In the world of industrial and commercial construction, the stability and longevity of piping systems are ensured by proper support of the pipes. Piping systems that carry fluids, gases, and other materials critical to various processes must be adequately supported for proper functioning. One key element in this support system is the spring hanger pipe support. In this blog post, we’ll explore what spring hanger pipe supports are, their benefits, and why they are an essential component in piping infrastructure.
What is a Spring Hanger?
A spring hanger is a type of pipe support that carries the weight of pipes and other components to compensate for the vertical movement or thermal expansion of these components. In critical piping systems, they are widely used. When due to pipe thermal movement, the line is lifting at some support points and the load is getting transferred to equipment nozzles, spring hanger supports are a good alternative that carries some of the pipe weight while allowing the thermal growth of the pipe.
Spring Hanger supports are basically mechanical resilient devices with a casing/housing that has a helical spring inside it that is pre-compressed during installation. While in operating condition, the inside spring is further compressed or expands depending on the pipe movement. So, during the operating condition, the spring support always bears some load. They are also known as Flexible Hangers.
Types of Spring Hangers
There are two types of Spring Hangers; Variable Spring Hangers and Constant Spring Hangers.
Variable Spring Hangers
Variable spring hangers are a type of spring hanger that supports a varying load with respect to pipe thermal displacement. The load of the variable spring hanger at the installed position is totally different from that of the operating condition. Variable spring hangers are used when the thermal displacements are less (usually less than 75 mm) and the load variation due to temperature difference does not make any significant impact to the piping system.
The standard practice of acceptable load variation for variable spring support is usually 25% as recommended by MSS-SP-58. However, for variable spring hangers near rotating equipment that are used to reduce equipment nozzle loads, the load variation is kept within 15%.
The term “variability” which is defined as 100*(Cold Load-Hot Load)/Hot Load indicates the load variation from the installed to working temperature condition. Here,
- Hot Load (HL)=Load that the spring hanger carries at working/operating temperature condition
- Cold Load (CL)=Load that the spring hanger carries during installed condition.
Mathematically, the formula of variability of a spring hanger support is represented as follows:
% Variability=100*(CL-HL)/HL=100*[Spring Rate(k)*Thermal Displacement(d)]/HL ….. Eqn 1
From the above equation if we know HL, Spring rate, and Displacement we can easily calculate CL and Variability.
And as informed,
- The Maximum variability for a piping system is<25%
- For Critical Piping Systems, the maximum variability is <15%
Constant Spring Hangers
Constant spring hangers can be defined as the type of spring hangers used in piping systems where there is no load variation. So, a constant spring support will carry the same loads irrespective of the piping temperature condition from installed to operating temperature condition. This means ideally the variability of constant spring hangers is Zero as Cold load = hot load.
Constant spring hangers are used when the displacement is too high or when the load variation is not expected. In, general constant springs are found near steam turbines, centrifugal compressors, and reactor piping systems to qualify the nozzle loads of such critical pieces of equipment.
Depending on the installation, supporting arrangement, and position of the spring hangers both variable and constant spring hangers are sub-divided into two major groups:
- Hanging Spring Supports, and
- Bottom Mounted Spring Hanger Supports
Hanging or Top-mounted spring hangers are installed from a top structure above the supporting pipe centreline and bottom-mounted spring hangers are installed from the bottom of the pipe similar to usual rest supports. Bottom-mounted spring hangers are often termed F-type spring Hangers. But there are several types of support arrangements for hanging type spring hangers and they are termed as A-Type, B-Type, C-Type, D-Type, etc. The following image in Fig. 1 (Reference: Carpenter and Paterson Catalogue) shows some of the typical spring hanger supporting arrangements.
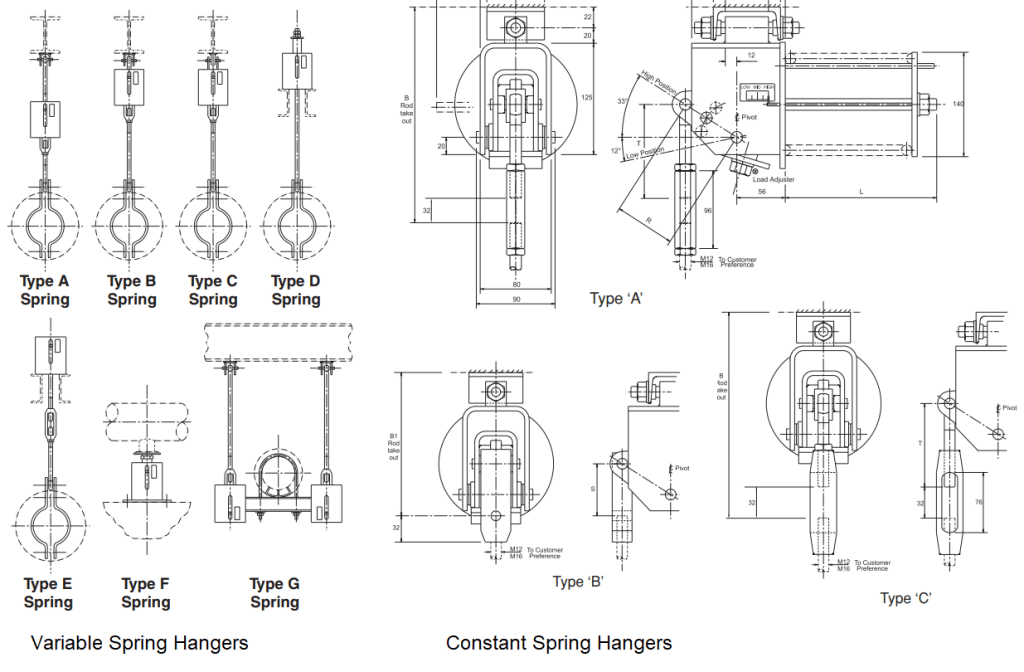
Components of a Spring Hanger
To effectively support piping loads, spring hangers have several key components as mentioned below:
Load Plate or Load Flange:
The load plate is the component that directly supports the weight of the pipe or equipment. It is typically a flat, horizontal surface that comes into contact with the bottom of the supported item. Load plates are available with bottom-mounted or F-type Spring hangers.
Hanger Rod:
The hanger rod is a vertical, threaded rod that connects the load plate to the upper attachment point. It acts as the primary structural element of the spring hanger, providing the means to adjust the height and tension of the spring.
Spring Assembly:
The spring assembly is the core component of the spring hanger, and it is responsible for providing the necessary spring force to support the load. The spring is typically made of specialized materials to ensure durability and flexibility. It’s designed to absorb and counteract the vertical movement of the supported item due to factors like thermal expansion, vibrations, or changes in load.
Upper Attachment Point:
The upper attachment point connects the hanger rod to the supporting structure, such as a beam, bracket, or other structural element. This point is crucial for anchoring the spring hanger securely in place.
Lower Attachment Point:
The lower attachment point connects the load plate to the load-carrying item, such as a pipe or piece of equipment. It ensures that the load is evenly distributed and that the hanger can move vertically as needed.
Adjustment Mechanism:
Many spring hangers include an adjustment mechanism that allows for precise control over the height and tension of the spring. This feature is essential during installation and maintenance to ensure that the supported item is correctly positioned and adequately supported.
Coatings and Finishes:
To protect against corrosion and enhance durability, spring hangers are often coated with materials such as epoxy, paint, or galvanizing. The choice of coating depends on the environmental conditions and the type of hanger.
Nameplate and Identification:
Spring hangers typically have a nameplate or load indicator that provides important information, including the hanger’s load capacity, specifications, and manufacturer details. This information is crucial for proper installation and maintenance.
Safety Features:
Some spring hangers may incorporate safety features like limit stops or travel stops to prevent over-compression or excessive movement, which could lead to damage or failure.
Accessories
Sometimes different accessories like Turn Buckles, Clamps, Lugs, etc. are required for proper connection with the pipe or support structure or adjustments.
Selecting the Spring Hanger
Selecting the spring hanger is always done with respect to a spring hanger catalog. So, if during the design phase of the project, the spring hanger vendor is finalized you can directly use that spring vendor’s catalog and it will make your technical bid evaluation process easier. Widely used reputed spring hanger vendors are Lisega, Anvil, PTP, Carpenter & Paterson, Binder, etc. If the vendor is not finalized, then select any of the spring catalogs and design your spring hanger based on that catalog. The steps followed for the selection of a spring hanger will be explained.
Selection of Variable Spring Hanger
Let’s understand the spring hanger selection process based on the Carpenter and Paterson spring catalog. A part of the variable support selection table from the same catalog is reproduced below in Fig. 2.
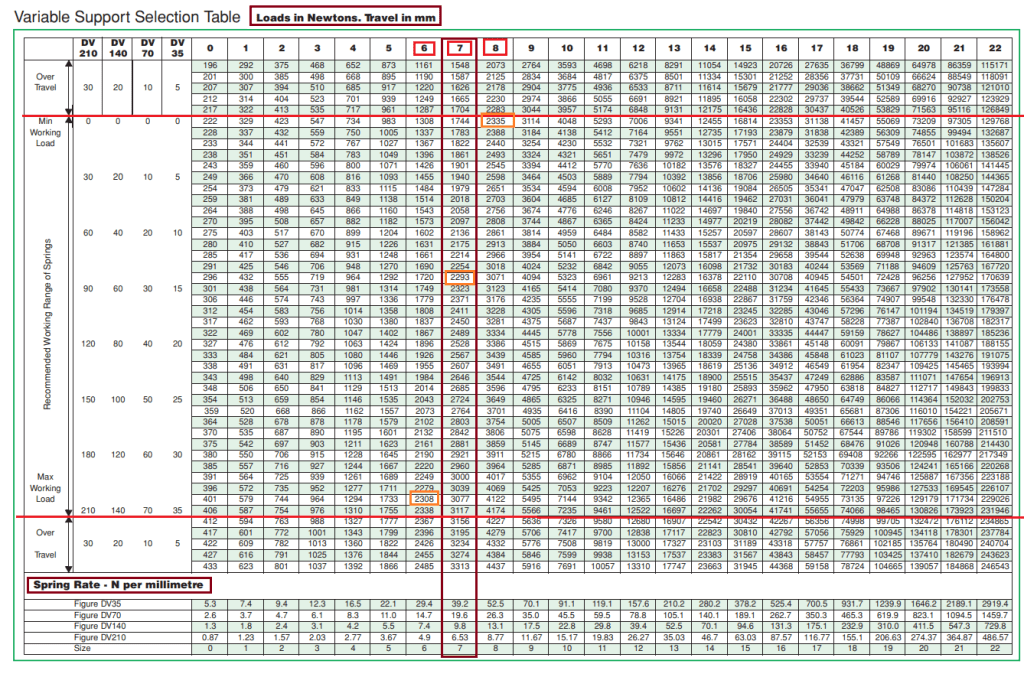
Now Let’s assume your pipe stress analysis software is showing the required load to support at operating (Hot) temperature condition is 2300 N. The maximum thermal displacement at that temperature is +20 mm (upward movement).
So cold load will be, CL=Hot Load (2300)+20 * Spring Rate as the movement is upward. (referring to the equation 1 above)
With these data in mind, we will enter into the spring support selection table and find out where the load 2300N is falling in the table. We can find that the load 2300 can be found in Size 6, Size 7, and Size 8. We have to select the spring in such a way that both the Hot Load and Cold Load fall inside the Red highlighted lines known as working range in the table. Now if we select Size 6, the cold load will be outside the range (Below the Bottom Red marked line). For Size 8, the hot load itself is near to overtravel (Top Red Line) and there is very little cushion for the spring. But if we select the variable spring hanger based on Size 7, both Hot load and Cold load will be within the working range.
So, we will design the spring hanger based on the Size 7. Now there are 4 choices for selecting the spring rate as per this catalog; DV 35, DV 70, DV 140, and DV 210. As we move from DV 35 to DV 210, the spring rate is reduced and so will the variability of the spring but the spring height will increase. DV 35 will be a compact spring, whereas DV 210 will be the longest spring.
Now Let’s calculate the variability for each choice.
- For DV 35, the variability is=100*39.2*20/2300=34% (Automatically it is not acceptable as variability limitation is 25%); Also for this case the Cold Load=Hot Load(2300)+20*39.2=3084 N which is again near the bottom working range.
- For DV 70, the variability is 100*19.6*20/2300=17% which is acceptable.
- For DV 140, the variability is 100*9.8*20/2300=8.5% which is also acceptable.
- For DV 210, the variability is 100*6.53*20/2300=5.7% which is also acceptable.
Hence, all three Spring rates for DV 70, DV 140, and DV 210 are acceptable. Now if your organization has a limit of 15% for spring hangers near rotary or other critical equipment you have to go to either DV 140 or DV 210.
Next, we have to check the heights of each spring. Let’s assume the above spring is a bottom-mounted F-Type Spring (You can easily calculate for hanging type springs as well). So From Fig. 3, you can easily understand that the installation length required is around 995 mm for DV 210.
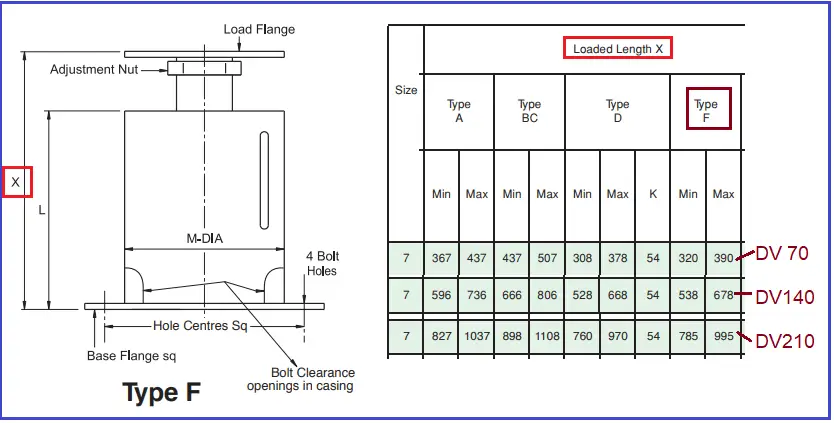
So based on the space available you can select your spring. Similar calculation you have to do for hanging-type spring hangers.
Selection of Constant Spring Hanger
To select a Constant Spring Hanger Support, find the Operating load and thermal movement from your stress analysis calculation. Let’s assume your travel is 127 mm and the load required to support is 5000 N.
Add an overtravel with this calculated travel (around 20% or as prescribed by your specification)
Hence total displacement after adding this over travel is 127+20%=152.4 mm.
Round off this value to the next 10 mm. So, designed travel for the constant spring hanger=160 mm.
Now that we know the operating load as 5000 N and displacement as 160 mm, we will enter the constant spring hanger selection table (Fig. 4) from the catalog.
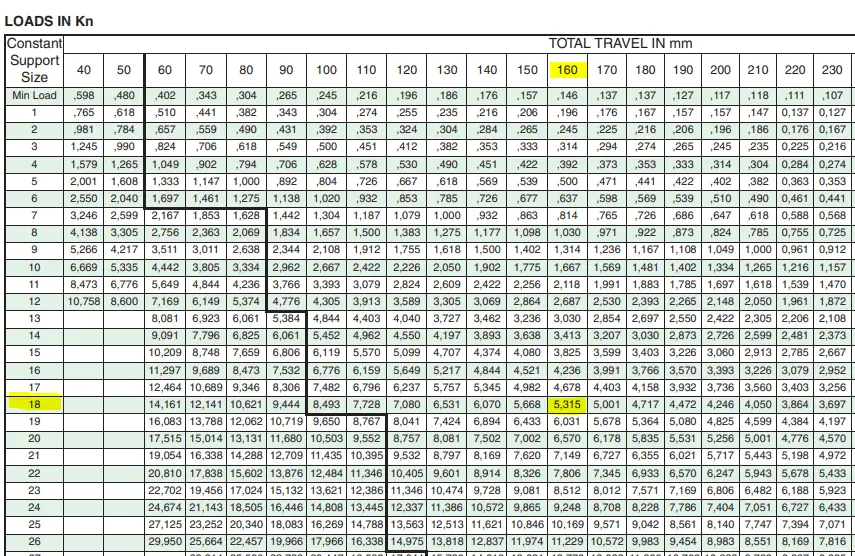
Locate Total Travel Column of 160 mm, and follow down the column for next load up from 5 KN (5000 N). This reads 5.315 KN.
Next, move horizontally to the left under the column headed ‘Constant Support Size’. In this example, the selected unit would be size 18. So your selected constant spring hanger will be Size 18. Now check which type of Spring hanger you need for installation and the space available and accordingly finalize that.
Some more insights regarding the selection of spring hangers are covered here. Further details about the spring hanger selection process using Caesar II software are presented here. Also, click here to learn the technical and general requirements for spring hanger support purchasing.
Benefits of Spring Hanger Pipe Supports
Load Management:
One of the primary benefits of spring hanger pipe supports is their ability to efficiently manage the weight of pipes and equipment. By distributing the load evenly, they prevent sagging, bending, or deformation of the pipeline. This not only extends the lifespan of the pipes but also ensures the efficient flow of materials.
Thermal Expansion Compensation:
Pipelines are subjected to temperature variations, causing them to expand and contract. Spring hanger pipe supports are designed with springs that can absorb this movement, preventing stress on the pipes. This is particularly crucial in high-temperature environments where thermal expansion is more pronounced.
Vibration Dampening:
In many industrial settings, pipelines may experience vibrations from nearby machinery or processes. Spring hanger pipe supports help dampen these vibrations, reducing the risk of fatigue and potential damage to the pipeline.
Adjustability:
Spring hangers are adjustable, allowing for precise control over the pipe’s elevation. This adjustability is vital during installation and maintenance, as it ensures that the pipeline is correctly aligned and supported.
Spring hanger pipe supports are essential components in the critical piping industry. Their ability to manage load, compensate for thermal expansion, dampen vibrations, and provide adjustability makes them invaluable for ensuring the integrity and longevity of piping and pipeline systems. Investing in quality spring hanger pipe supports not only improves safety but also contributes to long-term cost savings and regulatory compliance, making them an indispensable asset in the world of piping and pipeline infrastructure.
Great content!
I would appreciate the inclusion of counter weight support, which essentially works like a constant effort support with flexibility for load adjustment at site, if required.