Welding stainless steel is the principal joining method employed during the fabrication of stainless steel products and components. Because of its excellent corrosion resistance, and elevated and cryogenic temperature properties, stainless steel is one of the widely used engineering materials. Stainless is extensively used in the oil and gas, chemical, petrochemical, power plant, food, and pharmaceutical industries.
Stainless Steel Welding Processes
Welding of stainless steel is generally performed by two basic methods: Fusion Welding and Resistance Welding.
Welding Stainless Steel by Fusion Welding
Fusion welding of stainless steel generates heat by an electric arc struck between the metallic electrode and the stainless steel material. Four widely used principal processes that are used for fusion welding of stainless steels are:
- SMAW (Shielded Metal Arc Welding)
- GTAW (Gas Tungsten Arc Welding)
- GMAW (Gas Metal Arc Welding)
- SAW (Submerged Arc Welding)
There are some other fusion weldings methods like electron beam, laser, and plasma arc welding. Note that, To preserve optimum corrosion resistance and mechanical properties in the joint, the weld zone must be protected from the atmosphere by a gas, vacuum, or slag.
Welding Stainless Steel with SMAW:
SMAW, being a fast and versatile process, is very popular for stainless steel welding. The manual welding method uses a solid electrode wire with an extruded baked-on coating material. One end of the electrode that is held in a spring-loaded electrode holder is bare. The operator holds the electrode at an angle at a minimum distance from the base metal to maintain the arc and moves it along the joint.
The alloy composition of the SS material decides the selection of electrodes for SMAW. Depending on the type of power supply and welding types, the coatings of electrodes are usually lime-based or titania-based materials. The coating creates a gas envelope that protects the molten metal from air contact. Refer to Fig. 1 for a basic representation of the SMAW stainless steel welding process.
Welding Stainless Steel with GTAW:
Also known as Tungsten Inert Gas Welding or TIG welding, the welding of stainless steel by GTAW uses Argon or any other inert gas to protect the welding zone from atmospheric contact. An intense electric arc generated between the non-consumable tungsten electrode and the SS workpiece creates the necessary heat for welding. In case filler metal is required, a bare welding rod is fed into the weld zone to melt with the base metal.
GTAW is widely used for welding stainless steel pipes, and joining tubes to tube sheets in shell and tube heat exchangers. There are two variations for GTAW for stainless steel welding to increase welding speed and get higher deposition rates.
- In the first variation, known as hot-wire GTAW, an automated process is used and the filler wire is heated by resistance heating.
- Pulsed-arc GTAW is another variation where a pulsing arc is used that controls the molten weld puddle to increase penetration.
The following figure (Fig. 1) shows a typical representation of welding stainless steel with TIG.
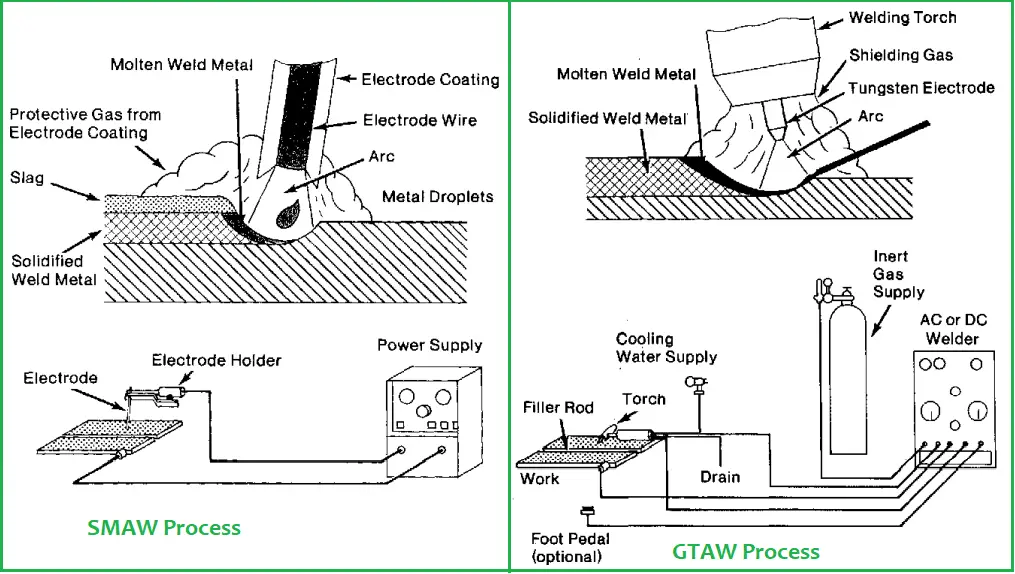
Welding Stainless Steel with GMAW:
Also widely popular as MIG welding, the gas metal arc welding of GMAW is a gas-shielded arc welding process using a consumable electrode that melts in a gas atmosphere. Refer to Fig. 2, which schematically shows the basic equipment like a torch, supply of shielding gas, DC power supply, and control for wire feed speed through the torch. The coiled form electrode filler metal is mechanically driven into the welding zone. Depending on the method of metal transfer, three variations of the GMAW process are found. They are:
- Spray Transfer
- Short-circuiting transfer, and
- Pulsed-type transfer.
The spray transfer or free flight transfer is characterized by a hot arc and fluid puddle. A short-circuiting transfer that is effective for welding thin stainless steel material utilizes small diameter wire (<0.045 inches). The pulsed-arc welding is characterized by a controlled free-flight metal drop rate of 60 drops per second at a lower current density.
Welding Stainless Steel with SAW:
SAW or Submerged Arc welding is a welding method where the heat for fusing the metal is generated by an electric current between the welding wire and the stainless steel workpiece. A layer of mineral flux composition covers the arc, the workpiece weld area, and the welding wire tip. No visible arc, spark, spatter, or smoke is found in this welding method and hence the name submerged arc welding. Refer to Fig. 2, which represents the SAW method schematically.
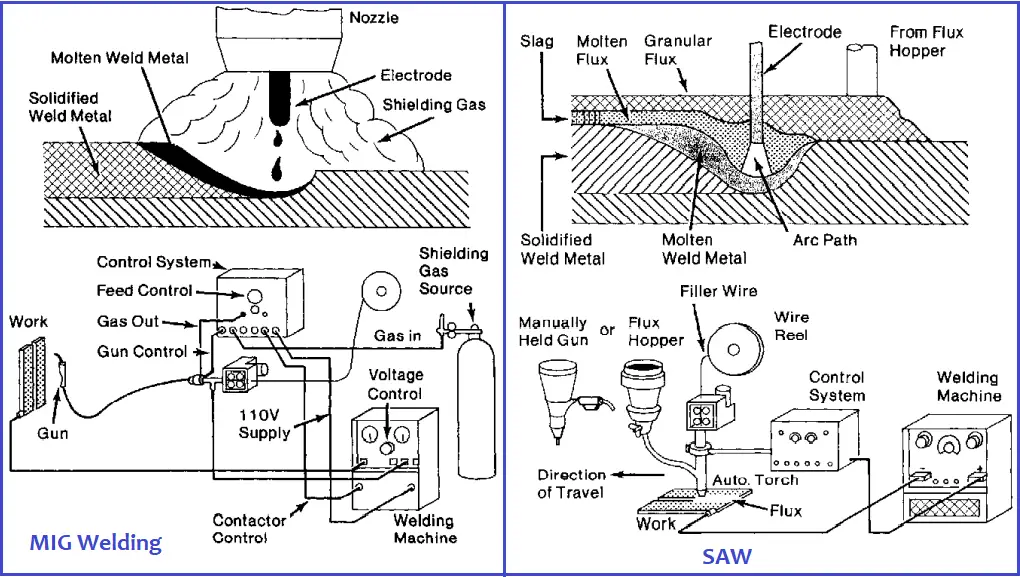
Welding Stainless Steel by Resistance Welding
One of the most economical and popular methods of joining stainless steel is by electrical resistance welding where heat is produced by the resistance to the flow of the electric current through the parts to be welded. For the mass volume of repetitive works, resistance welding for stainless steel products is particularly suitable. The widely used resistance welding processes for stainless steel welding are:
- Spot Welding
- Seam Welding
- Projection Welding
- Butt Welding
Welding of Stainless Steel using Spot Welding:
In spot welding of stainless steel, coalescence is produced by the heat generated from electric resistance and pressure on the electrodes. The contour of the electrodes limits the shape and size of the welds. The process uses two water-cooled electrodes or wheels which are brought together with the work parts using a mechanical force by foot, air, hydraulic, or motor-operated cam. The welding cycle consists of squeeze time, weld heat time, hold time, and off time. The parameters that affect the welding process are:
- Electrical resistance
- Thermal conductivity
- Expansion coefficient
- Strength at elevated temperature, etc
A typical process of spot welding is shown in Fig. 3.
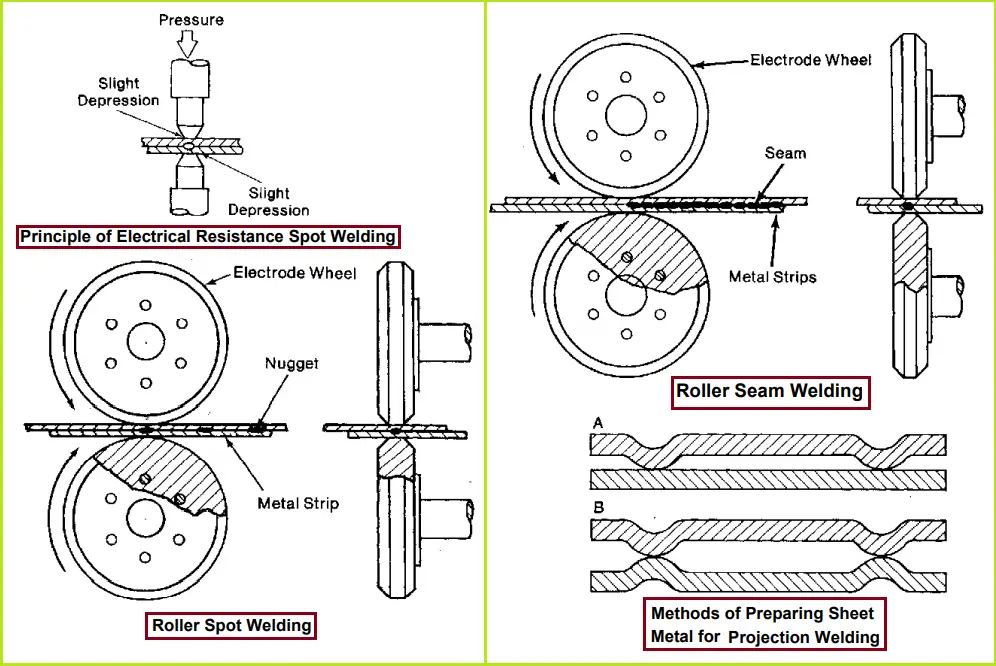
Welding of stainless steel by Seam Welding:
In the seam welding of stainless steel, circular electrodes (copper-based alloy) are used. A series of overlapping spot welds are progressively made by the rotating circular electrodes (Refer to Fig. 3) which supply the current as well as the pressure to hold the work parts. To get proper weld spacing, the electrode speed and current off-time must be adjusted. Usually, three types of seam welding machines are used:
- Circular
- Longitudinal, and
- Universal
Welding of stainless steel with Projection Welding:
Projection welding is best suited for heavy-gauge stainless steel workpieces. Localized welding is performed at predetermined points by projections, embossments, or intersections. At these projections, heat is concentrated and can be made in one or both pieces as shown in Fig. 3. Projection welding can be performed in almost all stainless steel.
Stainless Steel Welding by Butt Welding Process:
The butt welding process can be grouped into two classes; Flash Welding and upset Welding.
Flash Welding:
In the flash welding process, the work parts initiate a flashing action from the current delivered through the clamped electrodes. The basic sequence of flash welding of stainless steel is:
- load machine
- clamp workpiece
- apply weld current
- establish flash by contacting parts
- flashing
- apply upset force
- interrupt current
- unclamp workpiece
- unload and
- return platen.
Flash welding machines are manual, semi-automatic, or fully automatic and can perform various additional operations like pre and post-heating, clamping, shearing, flash trimming, etc. All types of stainless steel can be welded using flash welding.
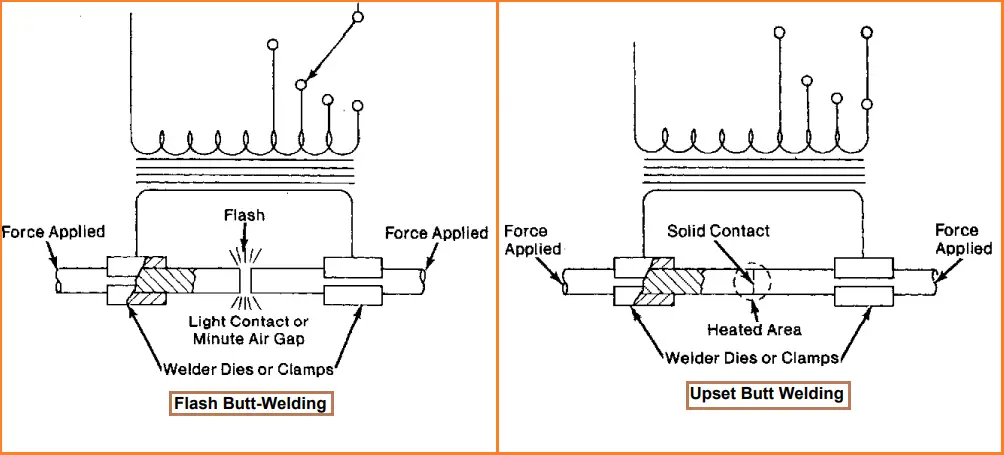
The alignment of the parts to be welded is very important so that heat is generated over the entire surface.
Upset Welding:
In the upset welding process, no flash occurs. The coalescence is produced over the entire area by the heat generated from the resistance of the electric current flow through the contact area of the abutting surfaces. The applied force is maintained throughout the heating period. The joining surfaces are brought together under pressure and the current is applied until the correct upset takes place and then the current is interrupted.
The non-heat-treatable stainless steels are easily weldable by this process. Continuous tube mills use this process quite extensively.
Other forms of resistance welding are high-frequency resistance welding, percussion welding, etc.
Welding of Stainless Steel Pipes
The selection of welding method for joining stainless steel pipes is dependent on:
- Pipe Size
- Pipe Thickness
- Possibility of pipe rotation, etc
TIG is widely used for stainless steel pipes of 4 inches and smaller sizes. Whereas for large-diameter pipes fully automatic methods are used.
Welding Courses Online
When developing in-depth knowledge about the welding processes and techniques, then the following online welding courses will surely serve the purpose:
- Learn MIG Welding
- Introduction to Welding Engineering
- A guide to become a Welding Inspector to start a Lucrative Career
Few more welding articles for you.
Welding Galvanized Steel
Overview of Pipeline Welding
Welding Positions: Pipe Welding Positions
Welding Defects: Defects in Welding: Types of Welding Defects
Welding Inspector: CSWIP and AWS-CWI
General requirements for Field Welding
Underwater Welding & Inspection Overview
Methods for Welding Stainless Steel