What are Composites?
Composites are novel materials made by combining two or more materials, the resultants of which possess the combination of better properties of the ingredients.
Constituents of composites
- Base material – Matrix – metal, ceramic, or polymer
- Reinforcement – e.g. fiber
- Fillers
Dual Laminate Composite
- Thermoplastics lined to thermosets e.g. PVC-FRP, CPVC-FRP, PVDF-FRP, ECTFE-FRP, PP-FRP, FRP-FRP
- FRP – made of fiberglass impregnated with either –
- Unsaturated polyester resin
- Vinyl ester resin
- Furan resin
- Fiberglass – provides structural stability
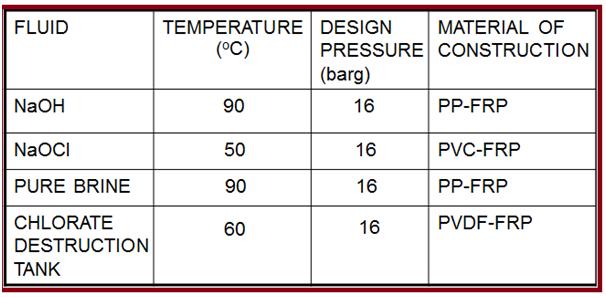
Various other combinations of Composites
- FRP-Polymer Concrete
- FRP-Steel
- FRP-Concrete
- Thermoplastic reinforced cement concrete
- Thermoplastics on Steel
FRP-Polymer Concrete
- Unsaturated polyester resin filled with quartz
- Cast like concrete in molds
- High compressive strength
- High corrosion resistant
- High impact strength
Application: used for electrolytic cells in copper refineries replacing lead-lined RCC cells
Fibre Reinforced Composites
Glass is the chief reinforcement used for composite materials in chemical process industries.
Mostly in the form of GRPs
- S-glass – for high strength
- C-glass – corrosion resistant
- Carbon fibers – superior mechanical properties, low density, and corrosion resistance used for offshore oil field applications
- For some strength: CFRP composite
- 80% lighter than steel
- 60% lighter than aluminum
Applications of GRP composites
Resistant to most chemicals including acids, where metals like SS and Ni-alloys fail to survive Also handle lethal and corrosive Chlorine gas, halide salts, and bleaching solutions including hypochlorite Unlike metals can withstand wide fluctuations in pH and temperature. E.g. effluent treatment process Resistant to corrosion in damp soil conditions, oxidizing and reducing agents such as H2S
Industries served
- Water and waste-water treatment
- Pulp & paper
- Food/chemical processing
- Mining-mineral recovery
- Microprocessor manufacturing
- Pharmaceutical
- Power generation
Chemical Industry Applications
- Piping
- Chimney and Stacks
- FGD applications
- Offshore applications
- Storage tanks and Pressure vessels
- Composites are attractive for this application due to the following parameters:
- Corrosion resistance, strength & ease of fabrication
- Installed cost as compared to SS or CS-lined e.g. CNG tanks
Dimensions:
- Diameter: 1 to 10m
- Wall thickness: 5 to 50mm
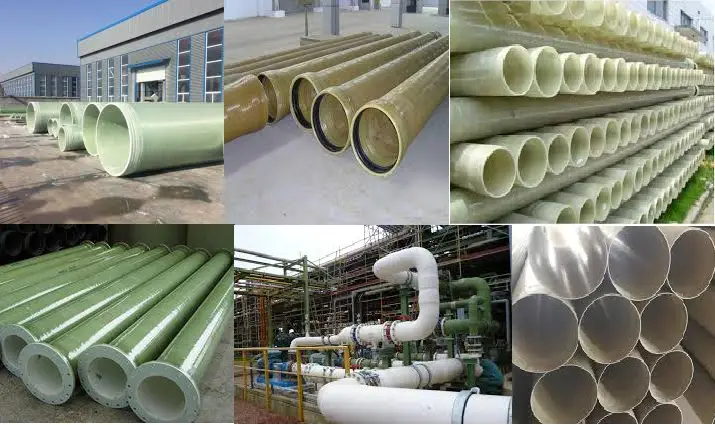
Composite Piping
- GRP piping applications include
- Potable water distribution
- Firewater systems
- Cooling water lines
- Handling De-mineralized water
- Effluent systems
- High-pressure pipelines handling aggressive media such as saltwater, oil, or brine
- Unsaturated polyester, vinyl ester resin used for chimneys and Stacks.
- Can withstand high temperatures (up to 240 Degrees C) and severe corrosive gases
- Carbon fiber reinforcements and epoxy resins are used only in selective cases, wherein high strength and light weight are more important than corrosion resistance.
- Deep well platforms – tension leg platforms(TLPs)
- spars and drilling risers
- choke and kill lines
Offshore Applications
- Secondary structures including ladders, handrails, and gratings
- Flow and gathering lines
- Firewater lines
- Casings
- Surface injection
- Saltwater disposal lines
- CO2 handling
- Tank battery piping
Materials used in Offshore composites
Bisphenol(A) polyester, bisphenol vinyl ester, Novalac epoxy, and phenolics – Fire retardant
Summary
Glass fiber-reinforced composites are being selectively used in chemical processes and oil & gas industries for the following advantages:
- Exceptional freedom of design and manufacture of many complex shapes.
- Outstanding durability even in extremely harsh environments
- A custom selection of resin and reinforcements
- Superior strength and stiffness-to-weight ratios
- Highly corrosion resistant in almost every chemical environment
- Lower maintenance and replacement costs
Glass Lining
Glass
- Inert, hard, and biologically inactive
- Can be formed into a very smooth and impervious surface
- Brittle in nature
Types of Pfaudler Glass
- World Wide Glasteel 9100
- Pharma Glass PPG
- Stainless Steel Glass 4000
- Ultra Glass-6500
- Anti-static Glass
World Wide Glasteel 9100
- Offers an unmatched combination of
- Corrosion resistance
- Impact Strength
- Thermal shock resistance
- Non-adherence
- Heat transfer efficiency
Stainless Steel Glass 4000
- Reliable glass lining of stainless steel for pharmaceutical / FDA applications
- Suitable for cryogenic processes & pure products for electronics
- A virtually inert glass that resists corrosion, abrasion, and product adherence
Pfaudler Ultra Glass
- Addresses the requirement of chemical reactions at high temperatures
- Enhanced thermal tolerance up to 343 Degrees C – an improvement over WWG 9100
- Extended thermal shock protection for faster heating and cooling
Limitations:
- Operating temperature
- Chemicals
- Cavitation
- Electrostatic discharge
- Abrasion
FRP
What is FRP?
FRP is a resin lining into which layers of Fibers are incorporated to optimize lining structure capability and performance.
Types of FRP
- Glass Fiber Reinforced Plastics (GFRP)
- Carbon Fiber Reinforced Plastics (CFRP)
- Polymer (Aramid) Fiber Reinforced Plastics (PFRP)
Why FRP?
- FRP is widely used because of its relatively low cost, good chemical resistance, and its mechanical properties:
- Specific tensile strength (GPacm3/gm) – Tensile strength per unit density
- Specific stiffness (GPacm3/gm) – Tensile modulus per unit density
Scope of Use of FRP
- The bottom lining of AST
- Piping
- Automotive
- Naval
- Aerospace
Why tank lining?
- An effective method for preventing internal corrosion in storage tanks
- Maintaining the stored chemicals’ purity and quality
- The long lifetime for storage tanks
- To overcome tank bottom perforations due to external corrosion
Graphite
Impervious Graphite is a traditional material selected for high conductivity, chemical resistance, and good mechanical properties. It is specially treated with synthetic resins to ensure that the base structure is fully impervious to liquids under pressure.
Graphite forms no compounds due to corrosion, and no surface films as do many metals. Hence graphite surface remains smooth and more resistant to scale build-up.
Graphite lining can replace most of the other types of linings due to:
- Better thermal conductivity
- Superior chemical corrosion resistance. Corrosion loss is < 0.05mm/yr
- Lower initial/lifetime costs
- Has higher temperature applications compared to all the polymeric linings except for the PTFE family
- The trouble-free operating life of approx. 5 yrs
- Can be used for lining very large size equipment
Regularly available equipment with graphite
- Reaction vessels
- Heat exchangers
- Falling film absorbers
- Acid dilution units
- Tail gas scrubbers
- Raschig rings
- Dry HCL gas handling equipment
- Impervious graphite tiles
Patch repairs: Can be repaired easily as compared to other linings, especially glass lining.
Few more useful Resources for you…
An Article on Forms of Corrosion
Corrosion under insulation: A Presentation
Corrosion Protection for Offshore Pipelines
Corrosion Monitoring Techniques & Surveys: A short Presentation
Guide for Coating Selection for External Bolting to Reduce Corrosion
Application of Anti-Corrosive Linings in Oil and Gas Industry
Hello ..help me out !,
We are interested find solutions for large (old pipes ) inside coating,lining from 50km (municipality/district / large project )
Pipes are running at 4-6 Bars and 110C
Diameters from 400mm –900mm
Status :10-30 years old liking is possible thickness >6mm
Please send us your technical solution ,certifications technology materials equipment ,projects/references etc.
We are interested for the equipment ,technology materials supply .
Thanks Aurel Ispas
Phone/Whasshap : +40742112575
WeChat : aurelispas
Email : aurel@ok.ro
https://www.instalservice.ro/