In oil and gas piping applications, a bypass valve is a type of valve used to divert or redirect the flow of fluids within a system. It is designed to create an alternate flow path, allowing the fluid to bypass certain components or sections of the piping system. Bypass valves are mounted in bypass loops or bypass lines.
Purpose of Bypass Valves
The primary purpose of a bypass valve is to provide operational flexibility, maintenance convenience, and system safety. Here are a few common applications and benefits of bypass valves in oil and gas piping:
Maintenance and Repair:
During maintenance or repair activities, certain equipment or sections of the piping system may need to be isolated for inspection, replacement, or repair. By installing a bypass valve, the fluid flow can be redirected around the isolated area, ensuring uninterrupted operation of the rest of the system.
Pressure Regulation:
Bypass valves can be utilized to regulate pressure within a piping system. By adjusting the position of the bypass valve, operators can divert a portion of the flow to either increase or decrease pressure in specific areas, ensuring optimal operation of downstream equipment.
System Start-Up and Shutdown:
During system start-up or shutdown, bypass valves can be employed to gradually increase or decrease flow rates, preventing sudden pressure surges or shocks that could damage sensitive equipment.
System Testing:
Bypass valves facilitate system testing by allowing fluid flow to be redirected to a test loop or auxiliary equipment for evaluation without affecting the primary operation of the system.
Valves Suitable as Bypass Valves
Bypass valves come in various designs, including gate valves, globe valves, ball valves, or butterfly valves, depending on the specific requirements and characteristics of the piping system. They are typically installed in parallel or in bypass lines adjacent to the primary flow path and can be manually operated or automated, depending on the system’s complexity and control requirements.
The choice of valve depends on factors such as fluid characteristics, system requirements, pressure ratings, and operating conditions. Here are some commonly used valve types for bypass applications:
Ball Valves:
Ball valves are versatile and widely used in bypass applications. They offer low resistance to flow, quick operation, and tight shut-off capabilities. They are suitable for both on/off and throttling operations. Ball valves can be designed with a full port or reduced port, depending on the flow requirements.
Gate Valves:
Gate valves are often employed as bypass valves due to their ability to provide a straight-through flow path. They offer low-pressure drop and good shut-off capabilities. Gate valves are commonly used in isolation applications, but they can also be used as bypass valves when properly sized and installed.
Globe Valves:
Globe valves are suitable for throttling and regulating flow in bypass applications. They provide precise flow control and have good shut-off characteristics. Globe valves are often preferred when fine adjustments or flow modulation are required.
Butterfly Valves:
Butterfly valves are compact and lightweight, making them suitable for space-limited applications. They offer quick operation and provide low-pressure drops. Butterfly valves are commonly used for larger pipe sizes and can be effective as bypass valves when designed appropriately.
Check Valves:
In some cases, check valves can be utilized as bypass valves to allow flow in one direction and prevent backflow. Check valves are typically used in situations where flow reversal needs to be avoided, such as in pump bypass applications.
Working of a Bypass Valve
To understand the working of a bypass valve let’s take an example of a control valve station as shown in Fig. 1 below:
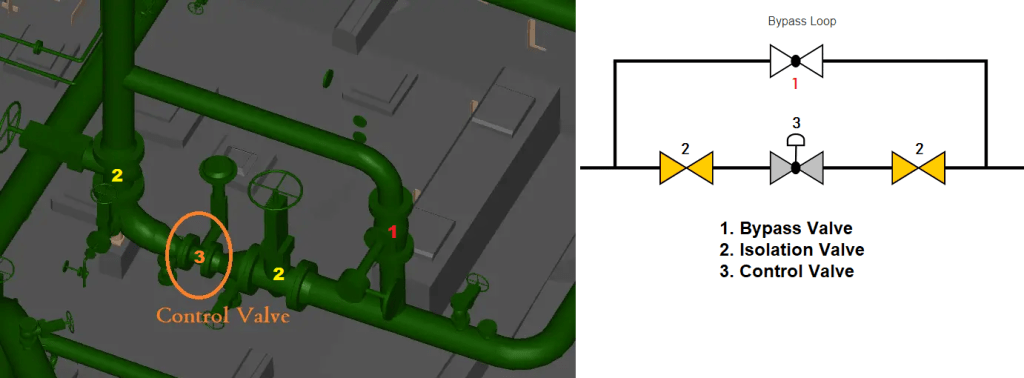
During normal operation, the isolation valves are kept open while the bypass valve is closed. So flow is transferred through the isolation and control valves and there is no flow through the bypass valve. During maintenance, if the control valve needs to be replaced, it has to be taken out of service. So, the maintenance professional will gradually open the bypass valve while closing the control valve in case of manual operation otherwise close one of the isolation valves.
So, the flow will gradually be transferred from the main line to the bypass line. An instrument usually indicates the flow or pressure of the line that the operator can easily observe. Once the flow is fully transferred to the bypass valve, both isolation valves are closed and the control valve can be vented or drained using the drain or vents installed in the line. The control valve can now be taken for maintenance or repair. So now the plant will operate normally and the flow will move through the bypass valve.
Applications of Bypass Valves
Bypass valves find applications in various industries and systems where redirecting or regulating the flow of fluids is necessary. Some common applications of bypass valves include:
Oil and Gas Pipelines:
Bypass valves are used in oil and gas pipelines for maintenance and repair activities. They allow the flow to be redirected, bypassing sections that require maintenance or isolation, ensuring uninterrupted operation of the rest of the pipeline.
Water Treatment Plants:
Bypass valves are employed in water treatment plants to divert the flow during maintenance, repair, or replacement of filtration systems, pumps, or other equipment. They ensure continuous water supply while the affected components are serviced.
Cooling Systems:
Bypass valves are used in cooling systems, such as HVAC (Heating, Ventilation, and Air Conditioning) systems, to regulate and control the flow of coolant or chilled water. They can redirect the flow to maintain optimal cooling performance, especially during maintenance or when specific areas require additional cooling.
Process Industries:
Bypass valves find applications in various process industries, such as chemical plants, refineries, and power plants. They are used to isolate equipment, redirect flows for testing or sampling purposes, and control pressure or flow rates in different parts of the system.
Steam Systems:
Bypass valves are utilized in steam systems to control pressure, divert steam flows, or bypass equipment during maintenance or shutdown. They allow for safe and efficient operation while specific components are serviced.
Hydraulic Systems:
Bypass valves are commonly employed in hydraulic systems to regulate pressure and flow rates. They can be used to bypass or isolate hydraulic components or control the operation of actuators and cylinders.
Fire Protection Systems:
Bypass valves play a crucial role in fire protection systems, such as sprinkler systems. They allow for testing, maintenance, and repair of the fire protection equipment without interrupting the overall system’s functionality.
Compressed Air Systems:
Bypass valves are used in compressed air systems to divert or isolate certain sections for maintenance, repair, or pressure regulation. They ensure continuous airflow while specific components or sections are serviced.
Really helpful contents
I’m working on a project of installing by-pass lines in the hydraulic system of our purse seiner fishing boats. Doing this will ensure sufficient flow rate in areas where it is more needed. The system operates with four hydraulic pumps and the by-pass lines will make the system operational even when one of the pumps breaks down. The present set-up is one pump per certain hydraulic motor.