid level (max. storage capacity) in their regulations. In countries that have no such regulations, NFPA shall be applied. NFPA-58 and 59 specify details of the maximum liquid level including liquid volume correction factors and equations concerning capacity and temperature (Refer to NFPA 58 Para. 4-4 and Appendix-F)
Few regulations specify that a vapor space of 10% shall be secured under the severest conditions, thus resulting in the following equation.
V = W/0.9d
Where V = tank geometrical volume (m3); W = Storage capacity (kg) and d = Density at the maximum design temperature (kg/m3)
NFPA specifies the coefficient of the above equation, i.e. 0.9 as follows.
- 9 to 0.95 at 100° F
- 98 to 0.99 at the maximum storage temperature.
This maximum liquid level fluctuates according to operating temperatures as below Example ;
The following figures are the results of example calculations according to the physical properties of Pure Propane per NFPA.
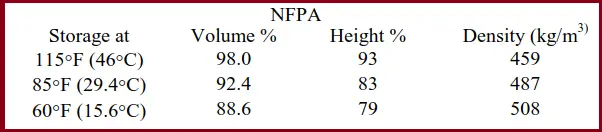
From the above, it is not possible to set a fixed level for the highest limit point. Therefore the highest limit of level should be compensated with the storage temperature or a differential pressure type level indicator shall be used.
(2) Minimum LPG levels
Refer to Fig. 2
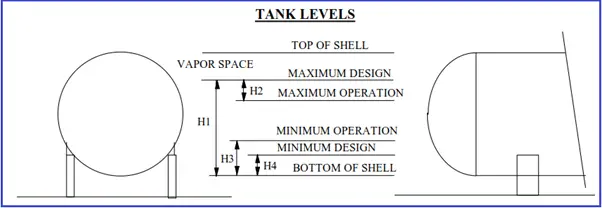
H2; 150 mm or 10 minutes from the maximum filling volume
H3; A height of the Deadstock area. The height shall be calculated by the reasonable dead stock volume.
The recommended height for the spherical tank is shown below.
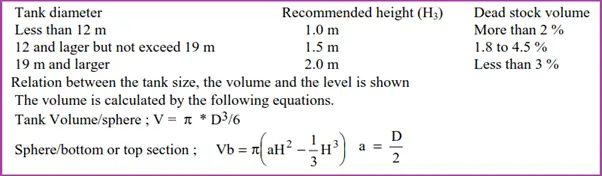
Where ;
- D: Diameter of the sphere
- H: Height of level
- V: Sphere volume
- Vb: Sectional Volume of the height H
- H4: 300 mm/ minimum 100 mm
Note 1; High and low-level (HLL and LLL) alarms shall be set at the maximum and the minimum operation respectively. If high-high and low-low levels (HHL and LLL) for an emergency shutdown or an automatic diversion system are provided, set points shall be selected at lower than the maximum and higher than the minimum design, but not inside of the maximum and the minimum operation.
Sphere Maximum Capacity
The maximum sphere capacity is limited due to the wall thickness. The wall thickness is limited by the manufacturing and the stress relief requirement.
Operating and Design Conditions
Operating Conditions
(1) Operating temperature: Operating temperatures are not so important for the design of tanks; they are merely used to design pumps connected to tanks. The maximum operating temperature and minimum operating temperature as pump design bases shall be determined separately. The operating temperature of a tank shall be determined based on the following conditions.
- The temperature of rundown from process units
- Ambient air temperature (annual mean or annual highest mean temperature)
- The temperature of products when they are received from a tanker.
(2) Operating Pressure: An operating pressure shall be an equilibrium pressure at operating temperature. Where the mole fraction of contents of the liquid in the tank fluctuates, the most severe case in normal operation shall be considered.
Design Conditions
(1) Design Temperature: A design temperature shall be determined based on the assumed highest temperature, with consideration given to input heat generated by solar radiation. Generally, design temperatures are specified per country based on the ambient air conditions of the district where the plant facilities are to be constructed. Major oil companies may have their own design standard for temperature selection. Where the country’s regulations or the client’s design standards do not specify design temperatures, NFPA shall be applied. Design temperature determination standards are closely connected with design pressures.
Major oil companies, in some cases, have specified the lowest design temperature as a design standard; they employ the equilibrium temperature of a tank internal at atmospheric pressure as the lowest design temperature. Low-temperature service materials, therefore, shall be used for tanks storing propane or lighter fluids.
(2) Design Pressure: The equilibrium pressure of a tank internal at the design temperature shall be used as the tank design pressure. Where the country’s regulations or the client’s design standards do not specify a design temperature, NFPA shall be applied as per the table below. Some major oil companies specify a higher temperature e.g. 65° C to be a mechanical design temperature, in their standards. In this case, however, they do not employ the equilibrium pressure of the internal at the specified temperature as design pressure, but the design pressure will be specified separately or the minimum design pressure specified in NFPA is otherwise used.
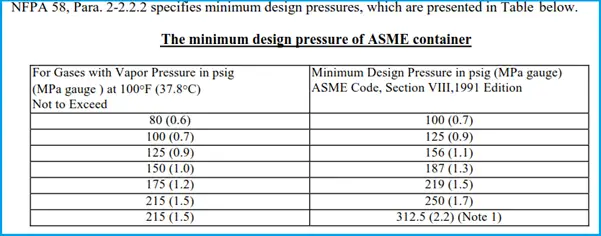
Note 1: Refer to NFPA 58, Para. 8-2.2
The NFPA specifies the equilibrium pressure at a design temperature of 41, 46, and 54° C, respectively, to be a design pressure, for each type of vessel as given below.
- Vessels up to 4.5 m3 incl. in-capacity (54°C)
- Vessels over 4.5 m3 in capacity (46°C)
- Underground vessels (41°C)
LPG Storage Tank Nozzles
(1) Tank nozzle information to be provided by basic engineering. The following items of nozzle information shall be provided by the basic design group.
- Size, number, and location of inlet and outlet nozzles. Note: The pump suction nozzle shall be inserted 300 mm from the tank bottom.
- Size, number, and location of the sampling nozzle(s) and water draw-off nozzle, if required
- Size and number of the spare nozzle(s), if required
- Size and number of the vent and drain nozzle. A minimum of one vent and drain nozzle shall be provided.
- Size and number of nozzles for safety relief valves. A minimum of one spare PSV shall be provided.
(2) Nozzle for instrumentation
Nozzle information for instrumentation will be provided by others.
(3) Nozzles to be decided by the detailed engineering group
The Instrumentation on LPG Storage Tanks
Level
Generally, two-level instruments will be installed to permit mutual calibration to be carried out, because LPG tanks cannot open without the tank shut down. One level instrument may be permitted if it is possible to remove and calibrate it by installing an isolation valve such as a radar type. To use the LPG tank capacity as effectively as possible, it is necessary to compensate the level with a temperature instrument or use a differential pressure type level instrument
Temperature
Generally, a temperature indicator shall be installed at the bottom crown
Pressure
Generally, two pressure gauges should be provided at the sphere’s top and bottom. One pressure instrument should be provided and indicated in the control room. Two pressure relief valves, each having a 100% capacity shall be provided. This configuration allows PRV maintenance without a sphere shutdown.
Water Drain
A Water draws offline shall be installed on each LPG tank. Two isolation valves shall be provided on the water draw offline: a distance of more than one meter shall be provided between the valves to prevent freezing the valves as figures below. As an alternative system, a water draw-off pot is provided, and the vent line from the water pot is returned to the flare line or the LPG tank.
Others
Insulation and Painting: For aboveground tanks, in some cases, cold insulation or fire protection may be provided, according to the client’s request. In such a case, it is possible to reduce the safety valve relieving capacity.
Tank Heaters or Coolers: A tank heater or cooler shall not be installed in the tank. However, an external heater may be required in the coldest areas, i.e. North East of China or Siberia, to avoid a vacuum in the tank.
Work Flow of LPG Storage Tank Basic Design
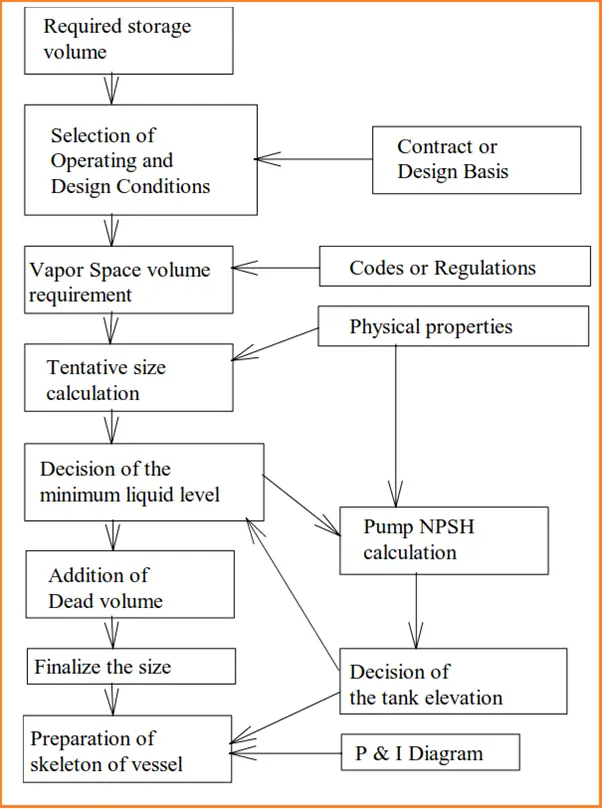
Codes and Standards for LPG Storage Tanks
There are several codes and standards that apply to the design, construction, installation, and operation of LPG storage tanks. These codes and standards are designed to ensure that the tanks are safe and reliable and that they comply with regulatory requirements.
Here are some of the key codes and standards that apply to LPG storage tanks:
- NFPA 58: This is the National Fire Protection Association’s standard for the storage and handling of Liquefied Petroleum Gases (LPG). It provides requirements for the design, construction, installation, and maintenance of LPG storage tanks, as well as guidelines for emergency procedures and training.
- ASME Boiler and Pressure Vessel Code: This code provides rules for the design, fabrication, and inspection of pressure vessels, including LPG storage tanks. It covers a wide range of factors, such as materials, pressure ratings, welds, and nondestructive examination.
- API 2510: This is the American Petroleum Institute’s recommended practice for the design and construction of LPG storage facilities. It provides guidance on the selection of tank materials, tank size, and tank location, as well as requirements for tank foundations, piping systems, and safety equipment.
- DOT Regulations: The US Department of Transportation (DOT) has regulations that govern the transportation of hazardous materials, including LPG. These regulations cover the design, construction, and testing of LPG cylinders, as well as requirements for labeling, marking, and documentation.
- State and Local Regulations: In addition to federal regulations, there may be state and local regulations that apply to the installation and operation of LPG storage tanks. These regulations can vary widely depending on the location, so it is important to consult with local authorities and experts in the field.
By following these codes and standards, LPG storage tanks can be designed, installed, and operated safely and efficiently, with minimal risk to people and the environment.
Materials for LPG Storage Tanks
LPG storage tanks can be made from a variety of materials, depending on the specific requirements of the application. Some common materials used for LPG storage tanks include:
- Steel: Steel is a common material for LPG storage tanks, due to its strength, durability, and resistance to corrosion. Steel tanks can be either aboveground or underground, and can be coated or painted to provide additional protection against corrosion.
- Stainless steel: Stainless steel is a common material used for cryogenic LPG storage tanks. It has good strength, durability, and resistance to corrosion at low temperatures.
- Nickel alloys: Nickel alloys, such as Inconel or Monel, can be used for cryogenic LPG storage tanks. They have good resistance to corrosion and embrittlement at low temperatures.
- Aluminum: Aluminum is another material that can be used for LPG storage tanks. Aluminum tanks are lightweight and corrosion-resistant, making them a good option for portable applications or locations with high humidity or salt air.
- Composite materials: Composite materials, such as fiberglass-reinforced plastic (FRP) or carbon fiber, can be used for LPG storage tanks. These materials are lightweight, corrosion-resistant, and have good impact resistance.
- Concrete: Concrete tanks can be used for underground storage of LPG. Concrete tanks are durable and can withstand high pressure, making them suitable for large-scale industrial applications.
LPG Storage Tank Sizes
LPG storage tank sizes can vary widely, depending on the specific application and the amount of LPG that needs to be stored. Some common LPG storage tank sizes include:
- Small LPG cylinders: These are typically used for portable applications, such as camping or outdoor cooking. They typically have a capacity of 1-20 pounds (0.5-9 kilograms) of LPG.
- Residential LPG tanks: These are often used to supply propane for heating and cooking in homes. They typically range in size from 100 to 1,000 gallons (380 to 3,785 liters) of LPG.
- Commercial LPG tanks: These tanks are used to supply propane for commercial applications, such as fueling forklifts or powering industrial equipment. They typically range in size from 1,000 to 30,000 gallons (3,785 to 113,562 liters) of LPG.
- Industrial LPG tanks: These tanks are used to supply LPG for large-scale industrial applications, such as power generation or chemical manufacturing. They can range in size from 30,000 to 250,000 gallons (113,562 to 946,353 liters) of LPG or more.
The specific LPG storage tank size that is required will depend on several factors, including the amount of LPG needed, the location and environment in which the tank will be installed, and the specific regulations and safety standards that apply to the installation. It is important to work with an expert in LPG storage tank installation to determine the appropriate tank size for the specific application.
LPG Storage Tank Specification
To specify an LPG storage tank, several factors need to be considered, including the required storage capacity, the type of LPG being stored, the location and environment in which the tank will be installed, and the specific regulations and safety standards that apply to the installation.
Here are some key steps to consider when specifying an LPG storage tank:
- Determine the required storage capacity: The storage capacity of the tank will depend on the amount of LPG required for the intended application. This may be based on factors such as the size of the property, the number of appliances being powered by the LPG, and the expected usage patterns.
- Identify the type of LPG: There are different types of LPG, including propane and butane, and the tank must be designed to store the specific type of LPG being used.
- Choose the appropriate tank type: Based on the required storage capacity and the intended application, select the appropriate type of LPG storage tank, such as aboveground, underground, horizontal, or vertical.
- Consider location and environment: Determine the location and environment in which the tank will be installed, taking into account factors such as accessibility, ventilation, and weather conditions.
- Check regulations and safety standards: Ensure that the installation complies with all relevant regulations and safety standards, including local building codes and fire safety regulations.
- Consult with an expert: Consult with an expert in LPG storage tank installation to ensure that the tank is properly specified and installed and that all safety and regulatory requirements are met.
By following these steps, it is possible to specify an LPG storage tank that meets the specific needs of the application while ensuring safety and compliance with regulations.
Uses of LPG Tanks
Liquefied petroleum gas is used in a number of applications. So in all such applications, the LPG tanks are required to store the LPG. Some of the typical uses of LPG Tanks are:
- Heating homes.
- Cooking appliances.
- Alternative fuel for cars and other vehicles.
- Refrigerant.
- Industrial uses like
- as an energy carrier.
- as feedstock for the chemical synthesis.
- for facilitating the different industries’ access to this substance.
Mind blowing.Thanks
1.Inserting the outlet line 300 mm into the vessel from its bottom is not a good practice. These days only one outlet line is recommended with drain line branched from it after the ROV.
2. Insulation on LPG storage vessels should be avoided.
This is very informative and it give basic details.
I will like to know more so that i can produce the tank from the design to construction.
Informative Anup. Thanks for sharing.
It’s interesting to know that different capacities determine the size of an LPG tank. I’m interested in learning more from an LPG storage tank manufacturer because I might need to have a large one.
It’s interesting to know that there are also temperature indicators on the bottom of an LPG tank. I’m currently looking for an LPG storage tank manufacturer because I’d like to use that kind of gas for my out door kitchen soon. After using an electric stove for years, I think it would be nice to start learning how to use real flames when cooking.
hello, I’m interest in the internal pressure retaining of LPG tank, is the reliquefaction required?
Can anyone share the spherical tank drawing?
Hello do you incorporate containment bunding in your design of LPG tanks of medium to large capacity or do they just require bollard or partition wall protection?
I thought they needed bunding to capture spillages ?
thank you
can you share 5 star hotel kitchen equipment gas line sizing and how to install lpg piping any drawings in pdf or autocad format. Thanks in advance.
wanted to know the density of LPG at 15 deg. temperature.
Very nice information but can you tell the thickness and grade for the iron useful in 1000 ton gas thank