Corrosion is the natural enemy of steel pipes, threatening their structural integrity, lifespan, and overall performance. As the backbone of many industries, from oil and gas to water distribution, ensuring the longevity of steel pipes is paramount. Anti-corrosive coatings and linings are a formidable solution that safeguards steel pipes against the relentless forces of corrosion. In this article, we’ll dive into the world of anti-corrosive coatings and linings, exploring their importance, types, application methods, and benefits.
What is an Anti Corrosive Coating?
An anti-corrosive coating is a specialized type of protective material applied to the surface of a substrate, typically metal, to prevent or significantly reduce the occurrence of corrosion. Corrosion is a natural process in which metals degrade due to chemical reactions with their surrounding environment, such as exposure to moisture, chemicals, and atmospheric elements. Anti-corrosive coatings create a barrier between the metal surface and its environment, acting as a shield to inhibit or slow down the corrosion process. These coatings are designed to resist the effects of various corrosive agents, thereby extending the lifespan and maintaining the structural integrity of the coated material. The anti-corrosive coating is also known as the anti-rust coating.
What is an Anti Corrosive Lining?
An anti-corrosive lining refers to a protective layer or material applied to the interior surfaces of a substrate, often pipes or containers, to prevent or mitigate the effects of corrosion caused by contact with corrosive substances. Unlike anti-corrosive coatings that are applied to the exterior surfaces, anti-corrosive linings are specifically designed to withstand the challenges posed by the materials being transported or stored within the substrate. These linings create a barrier that shields the substrate from chemical reactions, abrasive agents, and other factors that could lead to corrosion, ensuring the integrity, safety, and longevity of the substrate and its contents. Anti-corrosive linings are widely used in industries where the transported materials are corrosive or abrasive, such as chemicals, petrochemicals, and mining.
Advantages of Anti-Corrosive Coating and Lining
Anti Corrosive Coatings on Steel are widely used to protect the pipes from corrosion. The protective coating layer helps the steel material to prevent corrosion and increase the useful life of the material. Anti-corrosion coatings are one of the most effective and economical options for tackling corrosion. Corrosion-resistant anti-corrosive coatings serve the following purposes:
- Protect metal surfaces from degradation due to oxidation, and moisture.
- Prevents direct contact with environmental chemical hazards.
- Acts as a barrier from corrosive materials.
- Prolong the structural life along with increasing their efficiency.
- Provides chemical protection, abrasion resistance, etc.
- By preventing leaks and failures, anti-corrosive solutions contribute to environmental protection by minimizing the potential release of hazardous materials.
- Coated pipes maintain optimal flow efficiency, ensuring the smooth transportation of liquids or gases without obstructions caused by corrosion buildup.
For industries like oil and gas, chemical, petrochemical, infrastructure, marine, power generation, etc., the use of anti-corrosive coatings and linings has become a necessity to safeguard the huge investments in terms of money, property, and safety of workers. The demand for high-performance anti-corrosion coatings is increasing day by day. Before jumping into the core of anti-corrosive coating and lining types, let’s learn a few words about Corrosion.
Corrosion in the Oil and Gas Industry
Corrosion in the Piping and Pipeline Industry is quite common. Corrosion is a loss of material due to “REACTION” with the environment.
- Physical: erosion
- Chemical: irreversible loss
- Electro-chemical: electric microcell
- Biological: bio-fouling
Forms of Corrosion
Corrosion manifests in different forms as listed below:
- Erosion: commonly observed in lead-lined vessels; area of the vessel near the impeller
- Pitting: micro holes in the relatively unattacked surface
- Selective leaching: dezincification of Cu-Zn alloy
- Intergranular: welding or improper heat treatment
- Stress corrosion: welding, cold work, etc.
- Crevice corrosion: electrochemical cell in the crevice
Points to remember
- The steel surface for coating must be as clean as possible.
- The metal surface must not have scratches.
- The anti-corrosive coating itself must be environmentally friendly.
Types of Anti-Corrosive Coatings
A wide variety of anti-corrosive coatings are available in the market to suit the performance requirements of a specific application. Therefore, the selection of anti-corrosion coatings is not an easy process. Various parameters need to be ensured during anti-corrosive coating selection. Sometimes, the coating manufacturer needs to be consulted for some specific information.
Depending on the materials used, an anti-corrosive coating can be categorized into the following types
- Natural Paints
- Epoxy
- Polyurethane
- Synthetic Resins
- Plastics
- Phenolic
- Composites
- Alkyd
Again, depending on the anti-corrosive coating application they can be divided into two groups:
- Anti-corrosive coatings for new pipes, and
- Anti-corrosion coatings for maintenance and repair work.
Based on the application of the coating on the piping surface they can be classified as
- Internal Pipe Coatings, and
- External Pipe Coatings
The specific application dictates the type of anti-corrosion coating to be used.
Epoxy Coatings:
Epoxy coatings are renowned for their exceptional adhesion and resistance to various chemicals. They create a dense, protective layer on the pipe’s surface, shielding it from corrosion caused by exposure to chemicals, moisture, and abrasive substances.
Polyurethane Coatings:
Polyurethane coatings provide outstanding resistance to UV radiation, making them ideal for outdoor applications. They are often used in combination with epoxy coatings for enhanced protection against both chemical and environmental factors.
Zinc Coatings:
Zinc coatings, such as galvanization, involve applying a layer of zinc onto the steel surface. This sacrificial layer corrodes before the steel does, extending the life of the pipes. This method is commonly used for pipes exposed to high moisture levels.
Fusion-Bonded Epoxy (FBE) Coatings:
FBE coatings are known for their robustness and resistance to mechanical damage. They are applied as a powder and heated to form a strong bond with the steel surface. FBE coatings excel in pipelines that transport oil, gas, and water. The following video explains the process of coating a pipe using FBE coating and 3LP coating.
Types of Anti-Corrosive Linings
- Anti CorrosionLining:
- Fiber Reinforced Plastics
- Glass lining
- Graphite
- Rubber
- PE/HDPE Lining
- Roto Lining
Rubber Lining as an Anti-corrosive agent
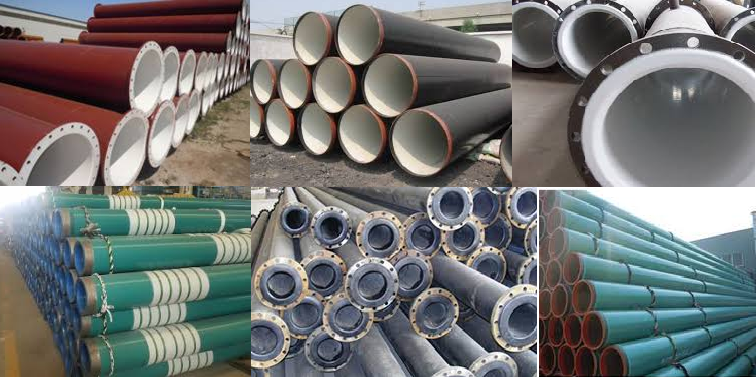
Types of Rubber Lining:
- Natural Rubber
- SBR
- Neoprene(Polychloroprene)
- Butyl (isobutylene)
- Halogenated Butyl – e.g. Chlorobutyl
- Bromobutyl
Applications of Rubber Lining:
Neoprene
- Resistant to acid, abrasion, oil, and seawater.
- High temperature and corrosive service, where natural rubber fails.
Butyl Rubber
- Used for High-Temperature Corrosive service e.g. Reaction vessels
- For Hot and abrasive services
Applications
- Chlor-Alkali Plant
- Phosphoric Acid Plant
- DI water plants
Fluoropolymer Coatings & Linings
Anti-corrosive fluoropolymer coatings offer a blend of high-performance resins and fluoropolymer lubricants. Consisting of a dry film lubricant, fluoropolymer coating generates a smooth, hard, and slick final coating to provide excellent corrosion and chemical resistance.
Advantages of Fluoropolymer Anti-corrosion Coatings & Linings
Anti-corrosion fluoropolymer coatings also provide the following advantages:
- resistance to galling
- non-wetting surface
- reduced friction
- non-stick surface
- electrical resistance and
- abrasion resistance.
- Chemical inertness against nearly all substances
- Broad application temperature range (-30oC to 260oC)
- Very smooth material surface and anti-sticking behavior
- Possibility of being electrically conductive
- Impact-resistant
- Absorbs pressure variations or impacts
- Vibration decreasing
- Insensitive to UV light
- No softening agents used
- Weather-resistant and approved for food and drugs service
Because of so many benefits, the application of fluoropolymer coating is extensive. Typical examples of anti-corrosive fluoropolymer coating and lining are
- PFA – PERFLUROALKOXY
- FEP – FLUORINATED ETHYLENE PROPYLENE
- ETFE – ETHYLENE TETRAFLUOROETHYLENE
- ECTFE – ETHYLENE CHLOROTRIFLUORO ETHYLENE
- PVDF – POLYVINYLIDENE FLUORIDE
- PP – POLYPROPYLENE
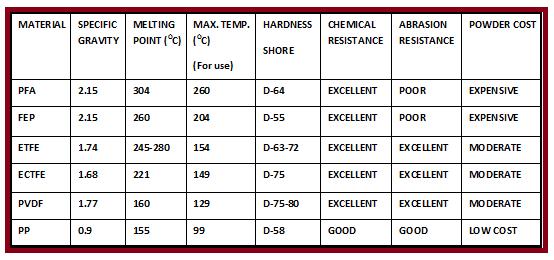
Advantages of High-Build Coatings
- Drastically reduces permeation through the coating and possible corrosion of the metal substrate.
- It lowers the metal content of the fluid being handled due to the reduction of permeation, substrate corrosion, and back migration of corrosion products.
- Extends the life of the coating when exposed to abrasive media
- Thick coatings can be repaired by welding if mechanically damaged. Thin coatings (<20mil) must be stripped and recoated if repairs are not possible.
- Thick coatings operate better under pressure-vacuum cycling than thin coatings.
- The cost of a thick coating is not directly proportional to its thickness. Longer online performance is achieved at only a small additional cost with high-build coatings. Less maintenance is an important benefit.
- No welds exist with a high-build coated vessel in comparison to one that is sheet-lined. Welds in sheet-lined vessels are a known point of failure.
- Used in all chemical processes with hazardous, corrosive, abrasive and-or toxic media.
- Well-established in the chemical, pharmaceutical, and petrochemical industry
- Ideal in any plant because of their good chemical and physical resistance and long lifetime in service.
- Absence of sensibility against:
- -mechanical impact
- -alternating pressure
- -vibration
- -temperature shock
- -aging
Application of High-Build Coatings
Typical applications of anti-corrosion high-build coatings are
- Mixed beds
- Water storage tanks
- Pumps
- Piping
- Chemical storage tanks
- Valves
- Chemical day tanks
- Filter housings
- Wet bench components
- Vacuum de-gasifiers
- Agitators
- CMP components
Anti-Corrosive Coating Selection Criteria
The parameters that must be considered while selecting a suitable anti-corrosive coating are
- Chemical exposure
- Permeability of the coatings to the materials to be processed
- Pressure if handling gaseous materials
- Purity, FDA, and USDA requirements
- Maximum operating temperature
- Abrasives, if present
- Cost
- Vessel configuration – dimensions, complexity
- Desired fluoropolymer
- Thickness of lining
- Reparability
- Track record
Anti-Corrosive Coatings And Linings thickness selection criterion
- If the corrosion rate of carbon steel is > 10 mpy (mills per year)-USE THICK LININGS
- If the corrosion rate of carbon steel is < 10 mpy (mills per year)-USE THIN LININGS
- THICK LININGS – >25MILS OR 0.635MM
- THIN LININGS – < 25MILS OR 0.635MM
Coatings-Linings thickness selection criterion
Use Thin Lining For
- Product purity
- Nonstick
- Localized corrosion
Use Thick Lining for
- Corrosion prevention
- Permeation resistance
Difference Between Coating and Lining: Coatings Vs Linings
Coating and lining are two methods of protecting surfaces from corrosion, erosion, abrasion, and other forms of degradation. The main differences between these methods are:
- Purpose: The purpose of the coating is to provide a protective layer on the surface of a substrate, such as metal, concrete, or wood, to prevent it from coming into contact with the environment or the substance being transported through a pipeline. The purpose of lining is to provide a barrier between the substance being transported and the surface of the substrate, to prevent it from reacting with the substrate and causing damage or contamination.
- Material: Coatings are typically made of materials such as paint, epoxy, polyurethane, or thermoplastic, while linings are usually made of materials such as rubber, PVC, or fiberglass-reinforced plastic (FRP).
- Application: Coatings are usually applied to the surface of a substrate using methods such as spraying, rolling, or brushing. Linings are applied to the interior surface of a substrate using methods such as pouring, spraying, or casting.
- Thickness: Coatings are typically thinner than linings and are applied in a single layer, while linings are thicker and may be applied in multiple layers to achieve the desired thickness and strength.
- Substrate: Coatings are used on a wide range of substrates, including metal, concrete, wood, and plastics, while linings are primarily used on substrates that are in contact with corrosive or abrasive substances, such as pipelines, tanks, and vessels.
In summary, the main differences between coating and lining are their purpose, material, application method, thickness, and substrate. Coatings provide a protective layer on the surface of a substrate to prevent it from coming into contact with the environment or the substance being transported, while linings provide a barrier between the substance and the surface of the substrate to prevent it from causing damage or contamination.
Other differences between pipe coating and pipelining are
- In terms of Thickness:
- Coatings – 10 to 1500 microns (0.01 to 1.5mm)
- Linings – 3000 to 5000 microns (3 to 5 mm)
- The coating can be done from outside and inside but the lining is done only inside the pipe.
- Lining in a pipe means a pipe inside a pipe, but the pipe coating is not the same.
Coatings are better than linings for the following:
- adhesive forces
- vacuum application
- heat transfer
- thermal shock
Internal Pipe Coating vs External Pipe Coating
The main differences between internal pipe coating and external pipe coating are:
- Location: Internal pipe coating is applied on the inside surface of the pipe, while external pipe coating is applied on the outside surface of the pipe.
- Purpose: Internal pipe coating is primarily used to protect the inside of the pipe from corrosion, erosion, and abrasion, as well as to improve the flow of fluid or gas. External pipe coating is primarily used to protect the outside of the pipe from corrosion, UV radiation, and physical damage.
- Material: The materials used for internal pipe coating are typically different from those used for external pipe coating. Internal pipe coatings are usually made of materials such as epoxy, polyurethane, or polyethylene, while external pipe coatings are typically made of materials such as polyethylene, polyurethane, or coal tar epoxy.
- Application: Internal pipe coating is applied using specialized equipment that sprays or brushes the coating onto the interior surface of the pipe, while external pipe coating is typically applied using methods such as brushing, rolling, or spraying.
- Thickness: The thickness of internal pipe coating is typically thinner than that of external pipe coating, as it only needs to provide a protective layer to the inside surface of the pipe. External pipe coating may be thicker to provide additional protection against external damage.
In summary, the main differences between internal pipe coating and external pipe coating are their location, purpose, materials, application methods, and thickness. Internal pipe coating is used to protect the inside of the pipe and improve fluid or gas flow, while external pipe coating is used to protect the outside of the pipe from corrosion, UV radiation, and physical damage. The materials used, application methods, and thickness may also differ between these two types of coatings.
Conclusion
The battle against corrosion in steel pipes is ongoing, but with anti-corrosive coatings and linings, industries can gain the upper hand. By implementing the right solution for the specific environment and application, steel pipes can be shielded from the damaging effects of corrosion, leading to prolonged service life, enhanced efficiency, and cost savings. As technology continues to advance, the development of even more effective and sustainable anti-corrosive solutions holds the promise of a corrosion-resistant future for steel pipelines across various industries.
Few more useful Resources for you…
An Article on Forms of Corrosion
Corrosion under insulation: A Presentation
Corrosion Protection for Offshore Pipelines
Corrosion Monitoring Techniques & Surveys: A short Presentation
Guide for Coating Selection for External Bolting to Reduce Corrosion
Application of Anti-Corrosive Linings in Oil and Gas Industry
Anti-Corrosive Composites for Oil and Gas Industry
Can give me your whatapp contact ?