The oil and gas industry plays a pivotal role in the global economy, supplying the energy needed to power industries, homes, and transportation systems worldwide. However, the infrastructure supporting this industry, including pipelines, storage tanks, and processing facilities, is subject to a persistent and costly problem: corrosion. Corrosion, the gradual degradation of materials (usually metals) through chemical reactions with their environment, poses a significant threat to the safety, efficiency, and economic viability of oil and gas operations. Corrosion inhibitors, substances that mitigate or prevent corrosion, are therefore essential to maintaining the integrity and longevity of oil and gas infrastructure. In this article, we will learn about corrosion inhibitors in detail.
What are Corrosion Inhibitors?
Corrosion inhibitors are chemical compounds that are added in very low concentrations to the flowing fluids (additives to the fluids) to significantly reduce the material corrosion rate. These corrosion inhibitors form a passive layer on the metal surface so the metal does not directly come in contact with the corrosive fluid. Depending on fluid composition, the quantity of water, and the fluid flow regime, the effectiveness of a corrosion inhibitor varies. To reduce the risk of corrosion in metals, corrosion inhibitors are widely used in the industry. Inhibitors are organic or inorganic compounds and are usually dissolved in aqueous environments. They are available in spray form in combination with a lubricant and sometimes a penetrating oil. However, they can be solids, liquids, or gases. Concentrations of corrosion inhibitors in the corrosive fluid vary from 1 to 15,000 ppm (0.0001 to 1.5 wt %).
In oil and gas exploration and production, chemical & petrochemical industries, petroleum refineries, water treatment industries, heavy manufacturing, and product additive industries, corrosion inhibitors are considered the first line of defense. Corrosion Inhibitors do not react with the fluid and can be applied in situ without causing any significant disruption to the process. To decrease the corrosion rate, Corrosion inhibitors affect any one of the four components of a corrosion cell (anode, cathode, electrolyte, and electronic conductor). The main mechanism on which most corrosion inhibitors work is adsorption.
Types Of Corrosion Inhibitors
Corrosion inhibitors can be classified based on the working mechanism, environment, and operating mode.
A. Depending on the mechanism or electrode process, corrosion inhibitors are classified as follows:
- Anodic Inhibitor
- Cathodic Inhibitors, and
- Mixed Inhibitors.
A.1: Anodic Inhibitors
Anodic inhibitors work by forming a protective oxide film on the metal surface, which reduces the anodic reaction (oxidation of the metal). Common anodic inhibitors include chromates, nitrites, and phosphates. These inhibitors are particularly effective in environments where oxygen is present, such as in cooling water systems.
- Chromates: Effective but toxic and environmentally hazardous.
- Phosphates: Commonly used in water treatment applications.
A.2: Cathodic Inhibitors
Cathodic inhibitors function by decreasing the reduction reactions (such as the reduction of oxygen) on the metal surface. Examples include compounds containing zinc and magnesium, which can form insoluble hydroxides that deposit on the metal surface, thus blocking cathodic sites.
- Bicarbonates: They can reduce corrosion rates in specific environments.
- Alkaline Substances: These raise the pH of the environment, which can slow down corrosion.
A.3: Mixed Inhibitors
Mixed inhibitors affect both anodic and cathodic reactions. They provide comprehensive protection by forming a film on the metal surface that impedes both oxidation and reduction processes. Commonly mixed inhibitors include amines and silicates.
- Amine-Based Inhibitors: Widely used in oilfield applications due to their effectiveness in both acidic and neutral environments.
- Imidazolines: Organic compounds that can provide robust protection against corrosion.
B. Based on the environment, corrosion inhibitors are of the following types:
- Acidic environment inhibitors
- Inorganic inhibitors (Example: As2O3, Sb2O3)
- Organic inhibitors (Example: amines, aldehydes, alkaloids, nitro, and nitroso compounds)
- Alkaline inhibitors (Examples: thiourea, substituted phenols, naphthol, β-diketone, etc.)
- Neutral inhibitors
C. Depending on the protection mode, the following types of corrosion inhibitors are found:
- Chemical passivation (Nitrites, Chromates, Zinc molybdate, etc)
- Adsorption inhibitors (quinolines, sulfur atoms in these compounds, nitrogen atoms in amines, and oxygen atoms in aldehydes)
- Film-forming inhibitors (Zinc and calcium salts, Benzoate, etc)
- Vapor phase corrosion inhibitors (Dicyclohexylamine chromate, benzotriazole, Phenyl thiourea, cyclohexylamine, dicyclohexylamine nitrite, etc.)
- Volatile corrosion inhibitors (Molybdenum oxide, salts of dicyclohexylamine, cyclohexylamine, and hexamethylene amine)
- Synergistic inhibitors (chromate-phosphates, polyphosphate-silicate, zinc-tannins, and zinc-phosphates)
- Precipitation inhibitors (Sodium silicate)
- Green corrosion inhibitors (Amino acids, alkaloids, pigments, and tannins)
Working Mechanism of Corrosion Inhibitor
Corrosion inhibitors work through various mechanisms, depending on their chemical nature and the type of corrosion they are designed to prevent. The primary mechanisms include:
- Adsorption: Many inhibitors adsorb onto the metal surface, forming a protective barrier that prevents corrosive agents from reaching the metal.
- Film Formation: Some inhibitors promote the formation of a stable, insoluble film on the metal surface, which acts as a physical barrier.
- Passivation: Anodic inhibitors can enhance the formation of a passive oxide layer on the metal, which reduces the rate of metal dissolution.
- Precipitation: Certain cathodic inhibitors can induce the precipitation of insoluble compounds that coat the metal surface and inhibit further corrosion.
In the following paragraphs, we will explore the Corrosion Inhibitor Selection for Oil & Gas Industry.
Sources of Corrosion for Oil & Gas Industries
Normally corrosion occurs in the water phase. The major sources of corrosion in the oil and gas industries are:
- Hydrogen sulfide: sulfide stress corrosion cracking (SSCC)
- Chloride: chloride stress corrosion cracking (CSCC)
- Carbon dioxide: Sweet corrosion.
- Oxygen: pits
- Bacteria: Microbiologically-influenced corrosion (MIC)
- Water Cut
- Strong Acids: hydrofluoric acid and hydrochloric or acetic acids for sandstone and carbonates, respectively, which can cause corrosion of production tubing, downhole tools, and casing
- Brines: In the presence of dissolved oxygen, act as corrosive.
Corrosion Inhibitor Selection Consideration
- The use of Corrosion Inhibitors (CI) as an alternative to CRA shall be decided in the earliest design stage based on ILSS, fluid corrosivity, total CAPEX & OPEX, and assumed efficiency & availability.
- ILSS based on BP, Intertek, and DNV research, values below 2.5 indicate CI likely successful with below 50 ppm, and a value above 5.5 is usually not feasible, CI likely requires a very high dosage and high-reliability injection package.
- Organic film-forming corrosion inhibitors’ efficiency is reduced in the presence of bacteria, oxygen, and scales. Hence, Compatibility with other chemical treatment and injection strategies shall be studied.
- Continuous, batch, or squeeze treatments are predicted to contain high concentrations of water. Batch treatment tends to be used in non-severe applications when continuous treatment is technically difficult or when additional protection is required for severe conditions.
- The chemical fluid analysis shall consist of temperature, pressure, flow rate, sand, CO2, H2S, Chloride, O2, pH, cation & anion, organic acids, bacteria, and viscosity.
- Failure risk and environmental policy & disposal must be addressed.
- The possible impact on downstream processes shall be studied.
- Corrosion inhibitors shall not be used as a primary option to mitigate cracking.
- High water cuts, velocity, temperature, presence of solids, and pre-existing corrosion have a negative impact on the effectiveness of corrosion inhibitors and require higher concentration.
- To comply with the environmental standard, rigorous test qualification, high-temperature stability, and long-term degradation, the use of green corrosion inhibitors from organic matter are increasing.
Probable issues with Corrosion Inhibitor Consideration
Corrosion Inhibitor is used in the oil & gas industry by continuous treatment via annulus or small tubing, batch treatment, tubing displacement, and squeeze treatment by adsorbing. In gas lift wells CI is introduced with the gas.
- Possible issues for continuous treatment via annulus: flashing & gunking, slugging, valve plugging, CI degradation, etc.
- Possible issues for continuous treatment via tubing: damage risk to injection line during installation, additional cost for accessories & wellhead modification, etc.
- Possible issues for batch treatment: Corrosion can occur between treatments, wells are taken off production for several hours, many wasted chemicals on restarting the well, and stable emulsions may form.
- Possible issues for squeeze treatment: expensive, may damage formation, wasted chemical, etc.
- Special corrosion inhibitor types and injection methods are required for acidizing or fracturing treatments.
The following images provide more guidelines about the corrosion inhibitors in the oil & gas industry.
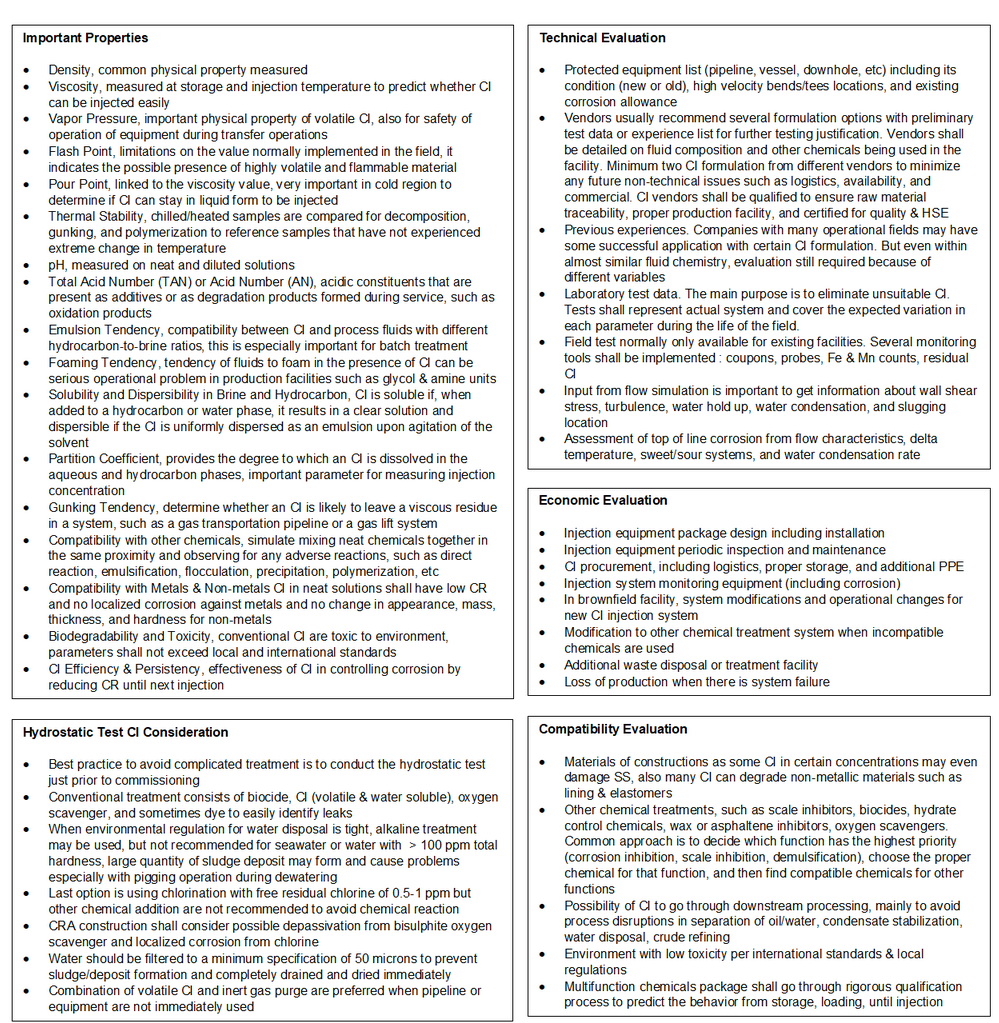
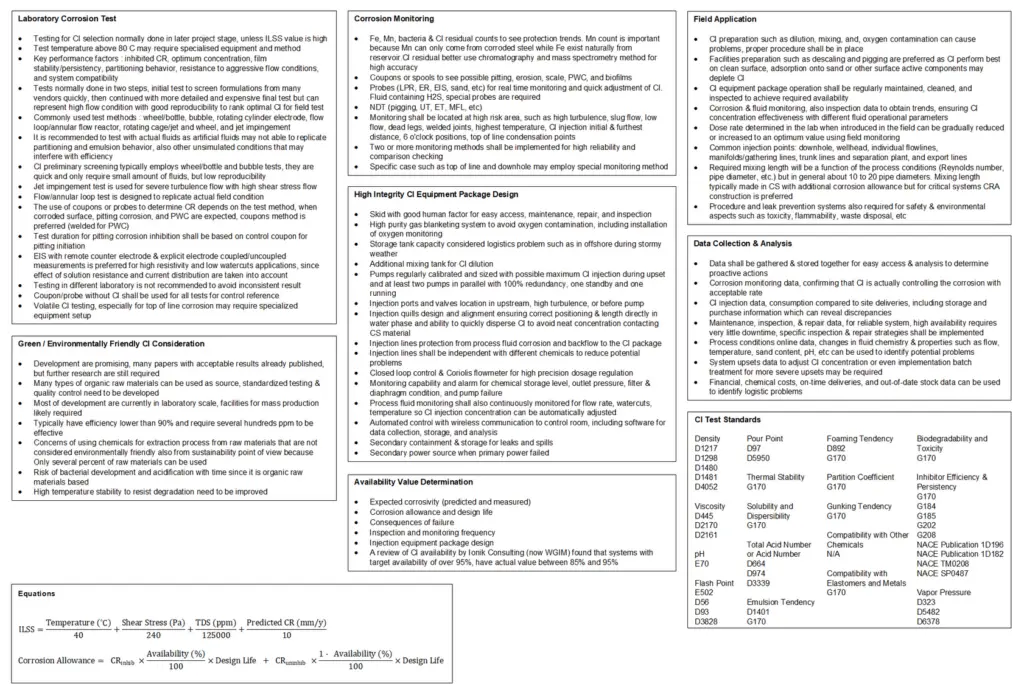
Applications of Corrosion Inhibitors in the Oil and Gas Industry
Corrosion inhibitors are used extensively in various sectors of the oil and gas industry, including:
1. Production Wells
In production wells, corrosion inhibitors are injected into the wellbore to protect tubing and casing from the corrosive effects of CO2, H2S, and chloride ions present in the produced fluids.
2. Pipelines
Pipelines transporting crude oil, natural gas, and refined products are susceptible to internal and external corrosion. Corrosion inhibitors are added to the pipeline fluids to protect the internal surfaces, while external coatings and cathodic protection are used for external corrosion control.
3. Storage Tanks
Storage tanks for crude oil and refined products are vulnerable to corrosion, especially at the oil-water interface. Corrosion inhibitors are often added to the stored product to protect the internal surfaces of the tanks.
4. Refineries
In refineries, corrosion inhibitors are used to protect equipment such as distillation columns, heat exchangers, and reactors from corrosive process streams containing sulfur compounds, acids, and salts.
5. Offshore Platforms
Offshore platforms face severe corrosion challenges due to the harsh marine environment. Corrosion inhibitors are used in combination with protective coatings and cathodic protection systems to safeguard structural components and equipment.
6. Downhole Equipment
Downhole equipment, including pumps and casing, is frequently exposed to corrosive substances like hydrogen sulfide (H₂S) and carbon dioxide (CO₂). Specific inhibitors can be tailored for these conditions to protect equipment integrity.
List of Corrosion Inhibitors
Here’s a table summarizing the names of corrosion inhibitors commonly used in the oil and gas industry, categorized by their type:
Type of Inhibitor | Examples |
---|---|
Anodic Inhibitors | Chromates |
Phosphates | |
Zinc Compounds | |
Cathodic Inhibitors | Sodium Nitrite |
Bicarbonates | |
Alkaline Substances | |
Mixed Inhibitors | Amine-Based Inhibitors |
Imidazolines | |
Cationic Surfactants | |
Volatile Corrosion Inhibitors | Benzotriazole |
Octadecylamine | |
Sodium Vapor Corrosion Inhibitors | |
Green Inhibitors | Plant Extracts (e.g., Neem, Rosemary) |
Chitosan | |
Tannin Extracts | |
Specialty Inhibitors | H₂S Scavengers |
Biocides with Corrosion Inhibitory Properties | |
Coating Systems | Epoxy Coatings |
Polyurethane Coatings | |
Zinc-Rich Primers |
This table provides a clear overview of various corrosion inhibitors used in the oil and gas industry, making it easier to identify and categorize them based on their type and application.
Corrosion inhibitors are essential tools in the oil and gas industry, protecting valuable infrastructure and ensuring operational efficiency. Understanding the types, mechanisms, and applications of these inhibitors is crucial for effective corrosion management.
Frequently Asked Question-Corrosion Inhibitors
1. What are corrosion inhibitors?
Corrosion inhibitors are chemical compounds that, when added to a corrosive environment, significantly reduce the corrosion rate of metals. They work by forming protective layers, altering electrochemical reactions, or passivating metal surfaces.
2. How do corrosion inhibitors work?
Corrosion inhibitors function through various mechanisms, including:
- Film Formation: They create a protective barrier on the metal surface.
- Electrochemical Control: They modify the rates of anodic and cathodic reactions.
- Surface Passivation: They promote the formation of passive films that protect the metal from further corrosion.
3. What types of corrosion inhibitors are available?
Corrosion inhibitors can be classified into several categories:
- Anodic Inhibitors: Form protective oxide layers.
- Cathodic Inhibitors: Modify electrochemical reactions at the cathode.
- Mixed Inhibitors: Provide both anodic and cathodic protection.
- Volatile Corrosion Inhibitors (VCIs): Vaporize and condense on metal surfaces.
- Green Inhibitors: Derived from natural sources and environmentally friendly.
4. Where are corrosion inhibitors commonly used in the oil and gas industry?
Corrosion inhibitors are widely used in various applications, including:
- Pipeline Protection: To prevent corrosion from soil and water.
- Downhole Equipment: To protect against corrosive substances like H₂S and CO₂.
- Refineries and Processing Facilities: To maintain the integrity of reactors and heat exchangers.
- Offshore Platforms: To withstand harsh marine environments.
5. Are there environmental concerns associated with corrosion inhibitors?
Yes, some traditional corrosion inhibitors, like chromates, are toxic and pose environmental hazards. This has led to stricter regulations and a growing focus on developing green inhibitors that are less harmful to the environment.
6. How do I choose the right corrosion inhibitor for my application?
Choosing the right corrosion inhibitor involves:
- Understanding the Environment: Analyze the specific corrosive agents and conditions (pH, temperature, humidity).
- Compatibility: Ensure compatibility with the materials used in your equipment.
- Regulatory Compliance: Consider any environmental regulations that may affect your choice.
7. What are the costs associated with using corrosion inhibitors?
While the initial cost of high-quality corrosion inhibitors can be significant, they often lead to substantial savings by preventing costly failures and extending the lifespan of equipment. A cost-benefit analysis can help determine the most economical solution.
8. Can corrosion inhibitors be used in combination?
Yes, in some cases, corrosion inhibitors can be used in combination to enhance their protective effects. However, it’s essential to ensure that the combined products are compatible and do not counteract each other’s effectiveness.
9. How can I monitor the effectiveness of corrosion inhibitors?
Effectiveness can be monitored through:
- Regular Inspections: Visual and instrumental inspections of equipment.
- Corrosion Rate Measurements: Utilizing tools like corrosion probes.
- Chemical Analysis: Testing for the presence and concentration of inhibitors.
10. What are examples of corrosion inhibitors?
Corrosion inhibitors come in various types, each suited for different applications. Here are some common examples:
Anodic Inhibitors
- Chromates: Effective in forming protective oxide layers, but environmentally hazardous.
- Phosphates: Commonly used in water treatment and industrial applications.
Cathodic Inhibitors
- Bicarbonates: Help reduce corrosion rates in certain environments.
- Sodium Nitrite: Often used in cooling water systems to protect ferrous metals.
Mixed Inhibitors
- Amine-Based Inhibitors: Effective in both acidic and neutral environments, frequently used in oilfield applications.
- Imidazolines: Organic compounds that offer protection in various industrial applications.
Volatile Corrosion Inhibitors (VCIs)
- Benzotriazole: Used to protect metals in enclosed spaces by vaporizing and forming a protective layer.
- Octadecylamine: A common VCI for protecting equipment during storage.
Green Inhibitors
- Plant Extracts: Natural extracts, such as those from neem or rosemary, can provide effective corrosion inhibition.
- Chitosan: A biopolymer derived from chitin, known for its biodegradable and non-toxic properties.
11. What is the difference between rust inhibitor and corrosion inhibitor?
A rust inhibitor specifically targets the prevention of rust, which is the corrosion of iron and its alloys, typically in the presence of moisture and oxygen. In contrast, a corrosion inhibitor is a broader term that encompasses a range of chemicals designed to reduce corrosion in various metals, not just iron, across different environmental conditions. While all rust inhibitors can be classified as corrosion inhibitors, not all corrosion inhibitors prevent rust; some are formulated to protect metals like aluminum, copper, or steel from a wider variety of corrosive agents.
Thanks to Mr. Andry Soetiawan (Material & Corrosion Engineer) for preparing part of the article.
The following articles will serve more insights regarding corrosion:
Forms of Corrosion: Corrosion Types
Overview of Corrosion Under Insulation (CUI)
Guide for Coating Selection for External Bolting to Reduce Corrosion
Corrosion Monitoring Techniques & Surveys: A short Presentation
Corrosion Protection for Offshore Pipelines