Pipe fabrication can be defined as the process of cutting, bevelling, and welding piping components such as pipes, tees, elbows, flanges, reducers, etc., as dictated by the design documents. In the process and power piping industry, Piping fabrication is a highly critical activity as it involves hundreds of components and thousands of steps and requires a high degree of precision. In any construction project wherever piping networks are involved, piping fabrication needs to be properly planned, scheduled, and executed as per design requirements. To maintain the system integrity, and proper functioning of each item, and minimize accidents, It is required to ensure maximum quality of work during pipe fabrication. In this article, we will explore more details about piping fabrication.
Piping fabrication involves various activities like piping material storage and handling, cleaning, cutting, bevelling, welding, inspection and testing, painting, insulation installation, etc.
Types of Piping fabrication
Depending on the location of the pipe fabrication work they are classified into two groups.
- Shop Pipe Fabrication and
- Field Pipe Fabrication.
Shop Fabrication vs Field Fabrication
There are various factors that determine whether pipes will be shop fabricated or field fabricated or both methods will be used. In most cases, both shop and field pipe fabrication is used. The major deciding factors are profitability, type, and size of the project, piping material, and size, post-fabrication surface treatment, environmental condition, accessibility of equipment, skilled personnel availability, time requirement, and availability, etc.
In general practice, small bore pipes, threaded and socket welded pipes are field fabricated whereas butt welded pipes, pipe bending, modular items, etc are shop fabricated.
In the Shop pipe fabrication process pipe, fittings and components are assembled by welding into spool assemblies at the fabricator’s facility or a workshop normally known as a pipe fabrication shop. The spools are then labeled using an identifier and transported to the construction site for installation. Whereas in field pipe fabrication all these assemblies are done at the construction site.
Tools/Equipment used for Pipe Fabrication
During pipe fabrication, various equipment and tools are used that helps in the fabrication process. The widely used equipment is listed below:
- Pipe Jacks
- Adjustable Pipe Rollers
- Welding Machine
- Pipe Rigging and transport equipment
- Chain Clamps/ C Clamps
- Pipe Fit-up Tools
- Pipe Purging Equipment
- Pipe Cutting and Bevelling Equipment
- Torque Wrench/Adjustable Wrench/Combination Wrench/Hammer Wrench
- Flange Alignment Tools and Pins
- Center Punch
- Compass/Contour Marker
- Pipe Threader
- Fork Lift
- Grinder
- Wraparound Tapes
- Hydraulic Crane/Tower Crane
- Pipe Bending Machine, etc
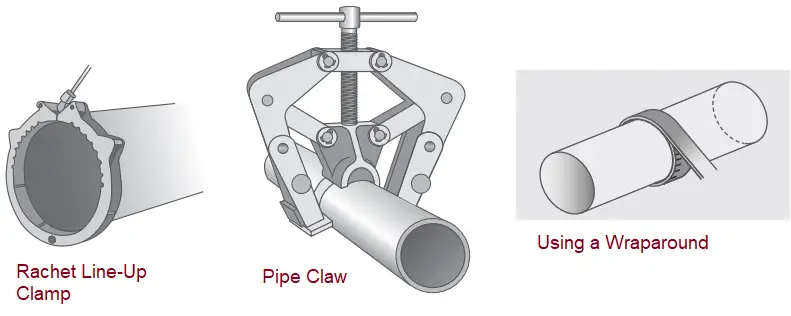
Preparation for Pipe fabrication
In this stage, pipe fabricators are required to calculate various parameters from the drawing specifications. They are required to take into consideration welding and tack welding processes along with any distortion that may arise from welding. The tools required for the fitting-up of pipes and flanges, such as pipe supports and clamps will also need some thought. Then they need to prepare a simple wire model of the pipe spool from the drawings. Material take-off and the client’s fabrication specification are also supplied to the pipe fabricators.
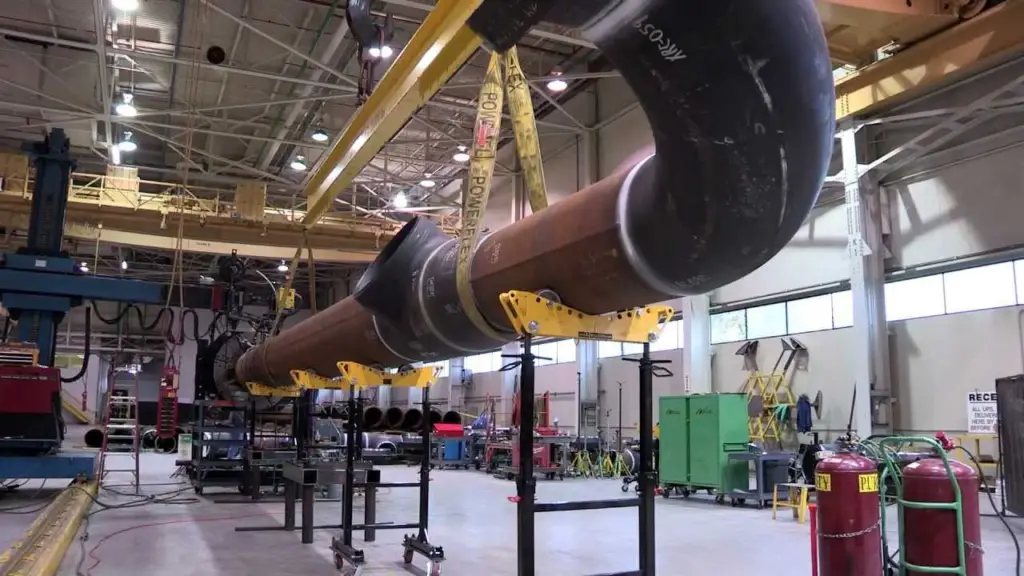
Piping Fabrication Procedure
The pipe fabrication process requires assembling pipes and pipe fittings according to the spool drawing. Pipe fabricators must take into consideration the size of the assembly, as transportation could be a problem. In such cases, Sub-assemblies are an effective way of transporting large projects. Piping fabrication is done as per the below-mentioned steps:
- Marking and Cutting: As per the design drawing requirement, Marking shall be done and the same shall be verified by the concerned supervisor prior to cutting. Pipe cutting is normally done as follows:
- Carbon Steel pipes – By gas cutting & grinding.
- Alloy Steel pipes – By grinding or flammable cutting.
- Stainless Steel Pipes – By grinding or plasma cutting.
- Tagging: Using dye stamping, Paint marking, or Tagging, pipe heat numbers are transferred to the cut pieces before cutting the pipe.
- End Preparation: In the next step, End preparation (bevelling) and fit-up are done following an approved Specification and WPS.
- Welding Pipes: Extra precautions must be exercised to ensure that longitudinal seams on the joining pipes do not come in one line in a butt-welded joint. Seams must be staggered at least 100 mm apart and also will clear the branch connections. Care is taken to make sure that longitudinal seams are not resting on the steel structure.
- Welding Pipes and Fittings: Pipes and Fittings for fit-up are then placed on a temporary pipe bed and supports are properly secured properly. Next, the arrangement is inspected for quality Fit-Up. Once inspection clearance is received, Joints are welded by qualified welders.
- Details Marking: Various details line pipeline No., Component Heat No., Joint No., Fit-up inspection signature, Welder No., Visual inspection signature, and welding date are marked near the joint using a metal paint marker.
- The pipe Spool Number is marked with a paint marker and an aluminum tag is tied to the spool.
- Heat treatment: As per project-specific requirements, Preheating and PWHT will be done at the shop or field.
- Fabricated pipe spools are then shifted from the pipe fabrication shop to the laydown area.
- Inspection: As per the requirement of the project specification or guidelines, NDT is performed. Once NDT clearance is received, spools are released for erection/painting with a release notice.
- Spools rejected in the NDT process are identified with yellow and black tags and sent for repair work. NDT has performed again on the repaired weld areas as required.
- Documentation: After painting, field inspection is executed for QC and the same is recorded in the prescribed format. After the painting inspection, the spool is released for erection.
- Fabrication of Stainless Steel Pipes: Stainless Steel piping fabrication is normally done in the shop with an isolated area from carbon steel and alloy steel. The equipment and tools which are used for CS fabrication shall not be used for SS. Tools for SS must be differentiated clearly by marking “For Stainless Steel” only. For Stainless steel materials, stainless steel tools will be used for grinding, brushing and clamping, etc.
- Protection: For the protection and temporary storage till the erection, all flanged raised faces of completed pipe spools are fitted with plywood blinds and spool ends shall be fitted with proper caps.
Pipe Fabrication Shop
The pipe fabrication Shop is basically a workshop where all the prefabricated pipe spools are developed. All the pipe works for spool preparation are normally performed inside this shop using highly skilled pipe fabricators. Generating pipe spools in the Pipe Fabrication shops is the best economic way for reducing site installation costs for big-size projects. All equipment, tools, and manpower are available in the pipe fabrication shop and pipe spools are produced with high quality.
Pipe Fabrication Specification
Pipe fabrication Specification is an engineering document that provides all guidelines to be followed by pipe fabricators for spool pipe fabrication. The specification for piping fabrication provides the minimum requirement of preparation of detail shop drawings and the fabrication, requirements for inspection and testing. It lists all applicable codes and standards.
Respected sir
My Name is Patel Ranjitkumar Arvindbhai I’am not piping engineer My Professional tred as PIPE FITTER / PIPE FABRICATOR I have more then 20thYears Piping Experience just now I Comment (1) What is the difference between pipe and tube ?
* pipe is identified by NB and thickness is defined by schedule
* Tube is identified by OD & it’s thickness
(2) from which size onwards NB of pipe is equal to OD of pipe ?
* From the size 14″and onwards NB – OD of pipe
Thanks and best regards
Ranjitkumar A Patel
Mob : +91 9512490855
Sr can u send me the detail of piping work
hello Aman Kumar i hope you and your family keeping well i do have campany call remistar we do NDT exsamles xrays mt pt
Dear Mr.Dey,
Thank you very much for posting this.
Eagerly awaiting for your next post.
I am a mechanical contractor and done various mechanical job but specially pipeline.
Regards and Thanks,
Surinder Mitra.
Kolkata.
I am a Japan trained Gas Pipe bevelling & welding consultant based in Pune offering novel equipment from Japan & Korea
Sir, I working two years fabrication department &and also acknowledge about ndt-2 level .l have loss job due to covid-19 any job you can help me.
Mr Dey,
Nice information given by you hope you will send next in future the information about flow and pressure
I’m GRE GRP FOREMAN
I Have Experience 12 Yrs
Lose Job Due To Covid-19 Have You Any Required Confirm Me So Thanks
We are looking for a Trainer – Pipe Fitter & Fabricator, Trainer – Pipe Welder for a Training Institute
Location Navi Mumbai Turbhe, interested may connect 8452067576
Thanks for your post. I’ve recently joined shop fabricated pipe industry and have got a lot of things to learn.
Your post is well orgnised and easy to disgest. Thank you so much !
Thanks for posting this helpful blog.
I want to ask about field weld and site weld, field weld have extra length 150mm for adjustment how about site weld, have spooling or not. please advice .tq sir