The injection quill is a precision-engineered mechanical device. As this device is widely used in the chemical injection process it is popularly known as the chemical injection quill. Various chemical industries use injection quills to provide an effective and safe means of injecting liquid chemicals into a vessel or pipeline system. They are usually a part of metering systems.
Applications of Chemical Injection Quills
Injection quills dose the chemical into the interior section of the flow and thereby keeping the chemical away from the sidewall and fittings. Chemical injection quills serve as an interface between the chemical feed line and the processing pipeline. The quill delivers the chemical efficiently into the interior of a process pipeline flow. Various chemical industries make use of chemical injection quills in applications like additive injection, bio-treatment, chemical injection, removal and separation processes, etc.
Chemical injection quills are used in a wide range of industries and processes, including:
- Water Treatment: In water treatment applications, chemical injection quills are used to introduce chemicals such as chlorine, chlorine dioxide, coagulants, and pH adjusters into the water to disinfect it, remove impurities, and maintain the desired water quality.
- Oil and Gas Industry: Chemical injection quills are employed in the oil and gas sector to introduce chemicals that aid in pipeline maintenance, inhibit corrosion, prevent scale formation, and enhance oil recovery during production.
- Chemical Manufacturing: In chemical production processes, quills are utilized to introduce catalysts, reactants, and additives into reaction vessels for precise control of chemical reactions.
- Pharmaceuticals: Chemical injection quills play a role in pharmaceutical manufacturing by accurately introducing active pharmaceutical ingredients (APIs) and other substances during drug synthesis.
- Wastewater Treatment: In wastewater treatment plants, chemical injection quills are used to introduce chemicals for flocculation and coagulation, aiding in the removal of suspended particles and pollutants.
Types of Chemical Injection Quills
To meet the demand for handling various chemical substances, there are a wide variety of injection quills that are found in industrial applications. All these chemical injection quills are categorized into one of the following two types:
Retractable Quills allow the operator to retract the injection quill without fully depressurizing the vessel or pipeline. These types of injection quills are complex in design and highly beneficial for clog-prone systems requiring frequent maintenance but where frequent shutdown is not feasible.
All retractable injection quills have the following components:
- Solution Tube that carries the treatment chemical.
- Restraint system to keep the solution tube in place.
- Isolation valve assembly consists of a valve and compression gland.
Non-Retractable Quills where the vessel or pipeline must be depressurized to remove the chemical injection quill. Non-retractable types of injection quills are widely used for chemical systems that do not form frequent deposits to clog the quill.
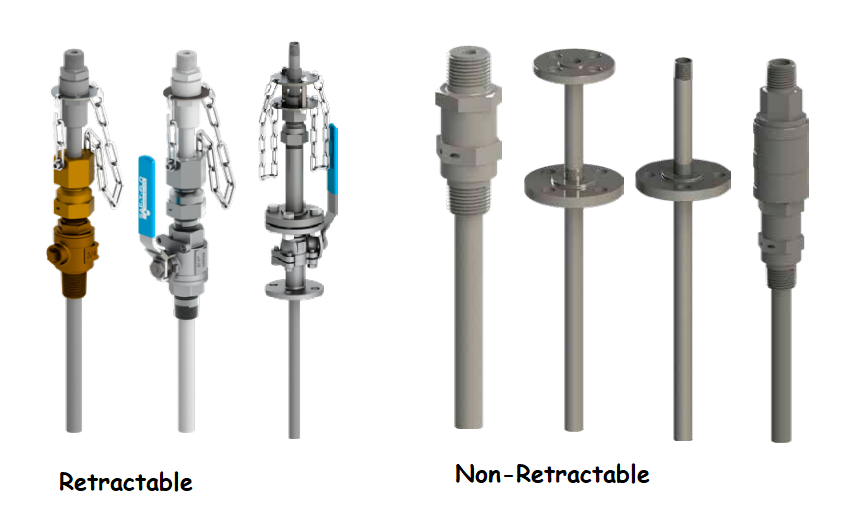
Depending on the number of Ports, injection quills are classified as follows:
- Dual Port Injection Quill: These types provide a uniform and rapid dispersal of two chemicals injected into one port.
- 3-port Injection Quill: Deaerators, boilers feed water tanks, etc use this type of injection quill for more uniform and rapid dispersal of chemicals into the center of the process pipe.
- 4-port Injection Quills: These are specially designed injection quills to disperse four chemicals into one port.
Chemical Injection Quill Configurations
Industrial injection quills are manufactured in various configurations, connections, and fittings. The configuration varies from a simple fabricated tube/probe to an integrated assembly with isolation valves and non-return valves. A compact integrated assembly consisting of the chemical injection quill, probe, double block & bleed assembly, and an integral non-return check valve is always beneficial.
Injection quills can be used as sampling quills by redesigning the probe and removing the integral check valve to safely take out fluid samples from the process line.
Chemical injection quills are mounted into the pipeline through a fitting. The probe is inserted and extended to the center of the process line. The other end of the injection quill connects to the chemical feed line by a pipe or tubing connection.
Designing An Injection Quill
The design of an injection quill is governed by various parameters like:
Design calculation
The wake frequency is calculated following the guidelines provided in the ASME PTC 19.3 TW standard for Thermowell as the injection quill is similar to it. The design of chemical injection quills needs both thermal and stress considerations. So process parameters like fluid, temperature, pressure, velocity, flow rate, density, viscosity, etc must be known for designing the injection quill.
Material of Construction
The material grade of the injection quill is selected such that the material is suitable for the service and the chemical to be injected. As the quill forms an integrated assembly together with the DBB and the check valve, several parameters similar to an isolation valve design must be evaluated.
Dimensions
The length of the injection quill is one of the most important parameters for wake frequency calculation. The length can be customized. Bore Size, Insertion Length, Tip Diameter, Root Diameter, Overall length, etc are the important dimensions to be considered during design.
Nozzles
In general, cylindrical tubes or nozzles are used for injection quills. However, specially designed nozzles depending on the application can be designed.
Mounting options
The design of injection quills can vary based on mounting options. Various different mounting options like flanged, welded, or threaded are possible. However, the quill/probe outside diameter (O.D.) must fit all the way down to the process stream.
Working Principle of Chemical Injection Quills
When the chemical injection pump operates, it pushes the chemical through the quill, which has a small orifice or series of holes at its tip. As the chemical is released into the fluid stream, it undergoes turbulent mixing with the surrounding fluid, promoting rapid dispersion and integration. The quill’s design helps prevent direct contact between the chemical and the pipe walls, which could lead to unwanted reactions or buildup.
Components of a Chemical Injection Quill Assembly
A chemical injection quill assembly consists of several essential components that work together to introduce chemicals or substances into a fluid stream. The specific design and configuration of the assembly may vary depending on the application and the requirements of the system. Below are the main parts commonly found in a chemical injection quill assembly:
- Injection Quill Body: The injection quill body is the main component of the assembly, usually a hollow tube or pipe made from materials compatible with the chemical being injected and the fluid in the system. It connects to the chemical injection system, such as a pump or storage tank, at one end.
- Injection Orifice or Holes: At the tip of the injection quill, there is an injection orifice or a series of small holes. These openings are responsible for releasing the chemical into the fluid stream. The size and number of orifices or holes are critical to achieving the desired injection rate and dispersion.
- Flange or Connection End: The end of the injection quill assembly that enters the fluid stream is typically flanged or threaded for easy installation and connection to the process piping. The type of connection used depends on the specific requirements of the system.
- Flange Gasket: A flange gasket is placed between the flange on the quill and the process pipe to create a secure and leak-free connection. The gasket material is chosen to be compatible with the fluid and the chemical being injected.
- Supports or Holders: Depending on the installation and process conditions, the injection quill may be supported by holders or brackets to keep it stable and properly positioned in the fluid stream.
- Injection Tube Extension: In some applications, a tube extension or extension pipe is attached to the injection quill to ensure that the chemical is introduced at the optimal location within the fluid stream. This extension can vary in length depending on the specific requirements of the process.
- Ball Check Valve (Optional): Some chemical injection quill assemblies may include a ball check valve to prevent the backflow of fluid into the quill. This check valve ensures that the chemical flows only in the desired direction.
- Stabilizing Fin (Optional): In certain applications, the injection quill may have stabilizing fins or vanes attached to the body. These fins help stabilize the quill in high-velocity fluid streams, reducing vibration and potential damage.
- Pressure and Temperature Sensors (Optional): In advanced quill assemblies, pressure and temperature sensors may be integrated to monitor the fluid conditions and provide feedback for process control.
- Chemical Injection System: Though not a part of the quill assembly itself, the chemical injection system, such as a chemical injection pump or storage tank, is an essential component that feeds the chemical into the injection quill.
It’s essential to ensure that the materials used in the construction of the chemical injection quill assembly are compatible with the chemicals being injected and the fluids in the process to avoid any chemical reactions or material degradation that could affect the system’s performance and integrity. Regular inspection, maintenance, and monitoring of the quill assembly are also crucial to ensure safe and efficient operation.
Selection of Injection Quills
The selection of required injection quills depends on the following factors:
- Retractable or Non-Retractable
- Key dimensions like solution tube size, process connection size, insertion length, pressure class rating, etc.
- Materials of Construction required.
Advantages of Chemical Injection Quills
The use of chemical injection quills offers several advantages:
- Uniform Dispersion: The quill’s design ensures that the injected chemical is uniformly dispersed within the fluid stream, preventing localized concentrations and ensuring effective mixing.
- Minimal Contact with Pipe Walls: The quill helps minimize direct contact between the chemical and the pipe walls, reducing the risk of chemical reactions or scale buildup that could hinder flow and affect system performance.
- Precise and Controlled Dosing: Chemical injection quills allow for accurate and controlled dosing of chemicals, ensuring the correct amount is introduced into the system.
- Easy Installation and Maintenance: Quills are relatively easy to install and maintain, making them a practical choice for various applications.
In conclusion, chemical injection quills are essential components in many industrial processes where precise and controlled chemical dosing is required. Their ability to uniformly disperse injected chemicals ensures effective performance and reliable results in diverse applications, ranging from water treatment to oil and gas production and beyond.
Dear Mr. Kumar
Thanks for sharing your experience with us, I have one small Question
My question is How I can start working like piping Engineer ?
Arshad Adnan
Chemical Eng.
Hi Anup Kumar Dey, hpe you were fine and thanks for such an important contribution.
I´m Nestor, and I need to design an injection quill for an oil&gas process piping. I´d like to know wether you count at more information about it: design codes, bibliography about quill calculations, calculation samples and / or with calc´s srpeadsheets.
Thanks in advanced.
can you brief , me from were you create your literature what are the sources please list it out in this web site it will be more help full for me
Hi Anup,
Great content but unfortunately the pictures are not vissible. WIll you please, make sur ethe pictures/illustrations are viewable on th epage.
Regards,
The pictures are visible to me… Mostly your explorer is blocking the images…