Pipe Bevelling is the term associated with pipe joining methods. Pipe edges are beveled to create a specific configuration to facilitate efficient and reliable piping connection. Appropriate pipe bevelling improves proper pipe end fit-up for efficient joining which in turn, increases pipework integrity and functionality. Note that both the terms ‘pipe bevelling’ and ‘pipe beveling’ are correct and indicate the same process; the only difference is that the first one is the spelling in UK English, whereas the latter one is the spelling in US English. In this article, we will learn about the definition, purpose, types, and methods of pipe bevelling.
What is Pipe Bevelling?
Pipe beveling is a pipe fabrication process to create an angle between the edge of the end of metallic pipes and tubes. The standard pipe beveling angle is 37.50. This bevel angle is formed between the edge of the pipe or tube and a plane perpendicular to the surface. Pipe Beveling is a type of pipe end preparation process. A pipe end with a certain angle cut is known as a beveled end. The bevelling of the pipe end is an important step in the welding edge preparation process of pipe joining. The quality of piping or pipeline welding is directly related to the quality of the beveled pipe and proper pipe bevelling ensures the best quality pipe welding. Beveling of pipes can also be done for aesthetic reasons and for deburring cut ends to increase safety.
The main reason for the 37.5-degree pipe bevel angle is that the wending method uses nearly 50% less filler, metal, time, and heat as compared to the 45-degree angle joint pipe bevelling.
Why is Pipe Bevelling Important?
The pipe bevelling involves the removal of the pipe’s outer edge to create a sloped or beveled surface by an angled cut. This is essential for several reasons:
Weld Quality:
Pipe Bevelling ensures a larger surface area is available for welding which makes the weld joint stronger and more secure. Thus the risk of weld defects, such as lack of fusion or incomplete penetration is minimised.
Strength and Durability:
Properly beveled pipe edges promote a more even distribution of stress across the weld joint. It enhances the strength and longevity of the piping connection.
Reduced Risk of Cracking:
Appropriate Pipe bevelling minimizes the chance of cracks and fissures forming in the weld area. It increases the structural integrity of the pipe.
Smooth Transition:
The bevelling of pipe edges creates a smooth transition between the pipe and the weld. This reduces the risk of stress concentrations or irregularities in the weld bead.
Methods of Pipe Beveling: How to Bevel a Pipe?
There are various methods for pipe bevelling. Each method is suitable for certain applications and materials. In the below section, we will discuss some of the most common pipe-bevelling processes used in the construction industry.
Bevelling of Pipes by Hand Grinding
Pipe beveling by hand grinding is a manual method. Even though this is the cheapest beveling method, it is dangerous compared to pipe beveling using machines. Skilled operators use handheld grinders to create beveled pipe edges. This is a time-consuming method and at the same time maintaining the bevel quality is very difficult due to manual work. Certain small-scale projects usually use pipe bevelling methods using hand grinders.
Pipe Bevelling by Flame Cutting or Plasma Torch Cutter
In this pipe beveling process, a gas torch or plasma torch heats the piping edge and then removes metal with the plasma cutter or cutting torch. This method of pipe beveling is quite fast but as they create heat-affected zones, post-processing is required.
Piping Bevelling by Machining
Various machines like lathe machines or milling machines can be used for creating bevels in the pipe. This pipe beveling method is accurate but may not be possible for large pipes due to equipment limitations. This type of pipe bevelling is mainly performed in pipe fabrication shops.
Bevelling of Pipes by Mechanical Bevellers
Mechanical bevellers or pipe bevelling machines are the most efficient and precise pipe beveling methods which are suitable for straight as well as contoured bevels. Pipe beveling machines can be portable or stationary.
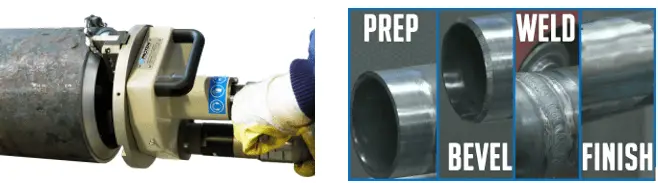
Types of Beveling
Pipe bevelling is a critical process in metalworking and welding. It involves preparing the edge of a pipe to facilitate welding. There are various types of Pipe beveling. Some of the common pipe beveling types are:
Straight Beveling: In this type of beveling, a straight bevel is machined at an angle of 30 degrees or 45 degrees.
Single-V Bevelling: In single-V bevelling, a single bevel is created on one side of the pipe. Single V bevelling is used when two pipes are joined together in a V-shaped groove weld. This is more suitable for thin pipes.
Double-V Bevelling: Double-V bevelling involves creating bevels on both sides of the pipe, resulting in a V-shaped groove on each side. This method is used when a thicker or larger-diameter pipe requires welding. It allows for a stronger and more even weld, distributing stress evenly across the joint.
U Bevelling: U bevelling is similar to V bevelling but with a U-shaped groove instead of a V-shape. It’s used when there is a requirement for deeper penetration in the weld, and it provides better access for the welder’s electrode or filler metal.
J-Bevelling: J-bevelling is characterized by a J-shaped groove on one side of the pipe, which is achieved by beveling one side of the pipe and leaving the other side square. This method is used for fillet welds where pipes are joined at a right angle.
Compound Bevelling: Compound bevelling involves creating complex bevel profiles, combining V, U, and J shapes to accommodate specific welding requirements. This method is often used in specialized applications where standard bevels are insufficient.
Countersink Bevelling: Countersink bevelling is used to create a tapered or conical surface at the pipe’s edge. It’s typically employed when a flush, smooth transition is needed between the pipe’s surface.
Selecting the Pipe Bevelling Method
The major factors that need to be considered while selecting the pipe bevelling methods are:
- Material Characteristics like hardness, thickness, brittleness, etc.
- Bevel Angle and width of angle cut.
- Available Tools and Equipment
- Complexity and Size of the Project
- Skilled Manpower requirement
Factors to Consider While Pipe Bevelling
The following factors are to be considered while pipe beveling:
- Angle of Beveling
- Length of beveling
- Speed
- Heat Generation
- Safety of the operator
Bevelling vs Chamfering
Chamfering is another machining process that is used for deburring, aesthetic, or functional purposes. The method of chamfering involves creating a beveled edge on a workpiece to remove sharp corners, improve safety, or enhance the appearance of the edge. The main differences between the beveling and chamfering process are added in Table 1 below:
Bevelling | Chamfering |
---|---|
The bevelling method uses specialized tools and machinery like pipe bevelling machines, milling machines, or grinders with beveling attachments | Bevelling means preparing for welding to improve weld quality and create smooth weld joints |
Beveling creates V-shaped, U-shaped, or J-shaped grooves | Chamfering creates Flat, angled edges, typically at 45 degrees or other specified angles. |
Beveling is used in welding and metalworking to improve structural integrity | Chamfering is used in woodworking, metalworking for deburring and aesthetics and proper assembly |
The bevelling method uses specialized tools and machinery like pipe bevelling machines, milling machines, or grinders with beveling attachments | The bevelling method uses specialized tools and machinery like pipe bevelling machines, milling machines, or grinders with beveling attachments |
Beveling typically involves removing more material to create grooves or bevels for weld joints | Chamfering usually involves minimal material removal, creating a beveled edge without significant thickness reduction |
HI SIR, RECENTLY I STARTED CARRER IN PIPING DESIGNER, PLEASE GUIDE ME WHAT HAVE TO LEARN, WHAT ARE THE SKIILS NEEDED, WHAT ARE THE BOOKS TO READ.