Piping and Pipeline Engineers often talk about pipe stress analysis or pipeline stress analysis which is a dedicated activity performed by stress engineers using some kind of software like Caesar II, Start-Prof, Autopipe, or Rohr-2. But to judge any piping or pipeline system, it is always good to know what is causing that stress in the piping or pipeline system. In this article, we will explain the answer to one of the most basic questions of pipe stress analysis; i.e., What causes the stresses in the pipe?
Classification of Stresses in Piping and Pipeline Systems
Let’s start the discussion by classifying the types of stresses in a piping system. In general, the Stresses generated in piping and pipeline systems can be broadly classified into three categories:
Primary Stresses:
These are stresses that result from external loads, such as internal pressure, dead weight, and external forces. They are generally steady and must be within the allowable limits to prevent failure.
Secondary Stresses:
These arise from displacement-controlled loads, such as thermal expansion or contraction. Secondary stresses are often self-limiting but can cause fatigue over time if not properly managed.
Peak Stresses:
These are localized stresses that occur at points of discontinuity, such as welds, fittings, and supports. Peak stresses are typically higher than the general stress in the system and can lead to crack initiation if not adequately addressed.
What Causes Primary Stresses in a Piping System?
1. Internal Pressure
One of the most significant contributors to stress in a piping system is the internal pressure of the fluid being transported. Internal pressure generates circumferential stress (also known as hoop stress) and longitudinal stress within the pipe wall.
Hoop Stress
This stress acts around the circumference of the pipe and is the result of the internal pressure acting outwards. It is the dominant stress in thin-walled pipes and is given by the formula: 𝜎h=(PD/2T).
Here,
- 𝜎h is the hoop stress
- P is the internal pressure
- D is the outside diameter of the pipe
- T is the wall thickness of the pipe
Longitudinal Stress
This stress acts along the length of the pipe and is generally lower than the hoop stress. It can be calculated using the formula: 𝜎𝑙=PD/4T.
From the above, it is clear that
- 𝜎h=2* 𝜎𝑙 which means hoop stress is more significant than longitudinal stress in the piping and pipeline system. In most piping or pipeline design codes, this hoop stress equation is used as the base equation for pipe thickness calculation.
- Both hoop stress and longitudinal stress are proportional to the internal pressure, which means the generated stresses increase with an increase in pressure.
- The stress in the piping or pipeline system increases with a decrease in pipe wall thickness (T) which means the stress and thickness are inversely proportional.
- Also, with an increase in diameter, the generated stresses also increase.
2. External Loads-Weight
The weight load constitutes of the following loads:
- Self Weight of the Pipe: The weight because of the material’s mass.
- Liquid Weight: The weight of the amount of liquids that the pipe carries.
- Insulation Weight: The weight of the insulation material, if any
- Rigid Body Weights: Weight of Flanges, Valves, or any other rigid bodies.
- Weight of external attachments.
- Weight of Snow and Ice.
These loads induce bending stresses and axial stresses in the pipe.
Bending Stresses:
These occur due to the pipe’s weight and any external forces acting on it. The magnitude of the bending stress depends on the pipe’s span length, support conditions, and the distribution of the external loads.
Axial Stresses:
Axial stresses are caused by the pipe’s weight and any external forces acting along its length. They are also influenced by the pipe’s restraint conditions, such as whether it is fixed, anchored, or free to expand and contract.
3. Pressure Transients (Water Hammer)
Pressure transients, often referred to as water hammer or pressure surge, occur when there is a sudden change in the flow rate of the fluid within the pipeline. This can happen due to the rapid closing or opening of valves, pump starts or stops, or sudden changes in demand. The water hammer generates a pressure wave that travels through the pipeline, causing high transient stresses. These types of stresses are known as occasional stresses as they usually occur for very short period of time with respect to the design life of the piping or pipeline system.
Impact of Water Hammer:
The rapid pressure changes can induce severe axial and hoop stresses, which can lead to pipeline rupture, joint failure, or support damage. It is essential to design systems with surge protection devices, such as pressure relief valves and surge tanks, to mitigate the effects of water hammering.
4. Other Occasional Forces
There are various other occasional forces that also contributes to the initiation of pie stress. Some of the notable occasional forces are:
- Wind Forces
- Wave forces
- Accidental forces
- Reaction forces of sudden PSV/PRV discharge
- Vibration generated due to
- High Flow velocities.
- Acoustic behavior (predominantly in gas systems)
- Equipment induced vibration
- Any other external events like vortex shedding, pulsating flow, two-phase flow, etc.
What Causes Secondary Stresses in a Piping or Pipeline System?
1. Thermal Expansion and Contraction
Piping systems are often subjected to temperature variations due to the nature of the fluids they transport or changes in ambient conditions. Thermal expansion and contraction cause the pipe material to expand or contract, leading to secondary stresses.
Thermal Stress:
A change in temperature causes a pipe to expand or contract. This movement can not be contained. This expansion needs to be absorbed. If the pipe can move freely without any restriction, there will not be any stress. However, because of the closed nature of the piping system, free thermal movement without restriction is not allowed. If the pipe deforms with little restriction, a little thermal stress is generated. However, if the pipe is over-constrained, the pipe and supports will experience increased load and stress.
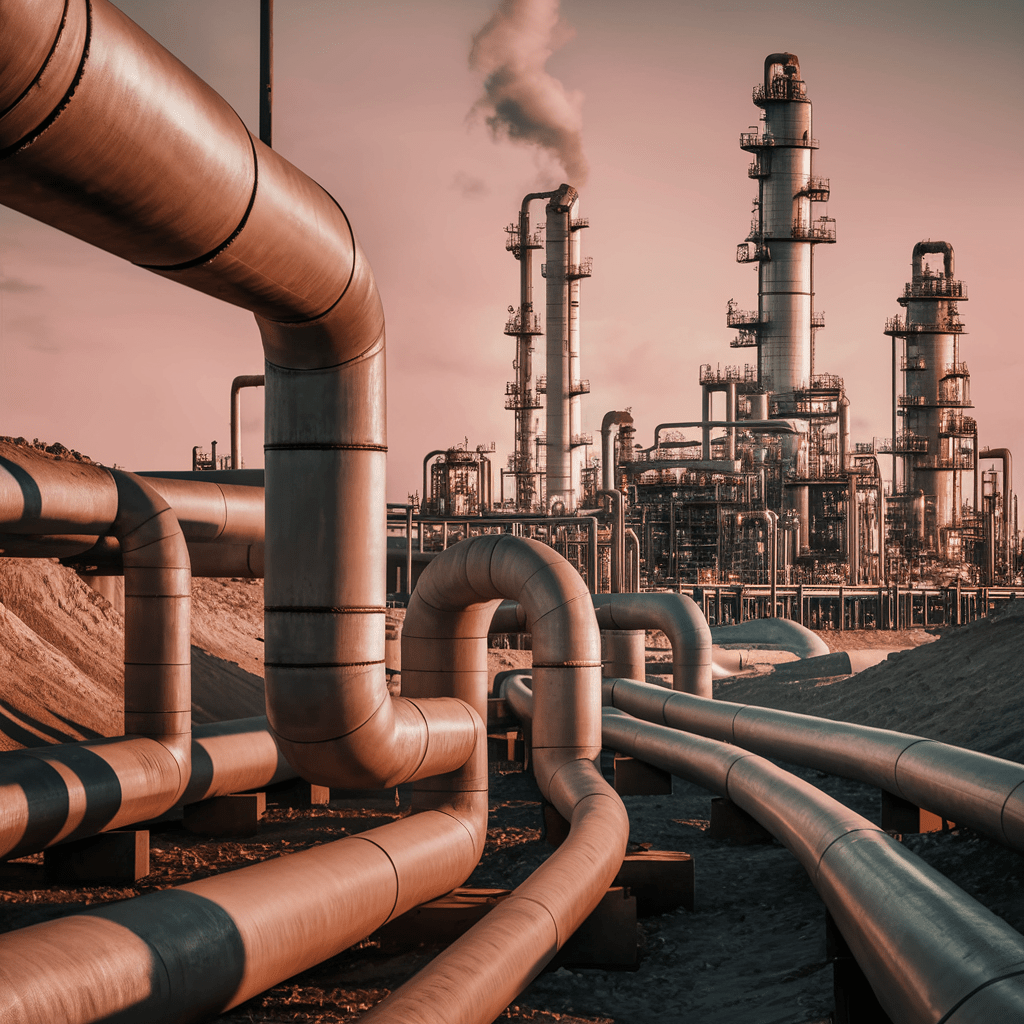
The stress induced by thermal expansion or contraction can be calculated using the formula: σt=E⋅α⋅ΔT
Where,
- σt is the thermal stress
- E is the modulus of elasticity of the pipe material
- α is the coefficient of thermal expansion of the pipe material𝑇
- ΔT is the temperature change
Thermal stresses are displacement-controlled and can cause significant movement in the piping system, leading to fatigue, stress concentration, and even failure if not adequately accommodated.
2. Thermal Gradient
A thermal gradient occurs when there is a temperature difference across the pipe wall or along the length of the pipe. This can happen in systems where hot and cold fluids are transported simultaneously, or where there are significant temperature differences between different sections of the pipeline.
Thermal Gradient Stresses:
The differential expansion caused by a thermal gradient can induce bending and axial stresses in the pipe. These stresses are particularly problematic in systems with rigid supports or where the pipe material has a low tolerance for thermal stress.
3. Pipeline Settlement and Ground Movement
In buried pipelines, ground movement due to settlement, earthquakes, or landslides can induce secondary stresses. These stresses arise from the differential movement of the pipeline relative to the surrounding soil or rock.
Settlement-Induced Stresses:
Differential settlement can cause bending and axial stresses in the pipeline. These stresses are particularly critical in long pipelines and can lead to buckling or rupture if not properly accounted for.
Seismic-Induced Stresses:
Earthquakes can generate significant ground movement, leading to high bending and axial stresses in pipelines. These stresses are often concentrated at points of restraint, such as bends, tees, and connections to rigid structures.
What Causes Peak Stresses in Pipe?
1. Discontinuities and Stress Concentrations
Peak stresses occur at points of discontinuity in the piping system, such as welds, fittings, flanges, and supports. These discontinuities create stress concentrations that are higher than the general stress in the pipe.
Welded Joints:
Welded joints are common sources of peak stresses due to the mismatch in material properties, geometry, and residual stresses from the welding process. Weld defects, such as cracks, porosity, or lack of fusion, can further exacerbate these stresses and lead to failure.
Fittings:
Fittings create geometric discontinuities that cause stress concentrations. For example, a sudden change in pipe diameter at a reducer fitting can induce peak stresses that are higher than the nominal stress in the pipe.
Supports and Restraints:
Pipe supports and restraints, such as clamps, hangers, and anchors, can create localized stress concentrations. The interaction between the pipe and the support can lead to high contact stresses, which can cause wear, fatigue, and eventually failure.
2. Corrosion and Erosion
Corrosion and erosion are common in piping systems that transport corrosive or abrasive fluids. These processes lead to material loss, which can create localized weak points and stress concentrations.
Corrosion-Induced Stresses:
Corrosion can cause thinning of the pipe wall, leading to a reduction in the pipe’s load-carrying capacity. Localized corrosion, such as pitting, can create stress concentrations that are much higher than the nominal stress in the pipe.
Erosion-Induced Stresses:
Erosion, particularly in high-velocity or turbulent flow conditions, can lead to material loss and the formation of localized pits or grooves. These defects act as stress concentrators, increasing the likelihood of crack initiation and propagation.
3. Fatigue
Fatigue is the progressive and localized structural damage that occurs when a material is subjected to cyclic loading. In piping systems, fatigue can be caused by fluctuating pressure, temperature cycles, and vibration.
Cyclic Loading:
Repeated cycles of loading and unloading, such as pressure fluctuations or thermal cycles, can cause fatigue in the pipe material. The fatigue life of the pipe depends on the magnitude and frequency of the cyclic loads, as well as the presence of stress concentrations.
Vibration-Induced Fatigue:
Vibration, particularly in systems with rotating equipment or turbulent flow, can induce cyclic stresses that lead to fatigue. Vibration-induced fatigue is often concentrated at points of discontinuity, such as welds, fittings, and supports.
Methods for Mitigating Stresses in Piping and Pipeline Systems
Mitigating the stresses in piping and pipeline systems is essential for ensuring their longevity, reliability, and safety. There are several methods and best practices that can be employed to reduce the impact of these stresses:
A. Proper Design and Material Selection
Design Codes and Standards:
Adhering to industry codes and standards, such as ASME B31.3 for process piping or API 1104 for pipeline welding, ensures that the piping system is designed to withstand the expected loads and stresses.
Material Selection:
Choosing the right material for the pipe, considering factors such as strength, toughness, corrosion resistance, and thermal properties, is crucial for minimizing stress-related issues. For example, selecting a material with a high thermal expansion coefficient can help reduce thermal stress in high-temperature applications.
Wall Thickness:
Increasing the wall thickness of the pipe can reduce the hoop stress induced by internal pressure. However, this must be balanced with the need to keep the system economical and manageable in terms of weight and installation.
B. Stress Analysis and Simulation
Finite Element Analysis (FEA):
FEA is a powerful tool for analyzing the stresses in complex piping systems. It allows engineers to simulate various loading conditions, including thermal expansion, pressure transients, and external loads, to identify areas of high stress concentration and potential failure points.
Piping Flexibility Analysis:
Flexibility analysis helps ensure that the piping system can accommodate thermal expansion and contraction without excessive stress. This involves calculating the pipe’s flexibility, considering factors such as support locations, pipe routing, and material properties.
C. Stress Mitigation Techniques
Expansion Loops and Joints:
Incorporating expansion loops or joints into the piping design can help absorb thermal expansion and reduce stress. These components provide the necessary flexibility to accommodate thermal movement without inducing excessive stress on the pipe or its supports.
Proper Support Design:
Properly designed and placed supports are critical for minimizing stresses in piping systems. Supports should be positioned to prevent excessive sagging, bending, and axial movement. Additionally, using spring supports or hangers can help accommodate thermal expansion and contraction.
Surge Protection:
Installing surge protection devices, such as pressure relief valves or surge tanks, can help mitigate the effects of pressure transients (water hammer). These devices absorb the energy of pressure waves, reducing the stress on the piping system.
D. Regular Inspection and Maintenance
Non-Destructive Testing (NDT):
Regular NDT, such as ultrasonic testing, radiographic testing, and magnetic particle testing, can help identify areas of stress concentration, corrosion, or fatigue before they lead to failure.
Corrosion Protection:
Applying protective coatings, using corrosion inhibitors, and implementing cathodic protection systems can help mitigate corrosion-induced stresses, extending the life of the piping system.
Fatigue Monitoring:
Implementing fatigue monitoring techniques, such as vibration analysis and thermal cycle monitoring, can help detect early signs of fatigue and allow for timely maintenance or replacement of affected components.
On a broader view, the following can be introduced to reduced stresses generated in a piping system:
- To reduce pressure stresses, increase the pipe thickness, if economically feasible.
- To reduce weight stress, add more support by reducing the support span.
- To reduce expansion stresses, add more flexibility to the system.
- To reduce occasional stresses, add more guides and axial stops in the piping system
- To reduce vibrational stresses, increase the system rigidity by adding supports.
Online Courses on Pipe Stress Analysis
If you are looking for an online course to learn pipe stress analysis then visit the following:
Complete Pipe Stress Analysis using Caesar II Online Course
thanks for info.