In industrial processes and manufacturing plants, precise control over various variables such as temperature, pressure, flow, and level is essential to ensure efficient and safe operations. One of the critical components that enable this level of control is the modulating control valve or modulating valve. Modulating control valves play a pivotal role in regulating the flow of fluids or gases in a system, offering flexibility and precision in adjusting process parameters. In this article, we will explore the fundamentals of modulating control valves, their applications, and the benefits they bring to industrial processes.
What are Modulating Control Valves?
A modulating control valve is a device designed to maintain a specific process variable at a desired setpoint by continuously adjusting the flow rate of the fluid or gas passing through it. Unlike on/off valves, which operate in a binary manner, modulating valves can regulate flow with infinite variability, allowing for precise control and smooth operation.
The core components of a modulating control valve include an actuator, a valve body, and a positioner. The actuator is responsible for moving the valve plug, which controls the flow rate, while the positioner receives signals from the process controller to position the actuator accordingly, maintaining the desired setpoint.
What is Modulation?
In the context of modulating valves, modulation refers to the ability of the valve to continuously vary the flow rate of a fluid or gas passing through it in response to changes in the process variable being controlled. The goal of modulation is to maintain a specific process variable, such as temperature, pressure, level, or flow rate, at a desired setpoint.
Modulation is achieved by adjusting the valve opening, which in turn regulates the flow of the fluid or gas. The extent of the valve opening is controlled by an actuator, which is typically powered by air, electricity, or hydraulic pressure. The actuator receives signals from a process controller that monitors the process variable and compares it to the desired setpoint. Based on this comparison, the actuator positions the valve’s closure element (such as a plug or disk) to allow more or less flow through the valve, aiming to bring the process variable closer to the desired setpoint.
The speed and precision with which the valve can modulate the flow are critical to maintaining stable and accurate control. Therefore, modulating valves are often equipped with positioners, which are devices that ensure the actuator accurately positions the valve closure element in response to the control signals from the process controller.
Types of Modulating Control Valves
Modulating control valves come in various types, each designed to suit specific applications and requirements. The selection of a particular type depends on factors such as the nature of the fluid or gas being controlled, the desired level of precision, the operating conditions, and the intended application. Here are some common types of modulating control valves:
Modulating Globe Valve:
Globe valves are perhaps the most widely used type of modulating control valve. They have a linear motion and provide excellent throttling control, making them suitable for applications requiring precise and fine adjustments in flow rates. Globe Modulating valves are commonly used in industries such as chemical, petrochemical, and power generation. They provide tight shut-offs.
Modulating Ball Valve:
Ball valves are known for their quick opening and closing action, making them ideal for on/off applications. However, they can also be used for modulating control when equipped with a specialized actuator and positioner. Modulating ball valves (Fig. 1) are commonly used in industries like oil and gas, water treatment, and HVAC systems.
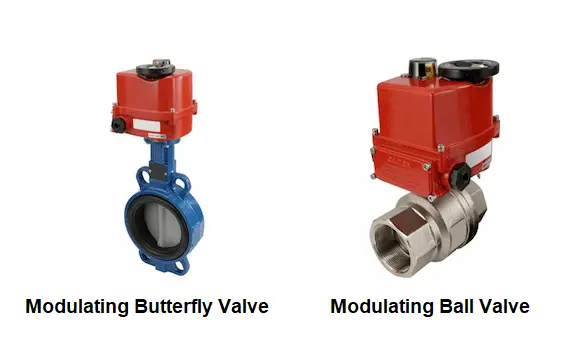
Modulating Butterfly Valve:
Butterfly valves have a simple and compact design, with a circular disk as the closure element. They offer good modulating control capabilities and are commonly used in large-scale applications where space and weight considerations are important, such as in water distribution and wastewater treatment. Modulating butterfly valves (Fig. 1) are durable, relatively easy to maintain, and can handle large flow rates. They are often found in systems where space is limited.
Modulating Diaphragm Valve:
Diaphragm valves are primarily used for controlling flow rates of corrosive or abrasive fluids. They have a flexible diaphragm as the closure element, which is particularly suitable for preventing contamination of the fluid by avoiding contact with the valve components. Diaphragm valves are commonly found in the pharmaceutical, chemical, and food industries and in systems where the fluid is corrosive or abrasive.
Applications of Modulating Control Valves
Modulating control valves find applications across a wide range of industries, including:
- Process Industries: In chemical, petrochemical, and pharmaceutical industries, modulating control valves are used to regulate fluid flow and maintain accurate process parameters, ensuring product quality and safety.
- Power Generation: In power plants, these valves control steam flow to turbines, enabling precise regulation of power generation based on electricity demand.
- HVAC Systems: Modulating control valves in heating, ventilation, and air conditioning systems help maintain comfortable indoor temperatures by adjusting the flow of heating or cooling fluids.
- Water Treatment: Modulating control valves are employed in water treatment plants to regulate the flow of chemicals, water, or wastewater, ensuring efficient treatment processes.
- Oil and Gas Production: In the oil and gas industry, modulating control valves are used for regulating the flow of crude oil, natural gas, and other fluids in production, refining, and transportation processes.
Benefits of Modulating Control Valves
- Enhanced Efficiency: Modulating control valves provide precise control, reducing fluctuations and overshooting, leading to improved energy efficiency and reduced operating costs.
- Process Optimization: These valves allow operators to fine-tune process variables, optimize production, and meet strict quality standards.
- Reduced Wear and Tear: Modulating valves can extend the lifespan of equipment by reducing sudden pressure changes and eliminating unnecessary stress on pipelines and machinery.
- Safety and Reliability: Precise control of critical processes enhances safety by preventing unexpected deviations and potential hazards.
- Automation Integration: Modulating control valves can be seamlessly integrated into automation systems, allowing for remote control and monitoring.
Best Practices for Modulating Valve Management
To ensure the effective and reliable operation of modulating control valves, consider the following best practices:
- Regular Maintenance: Conduct routine inspections and maintenance to keep valves in optimal condition.
- Calibration: Regularly calibrate control valves to maintain accuracy and responsiveness.
- Positioner Tuning: Properly tune positioners to match the requirements of specific processes.
- Training and Knowledge: Ensure operators are well-trained in control valve operation and troubleshooting.
- Data Analysis: Utilize data from control systems to identify trends and optimize valve performance.
In conclusion, modulating control valves are essential tools for maintaining precise control over critical process variables in various industries. By integrating these valves into industrial processes and following best practices, businesses can enhance efficiency, productivity, and safety, ultimately contributing to their overall success.
Online Courses on Piping Design and Engineering
If you wish to dig deeper and learn more about elements of piping design and engineering then the below-mentioned online courses will help you to do so:
- Designing Piping Systems: Pipe Fittings Flanges Valves
- Piping Isometrics demystified through practical examples
- Flow of fluids through piping systems , valves and pumps
- The Complete Course on Piping Components for Oil&Gas Career
- Piping Design Engineering & Piping Isometrics Masterclass
- PG Diploma in Piping Design Engineering
- Click here for other relevant piping engineering courses