A pipe sleeve is a higher-size pipe section to protect the inner pipe from higher loads or to provide free movement in a certain direction. Through these pipe sleeves, the lower-size pipes or cables can easily run. In the process and power piping industry, there are many instances where pipe sleeves are used. In this article, we will learn the common applications of pipe sleeves in the piping and pipeline industry.
What is a Pipe Sleeve?
As already stated, a pipe sleeve is a protective cover to safeguard the original pipe. This protective shield for pipes ensures their longevity, integrity, and functionality. Depending on the purpose and application, A pipe sleeve can be made of various materials like Carbon steel, Cast Iron, Stainless steel, Copper, Nickel, Aluminum, PVC, Rubber, HDPE, Composites, etc. Carbon steel pipe sleeves are quite common. They create a barrier between the main pipe and its surroundings. Pipe sleeves do not restrict the thermal growth of piping and hence the thermal cycle remains unaffected. Refer to Fig. 1 for typical pipe sleeve applications.
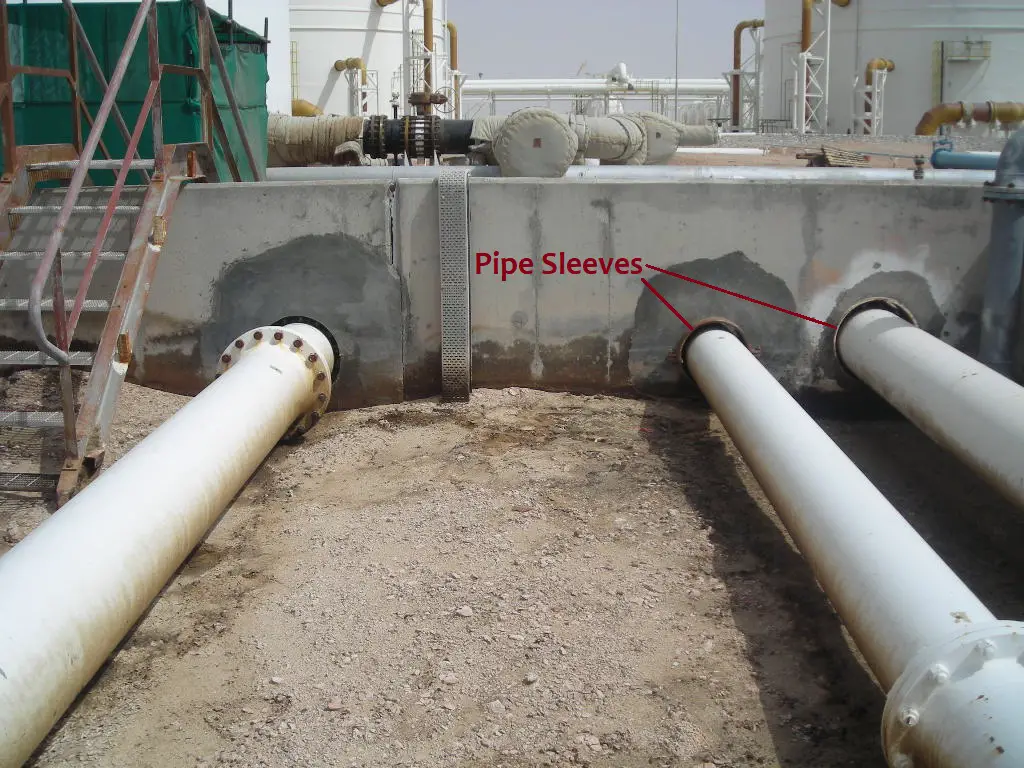
Purpose of Piping Sleeves
Piping sleeves serve several important purposes in piping systems:
- Protecting Pipes: They shield pipes from damage where they pass through walls, floors, or other structural elements. This helps prevent external damage, abrasion, corrosion, leakage, or physical impact.
- Allowing for Expansion and Contraction: Sleeves provide a space for pipes to expand and contract due to temperature changes without causing damage to the surrounding structure.
- Facilitating Maintenance and Replacement: By providing a clear passage through walls or floors, pipe sleeves make it easier to remove or replace pipes without disturbing the surrounding material.
- Preventing Leakage: Sleeves can help maintain the integrity of seals and prevent leaks between the pipe and the surrounding structure.
- Reducing Vibration Transmission: For vibrating piping systems, piping sleeves can also help reduce the transmission of vibrations from the pipe to the building structure, minimizing noise and potential structural damage.
Overall, piping sleeves are essential for ensuring the durability, functionality, and maintainability of piping systems.
Materials for Pipe Sleeves
As mentioned earlier, various materials can be used for piping sleeves. Some common ones are explained below:
Carbon Steel
Carbon steel pipe sleeves are widely used for their robust construction and cost-effectiveness, making them ideal for providing long-lasting protection to pipes. Their durability ensures that they can handle substantial wear and tear while maintaining the integrity of the piping system. Carbon steel’s notable resistance to corrosion makes it suitable for environments where pipes are exposed to moisture and other degrading elements. Additionally, the material’s inherent strength enhances the overall structural integrity of the pipe, contributing to a prolonged lifespan. This combination of resilience and affordability makes carbon steel a popular choice across various industries.
Stainless Steel
Stainless steel pipe sleeves are renowned for their excellent corrosion resistance, which makes them ideal for harsh and corrosive environments. These sleeves effectively resist rust and staining, ensuring a long service life even under challenging conditions. Their superior durability helps maintain the integrity of the piping system over time. Additionally, stainless steel’s sleek and modern appearance adds an aesthetic appeal, making it suitable for applications where visual impact is important. The combination of functional benefits and visual attractiveness makes stainless steel pipe sleeves a preferred choice in many demanding industries.
PVC
PVC pipe sleeves are favored for their versatility, lightweight nature, and cost-effectiveness. They offer effective protection for pipes, cables, and wires while being easy to handle and install. PVC’s resistance to a wide range of chemicals makes it suitable for environments where exposure to corrosive substances is common. The lightweight quality of PVC simplifies the installation process, reducing both time and labor costs. Its durable and insulating properties further contribute to its popularity in various applications, providing a reliable and efficient solution for pipe protection across different industries.
Rubber
Rubber pipe sleeves are valued for their flexibility and durability, making them ideal for situations involving frequent movement or mechanical strain. Their pliability allows for easy installation and adjustment, ensuring a snug fit around pipes and accommodating varying geometries. Rubber’s impact resistance provides significant protection against physical damage, enhancing the pipe’s overall durability. Additionally, rubber sleeves offer effective sealing and insulation benefits, making them indispensable in applications requiring resilience and adaptability. These characteristics make rubber a practical choice for industries that need reliable performance under dynamic conditions.
Composites
Composite pipe sleeves, made from materials like fiberglass and carbon fiber, offer customized solutions to address specific challenges in industrial piping systems. They provide exceptional strength, chemical resistance, and thermal insulation, making them well-suited for demanding environments. The ability to tailor composite materials allows for a balance between strength, flexibility, and environmental resistance. Innovations in composite technology ensure that these sleeves meet evolving industry needs by combining the best attributes of various materials. This adaptability and advanced performance make composites a preferred choice for creating durable and efficient piping solutions.
Note that whatever material is used for the piping sleeve, when it is used for railroad crossings, proper design calculation has to be performed to ensure that the pipe sleeve thickness is sufficient to carry the loads. API 1102 provides certain guidelines for Rail-Road Crossing calculations.
Applications of Pipe Sleeves
Pipe sleeves find wide applications in the piping industry. Some of the common uses of pipe sleeves are:
- While running through the dike-wall or bund walls in the tank farm area if a pipe is not required to be anchored, it is routed through pipe sleeves.
- For buried pipes, while crossing rail or roads, or bridges and culverts, the original main pipe may be routed through pipe sleeves to protect the main pipe from heavy loads from vehicles and trains.
- Pipe sleeves are also commonly used in piping insulation.
- Plumbing pipe sleeves are used in industrial and residential buildings.
Functions and Uses of a Pipe Sleeve
Pipe sleeves can also be used to repair a pipe temporarily to avoid costly shutdowns. By properly deciding the sleeve pipe thickness they can be welded directly over the main pipe and can serve the purpose of the main pipe. Pipeline sleeves are used for the temporary repair of pipeline leakages.
Full encirclement pipe sleeves are used in the weaker sections of the pipe to provide reinforcement on the parent pipe. They are also widely used during hot tapping operations where branch connection is taken from operating lines.
PVC pipe sleeves are widely used for cable and wiring solutions, mostly for building applications.
In some situations, spacers are provided to support the pipe or pipeline inside the pipe sleeve. This type of arrangement with equidistant spacer supports is quite common for buried composite piping systems (FRP and GRP piping systems) where running through rail or road crossings.
It is a good passion, to blogging in social media about our experiments, work and profession. Witch help to others to gain the knowledge, which was not limited to ourself
When inserting a pipe through the bundwall of a tank farm, what and how is the best method to prevent leak between the pipe and the bundwall?
Well articulated post, gives a detail knowledge of the product without being unnecessary lengthy.
Would like to know more about piping components from you blog.
Have a agood day
Dear Sir
Keep posting. Its helps new people in the industry to learn about different stuffs of oil & gas without struggling.
Good work . Keep it up
Do you have any reviews/literature regarding pipe sleeves for in-service welding according to API 1104 Annex B ?
Can you please also explain the “what is the methodology for the installation of the sleeves and the watermain”?
Thank you for this information. I am not in your field, but I work with engineers. This was an easy read and very simple to grasp. Thanks again!
You know which standard should i check to find out what kind of sleeve is used for a explosive room.
Im working with fire protection system.
Best regards
Is a sleeve necessary for the following conditions when a pipe crosses the road within the station’s piping scope?
Steel pipe crossing a black road (tramac road).
Steel pipe crossing a grader road.
Steel pipe crossing either a black road (tramac road) or a grader road, but it is difficult to install a sleeve due to the proximity of another line and insufficient gap for the sleeve.