Pipe joints are integral to any piping system as the length of the pipe is limited. So, to have a continuous piping network, pipe joints must be used. Also, these pipe joints are usually the weak sections of a piping network. So, depending on the durability of the technique used to form the joint, the actual working of the piping or plumbing system varies. A variety of joints or joining methods are used in a piping assembly as per the requirement. So, pipe joints are an important component in any piping or plumbing system. Usually, the pipe joints are able to sustain the piping pressure.
What is a Pipe Joint?
A pipe joint is a connection point between two sections of pipe or between a pipe and a fitting. Its primary function is to ensure a secure, leak-proof connection that allows fluids or gases to flow through the piping system. Pipe joints also accommodate various mechanical stresses such as thermal expansion, contraction, and vibration, which can affect the integrity of the system. The main functions of every pipe joint are
- Sealing: Prevents leaks at the connection points, which is critical for maintaining system efficiency and safety.
- Alignment: Ensures that the connected pipes are properly aligned to facilitate smooth flow and reduce stress on the system.
- Flexibility: Allows for movement and adjustments in the piping system to accommodate changes in temperature, pressure, or mechanical forces.
- Ease of Maintenance: Facilitates the replacement or repair of pipe sections without needing to dismantle large portions of the system.
Types of Pipe Joints
Depending on application requirements, various types of pipe joints are used. They can be grouped as follows:
- Threaded joint
- Welded joint (butt welded, socket welded)
- Brazed and Soldered joint
- Grooved joint
- Compression joint
- Flanged Joint
1. Threaded joint
A threaded joint is piping joining, where pipes are joined by screwing in threads provided in the pipe. One of the pipes is provided with internal threads, whereas the other pipe has external threads. Threaded piping joints are ideal for non-critical, low-pressure-temperature, and low-cost applications like domestic water, fire protection, industrial cooling water systems, gas lines, plumbing fixtures, etc. The productivity of such pipe joints is moderate and installation is quite easy. Screwed piping joints should not be used for vibrating lines, as vibration can lead to leakage due to differential thermal expansion.
Threaded pipe joints are widely used for PVC, CI pipes, copper pipes, GI pipes, and brass or bronze, carbon, and alloy steel pipes. Even though threaded joints are available from 6 mm diameter to 300 mm diameter pipes, economic considerations normally limit industrial applications to 80 mm. Threaded construction is commonly used with galvanized pipe and fittings for domestic water and drainage applications. A screwed piping system is a good choice where maintenance or the process requires frequent disassembly and reassembly. Note that threaded pipe joints should always be used within the limits of the governing code.
The main advantages of threading pipes are:
- Simple and quick installation
- No need for additional sealing compounds if the threads are properly designed
- Allow for easy disconnection and reassembly
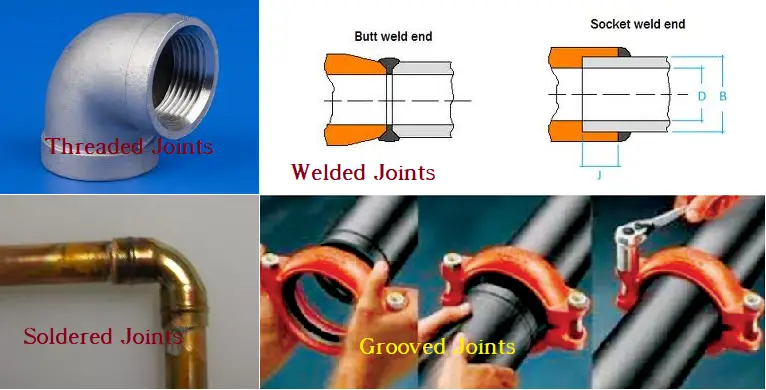
2. Welded joints
Welded joints involve fusing the ends of two pipes together using a welding process. This creates a continuous, seamless joint that is highly durable and strong. Welding joints are suitable for High-pressure and high-temperature applications, Structural applications, and Pipelines in oil and gas industries. There are two types of welding joints; butt-welded joints and socket-welded joints.
2.1 Butt-welded joints:
Butt-welded pipe joints are the most common for pipes in large commercial, institutional, and industrial systems. Skilled pipe welders and fitters are required for butt welding. Butt-welded pipe joints provide extremely good strength and leakage integrity. This pipe joining results in a low-pressure drop as the inside surface of a butt-welded piping system is smooth and continuous.
Butt-welded pipe joints are the preferred joints for high-temperature-pressure large-bore pipe applications. Most butt-welded piping installations are used for size NPS 2 (DN 50) or larger. They produce a smooth external pipe surface.
2.2 Socket-welded joints:
Socket-welded pipe joints are used for systems with high leakage possibility. In socket-welded pipe joints, one pipe is put inside the other and welded around the joint. The construction cost of this type of pipe joint is usually lower than butt-welded joints. However, the internal crevice is prone to corrosion. The mechanical strength of socket-welded pipe joints is better than other types of pipe joints.
The main advantages of welding joints are:
- High strength and durability
- Leak-proof when properly executed
- Suitable for high-pressure and high-temperature environments
3. Brazed and Soldered Joints
Brazing and soldering joints are widely used to join copper and copper-alloy piping systems. The brazing of steel and aluminum pipe and tubing is also possible. Both the brazing and soldering joining methods involve the addition of molten filler metal, which is drawn into the joint by capillary action. This metal then solidifies to fuse the parts together. The melting point of the pipe material has to be higher than the chosen filler material to avoid the melting of the parent pipe. Both of these piping joints are found in Residential plumbing, HVAC systems, and Low-pressure water systems.
Brazed and soldered joints provide very good leakage integrity and installation productivity. For medical gases and high-purity pneumatic control installations, brazed and soldered joints are popular. However, the mechanical strength of these systems is low.
The main difference between brazed and soldered joints is that brazing is done with molten filler material at above 840°C while soldering is performed at much lower temperatures. They are preferred for moderate pressure and temperature services. The main advantages are
- Provides a strong, reliable connection
- Easy to execute with basic tools
- Suitable for small-diameter pipes
4. Grooved Joint
Grooved joints are widely used for fire protection systems, ambient temperature service water, and low-pressure drainage applications. They are quite easy to install and uninstall; Hence, labor cost is lower. In these piping joints, two pipes are assembled together by making grooves at the end of pipes with the help of sockets or couplings. They usually provide good leakage integrity and can accommodate some axial misalignment. The grooved construction prevents the joint from separating under pressure.
The use of elastomer seals limits the use of grooved joints in high-temperature applications. Also, they have poor resistance to torsional loading.
5. Compression Joint
Compression joints are common for joining plain piping ends without any end preparations. Such pipe joints have the ability to absorb a limited amount of thermal expansion and angular misalignment. Using compression joints, pipes of dissimilar materials can be joined. The installation cost is low. They are mostly found in Plumbing systems, Gas lines, and HVAC systems.
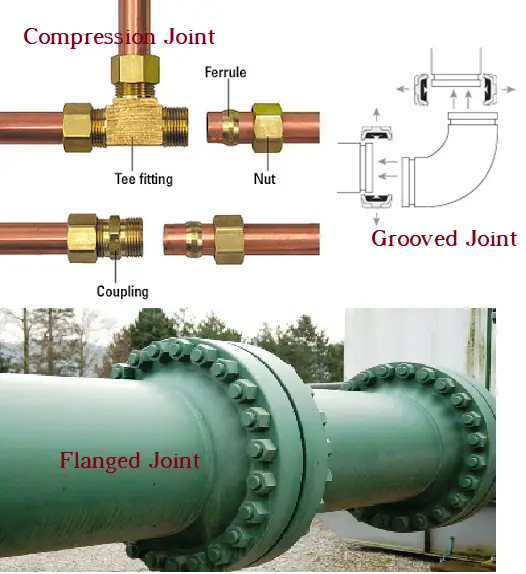
In compression joints, the pipe ends are joined with threaded fittings or couplings. To avoid leakage problems, the joints need to be properly placed to check the flow pressure.
In instrument and control tubing installations and applications where high seal integrity and easy assembly and disassembly are desirable, Compression joints are used. The main benefits of compression joints are:
- No need for special tools or skills for the installation
- Allows for disassembly and reassembly
- Suitable for a wide range of pipe sizes
6. Flanged Joint
In all modern piping and pipeline systems, flanged connections are extensively used due to their ease of assembly and disassembly. However, they are costly due to the high cost of the flanges themselves and the labor costs of attaching the flanges to the pipe using bolting. Flanged joints are used for all high-pressure and temperature applications. But they have a tendency to leak. Dissimilar pipe materials can be easily joined using flanged pipe joints. A gasket is inserted between two flanges to prevent leakage. To learn more about flanged joints, kindly refer to the following articles:
- Types of Flanges: Pipe Flange Types
- Pressure Temperature Rating and Flange rating of ASME Flanges
- https://whatispiping.com/?s=flange
The main advantages of flanged joints are:
- Strong, leak-proof connection
- Suitable for large pipe sizes and high-pressure applications
- Allows for easy disassembly for maintenance
7. Other Pipe Joint Types
There are some other types of pipe joints that are used for specific applications. Some of them are:
- Push-fit Joints
- Victaulic Joints
- Clamp Joints
- Expansion Joint
- Hydraulic Joint
Selection of Pipe Joints
The design and selection of a proper type of pipe joints can have a major impact on the initial installed cost. Also, the long-term operating and maintenance costs and the performance of the piping system are dependent on piping joints. There are various factors that must be considered in the pipe joint selection, like
- temperature and pressure range (high-pressure or low-pressure),
- pipe material (metallic or non-metallic),
- size of pipe (small or large),
- material cost,
- installation labor cost,
- degree of leakage integrity required,
- accessibility requirements,
- periodic maintenance requirements, and
- specific performance requirements.
Additionally, the pipe joint selection should meet the applicable code requirements.
To sum up, understanding the different types of pipe joints and their applications is essential for designing effective piping systems. Each joint type has its advantages and limitations, making it crucial to select the right one based on the specific requirements of your system. By considering factors such as pressure, temperature, pipe material, and accessibility, you can ensure a reliable and efficient piping system.
Frequently Asked Questions for Pipe Joints
Which is the most common joint in piping?
The most common joint in piping is the threaded joint. This method involves connecting pipes using male and female threads, which provide a secure and leak-proof connection, especially for smaller pipe sizes. Threaded joints are favored for their simplicity, ease of installation, and ability to be disassembled for maintenance.
What is pipe joint length?
Pipe joint length refers to the distance over which two pipes are joined together. It encompasses the length of the overlap or the segment where the pipes are connected to ensure a secure fit and proper alignment. The length can vary based on the type of joint and the specific requirements of the piping system.
What are the methods of pipe joining?
Methods of pipe joints include threaded, flanged, welded, soldered, compression, push-fit, Victaulic, and clamp joints. Each method has its own set of applications, advantages, and installation requirements, catering to different pipe materials, sizes, and system conditions.
How to join two pipes?
To join two pipes, first, ensure they are properly aligned and clean. Depending on the joint method being used, apply the appropriate technique—such as threading, welding, or using a compression fitting—follow the manufacturer’s instructions, and secure the connection to ensure a tight, leak-proof seal.
What is a pipe joint diagram?
A pipe joint diagram is a visual representation that illustrates how pipes are connected within a system. It shows the types of joints used and their arrangement, helping to clarify the layout and connectivity of the piping system for design, installation, and maintenance purposes.
Sir please explain Flange Allizment system
Good morning.
My winter project this year involves the restoration of a smallish marine diesel engine, a 1938 Gleniffer DB2. It originally had air start in that a V4 air motor engaged on a ring on the flywheel just like a modern electric starter motor. It works at 150-300psi and the air bottles are charged by the engine when it is running by knocking off the fuel to one cylinder and opening a valve on the head.
I have got most of the bits that I need except for some pipe/fittings and technical expertise!
I am enclosing a picture of the original pipework (approx 5/8 in diameter copper) and the joint which has a conical arrangement.
Is this a type of coupling that you recognise? If so do you know where I could get some pipework made up?
Regards and thanks Ian
One attachment will try to send separately.
• Scanned by Gmail
Very informative read! Exploring the different types of pipe joints and their applications provides valuable insights into plumbing systems. Whether it’s soldering, threading, or compression joints, understanding their strengths and best uses is essential for ensuring reliable and leak-free connections. Thanks for breaking down this crucial aspect of plumbing!