Pressure Gauges are pressure measuring instruments. Pressure and Temperature are two very important parameters for all chemical industries. So, pressure measurement is of utmost importance. There are various pressure-measuring instruments available to perform this task. Pressure measurement basically means the analysis of the fluid forces that are imparted on a surface. The accuracy of pressure-measuring instruments is very important for proper operational control. In this article, we will explore various pressure measuring devices or pressure gauges used across industries.
What is a Pressure Gauge?
A pressure gauge is a device used to measure the pressure of a fluid or gas in a closed system. It typically consists of a Bourdon tube, which is a curved tube that is connected to the system being measured. When the pressure inside the system changes, the Bourdon tube flexes and moves a pointer on a dial, indicating the pressure reading.
Pressure gauges are used in a wide range of applications, including industrial processes, heating and cooling systems, automotive and aerospace systems, and medical devices. They come in various sizes, types, and accuracy levels, and can measure different units of pressure such as psi (pounds per square inch), kPa (kiloPascals), bar, and mmHg (millimeters of mercury).
Proper calibration and maintenance of pressure gauges are important to ensure accurate and reliable readings. Depending on the application, pressure gauges may need to meet specific industry standards and regulations, such as those set by the American Society of Mechanical Engineers (ASME) or the International Organization for Standardization (ISO).
Uses of Industrial Pressure Gauges
Industrial pressure gauges are used in a wide range of applications to measure the pressure of fluids or gases in a closed system. Some common uses of industrial pressure gauges include:
- Process control: Pressure gauges are used in industrial processes to monitor and control the pressure of fluids and gases in pipes, tanks, and vessels.
- Safety: Pressure gauges are used to ensure that systems are operating within safe pressure limits. This is important to prevent system failure, equipment damage, and worker injuries.
- Quality control: Pressure gauges are used in manufacturing processes to ensure that products are produced to specific pressure requirements.
- Maintenance: Pressure gauges are used during maintenance and troubleshooting to diagnose problems with industrial systems and equipment.
- Research and development: Pressure gauges are used in research and development to measure pressure changes during experiments and simulations.
- Environmental monitoring: Pressure gauges are used to measure pressure changes in environmental monitoring systems, such as weather stations and air pollution sensors.
Industrial pressure gauges come in different types, sizes, and accuracy levels, and are used in a variety of industries, such as oil and gas, chemical processing, pharmaceuticals, food and beverage, and manufacturing.
Pressure Gauge Working Principle
The working principle of a pressure gauge is based on the mechanical deformation of a sensing element in response to the applied pressure. The sensing element is usually a Bourdon tube, which is a curved metal tube with an elliptical or spiral shape.
When pressure is applied to the inside of the Bourdon tube, it causes the tube to straighten out slightly. This deformation is transferred to a mechanical linkage, which causes the movement of a pointer on a dial to indicate the pressure reading.
The degree of deformation of the Bourdon tube is directly proportional to the pressure applied, so the pressure gauge can accurately measure the pressure of the fluid or gas being measured.
Other types of sensing elements used in pressure gauges include diaphragms, bellows, and capsules, which all work on similar principles of mechanical deformation in response to pressure.
The accuracy of a pressure gauge depends on a number of factors, including the design of the sensing element, the quality of the materials used, and the calibration of the gauge. Calibration is important to ensure that the pressure gauge provides accurate readings over the range of pressures it is designed to measure.
What is Pressure?
- Pressure (P) is defined as Force (F) per Unit Area (A).
- Pressure is the action of one force against another force.
- The pressure is the force applied to or distributed over a surface.
- P = F/A F: Force A: Area
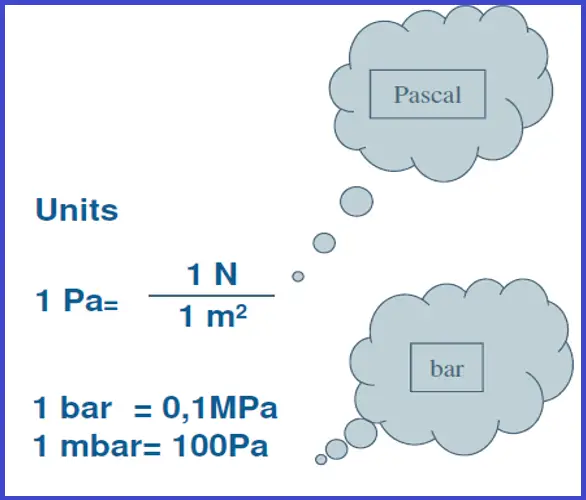
Absolute pressure
- Measured above total vacuum or zero absolute.
- Zero absolute represents a total lack of pressure.
- Range: 0-1 Kg/cm^2 (a)/ 0-1 Bar (a)/ 0-760 mm Hg (a)
Atmospheric pressure: The pressure exerted by the earth’s atmosphere.
Barometric pressure: Same as Atmospheric pressure.
Vacuum Pressure: Pressure below atmospheric.
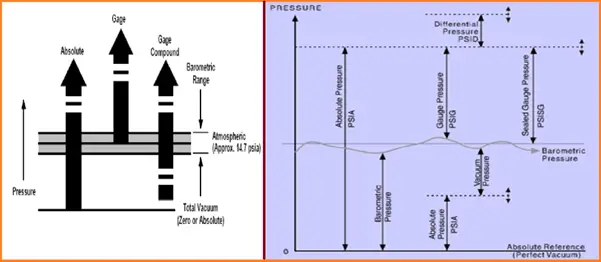
Differential pressure: It is the difference in pressure between two points of measurement. In a sense, Absolute Pressure could be considered as a differential pressure with a total vacuum or zero absolute as the reference.
Gauge/Gage pressure: The pressure above the atmosphere is gauge pressure. Represents a positive difference between measured and existing atmospheric pressure. For example – Blood pressure.
Pressure Gauge Formula
The pressure gauge formula is: P = F/A
Where: P = Pressure in Pascals (Pa) F = Force in Newtons (N) A = Area in square meters (m^2)
In this formula, pressure (P) is equal to the force (F) applied per unit area (A). This means that the pressure is directly proportional to the force and inversely proportional to the area.
The pressure gauge formula can be used to calculate the pressure of a fluid or gas by measuring the force applied to a sensing element, such as a Bourdon tube, and dividing it by the area of the sensing element. The resulting pressure can be displayed on a dial or digital readout in units such as pounds per square inch (psi), bar, or kilopascals (kPa), depending on the gauge’s calibration.
Pressure Measurement
The measurement of pressure is considered the basic process variable for measurement of:-
- Flow (difference of two pressures).
- Level (Head or backpressure).
- Temperature (Fluid pressure in a filled thermal system).
The Pressure Measurement System consists of two basic parts:-
- A primary element, which is in contact, directly or indirectly, with the pressure medium and interacts with pressure changes.
- A secondary element translates this interaction into appropriate values for indicating, recording, and/or controlling.
Common Units of Pressure Measurement
Pressure can be measured using various units depending on the system of measurement and the application. Here are some of the most common units of pressure measurement:
Pascal (Pa):
- The SI (International System of Units) unit of pressure.
- 1 Pascal is equal to 1 Newton per square meter (N/m²).
- It is a small unit and is often used for precise scientific measurements.
Kilopascal (kPa):
- Equal to 1,000 Pascals.
- Commonly used in engineering and everyday applications.
Bar (bar):
- Equal to 100,000 Pascals (100 kPa).
- Frequently used in Europe for expressing pressure in various contexts.
Atmosphere (atm):
- Represents the average atmospheric pressure at sea level on Earth.
- Approximately 101.3 kPa or 1.01325 bar.
Millimeters of Mercury (mmHg or Torr):
- Originally based on the height of a column of mercury in a barometer.
- 1 mmHg is approximately 133.322387415 Pa.
Pounds per Square Inch (psi):
- Commonly used in the United States and some other countries.
- 1 psi is approximately 6,894.76 Pa.
Pound-Force per Square Inch (lbf/in²):
- Similar to psi but includes the force component.
- Used in engineering and aviation.
- 1 lbf/in² is approximately 6894.76 Pa.
Technical Atmosphere (at):
- Equal to 1 kg-force per square centimeter (kgf/cm²).
- Used in some industrial contexts, especially in Germany.
Megapascal (MPa):
- Equal to 1,000,000 Pascals (1 kPa).
- Often used in high-pressure applications.
Newton per Square Millimeter (N/mm²):
- Equivalent to 1 Megapascal.
- Less common but used in some engineering applications.
Pound per Square Foot (psf):
- More commonly used in geotechnical engineering.
- 1 psf is approximately 47.88 Pa.
Inch of Water (in H2O):
- Used for measuring low pressures, such as in HVAC systems.
- Typically, 1 in H2O is approximately 248.84 Pa.
Decibar (dbar):
- Used primarily in oceanography and marine science.
- Equal to 1000 Pascals.
Millibar (mbar):
- Equal to 100 Pascals.
- Commonly used in weather forecasting.
Dyne per Square Centimeter (dyn/cm²):
- A non-SI unit of pressure is often used in older scientific literature.
- 1 dyn/cm² is equal to 0.1 Pa.
Classification of Pressure Measuring Instruments or Pressure Gauges
Pressure-measuring devices or pressure gauges can be classified on the basis of :
A: Pressure ranges:- Vacuum gage, Draft gage, Low range, compound gage, Medium range, high range, etc.
B: Design principle involved in their operation:
- Mechanical movement of the sensing element – e.g. Bourdon gages, Diaphragm gages
- Electronic Sensors: e.g. Strain gages, Capacitive, Potentiometric, Resonant wire, Piezoelectric, Magnetic, Optical, etc.
C: On the basis of their application:
- Local pressure indication,
- Remote pressure indication,
- Corrosive service
- Pulsating service
- Differential pressure measurement
Methods of Pressure Measurement
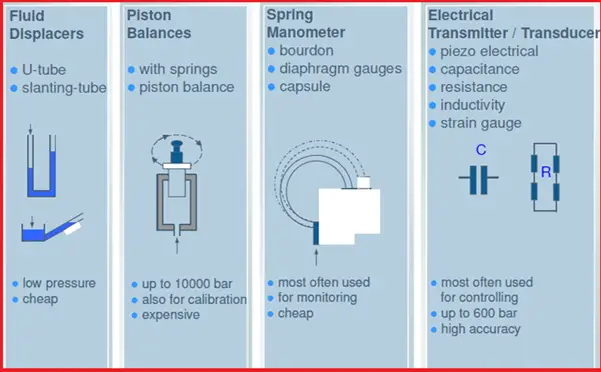
Basic Measurement – U Tube Manometer
A manometer is one of the oldest pressure-measuring instruments and is widely used even in recent times. Their operation is simple and provides accurate results. As the name suggests it is a “U” shaped tube made of glass and partially filled with liquid.
The principle of the manometer is given as P= HEIGHT*DENSITY Where “P” is Pounds /sq. Inch; “HEIGHT” in Inch “ DENSITY” in pounds /Cu. Inch
Advantages of Manometer
- Fluids are simple & time-proven
- High accuracy & sensitivity
- Wide range of filling
Disadvantages of Manometer
- No over-range protection
- Large & bulky
- Measured fluids must be compatible with the manometer fluids
- Need for leveling
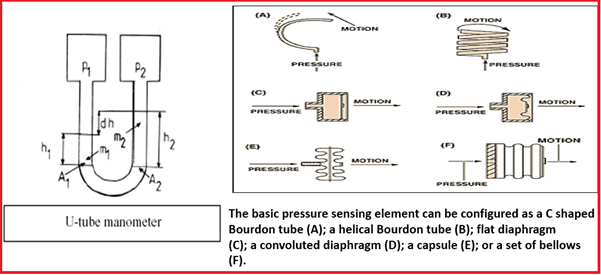
Pressure Sensing Elements
Pressure Sensing Elements are basically mechanical elements like plates, shells, and tubes. On the application of pressure, these elements deflect which is then converted into physical movement. They are a very important part of pressure-measuring devices.
- The main types of sensing elements are Bourdon tubes, diaphragms, capsules, and bellows.
- All the above devices, except diaphragms, provide a fairly large displacement. Mechanical gauges use that displacement which is further used by electrical sensors that require significant movement.
Bourdon Tube Pressure Gauges
The pressure measuring device, the Bourdon tube is the most common. They measure medium to high pressures. The Bourdon tube is basically a curved tube with a circular, coiled, or spiral shape.
- It is the twisted tube whose cross-sectional isn’t circular.
- Bourdon tube types are c-type, helical type, and spiral type.
- They should be filled with oil to limit the damage caused by vibration.
- Range: (-)1 to 1600 Kg/cm^2
Advantages of Bourdon Tube
- Low cost & simple construction
- Wide rangeability
- Good accuracy
- Adaptable to transducer designs
Disadvantages of Bourdon Tube
- Low spring gradient below 50psig
- Subject to Hysteresis
- Susceptible to shock & vibration
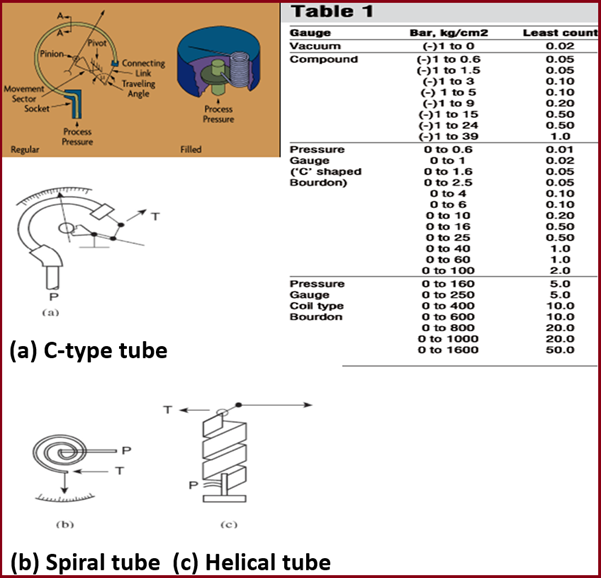
Bellows type Pressure Gauge
Bellows are also used as a pressure measuring instrument. Their main features are
- Made of Bronze, S.S., BeCu, Monel, etc..
- The movement is proportional to a number of convolutions sensitivity is proportional to size.
- In general, a bellows can detect a slightly lower pressure than a diaphragm.
- The range is from 0-5 mmHg to 0-2000 psi
- Accuracy in the range of 1% span
- It is a series of circular parts so formed or joined that they can be expanded axially by pressure. A wide range of springs is employed to limit the travel of bellows.
- The measurement is limited from .5 to 70 psi.
- It is greatly used as receiving elements for pneumatic recorders, indicators & controllers & also as a differential unit of flow measurement.
Advantages of Bellows Pressure Gauge
- High force delivered
- Moderate cost
- Good in the low to moderate pressure gauge
Disadvantages of Bellows Pressure Gauge
- Need ambient temperature pressure compensation
- Require spring for accurate characteristics
- Limited availability
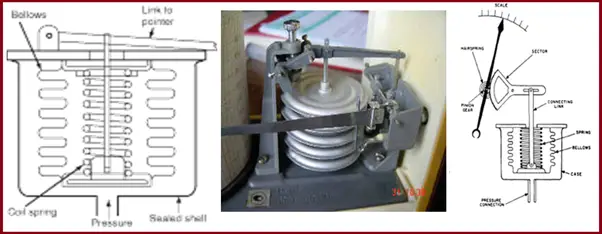
Diaphragm Pressure Gauge
The diaphragm can be used to measure the pressure of both liquids and gases. One circular diaphragm is clamped between a pair of flanges to constitute the pressure-measuring element.
- The deflection of a flexible membrane is used for pressure measurement.
- For known pressures, the deflection is repeatable. Hence, calibration is possible.
- The pressure difference between its two faces dictates the deformation of a thin diaphragm.
- The reference face can be opened to the atmosphere to measure gauge pressure, opened to a second port to measure differential pressure, or sealed against a vacuum or other fixed reference pressure to measure absolute pressure. Mechanical, optical, or capacitive techniques are used to measure the deformation. Ceramic and metallic diaphragms are used.
- Range: (-) 10000 to (+) 10000 mm-WC
Advantages of Diaphragm pressure gauge
- Small size & moderate cost
- Linearity
- Adaptability to slurry services & absolute & differential pressure.
- High over-range characteristics
Disadvantages of Diaphragm pressure gauge
- Limited to low pressure
- Difficult to repair
- Less vibration & shock resistance
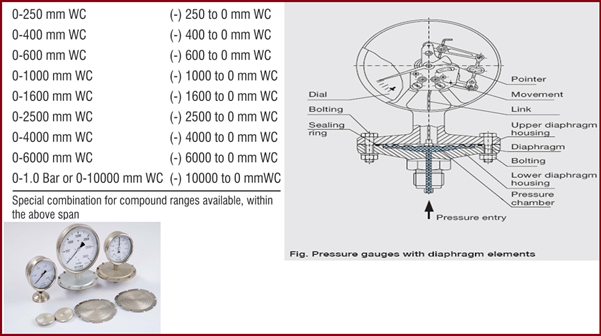
Capsule Pressure Gauge
Capsules as pressure measuring devices are used normally for low-pressure applications.
- A capsule is formed by joining the peripheries of two diaphragms through soldering or welding.
- Used in some absolute pressure gages.
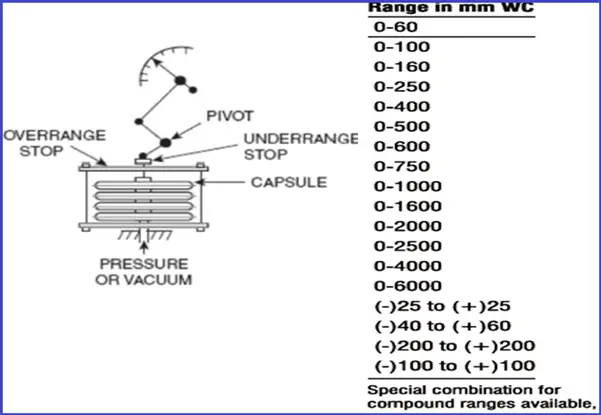
Range of Elastic-Element Pressure Gages
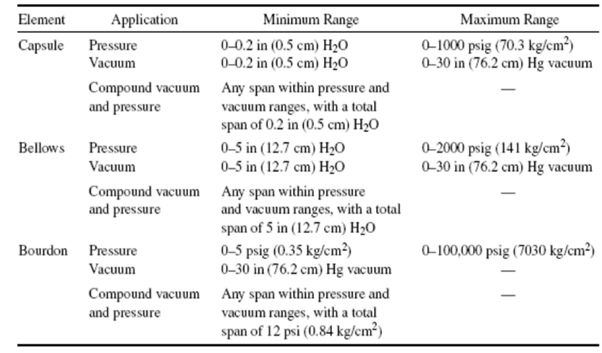
Pressure Measuring Accessories
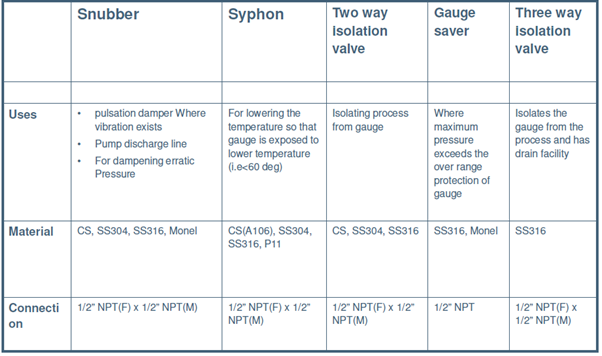
Diaphragm seals: These are designed to isolate the sensing element of pressure gauges from process fluids.
Gauge Saver: Gauge Savers also known as overpressure protectors are applicable where pressures exceed the maximum pressure rating of the pressure gauge.
Pulsation dampener: Dampeners considerably reduce the pulsations and make the gauge reading easier and also improve the life of the gauge.
Siphon: This connection between the pressure gauge & process in applications, where high temperatures like steam, vapors, or fluids are present. It acts as a cooling coil and protects the gauge from high temperatures and also helps in dissipating heat.
Precautions: When first installed the siphon should be filled with water or any other suitable separate liquid.
- U Type – For Horizontal pressure tapping
- Q Type – For vertical pressure tapping
Needle valve: The large round handle offers maximum ease and precise control to throttle the pressure to the gauge.
Block & Bleed Valve: Equipment Isolation with automatic pressure bleed for safety
Manifolds
- These are fluid distribution devices.
- These are used in conjunction with pressure gauges, differential pressure gauges & differential pressure transmitters.
- They combine instrument isolation & equalizing in one block.
- The manifolds are available in 2way, 3 way & 5-way types with remote & direct mounting styles
Gauge cack: It is used in conjunction with the siphon as an isolation valve. It is not recommended for pressure over 100 psi.
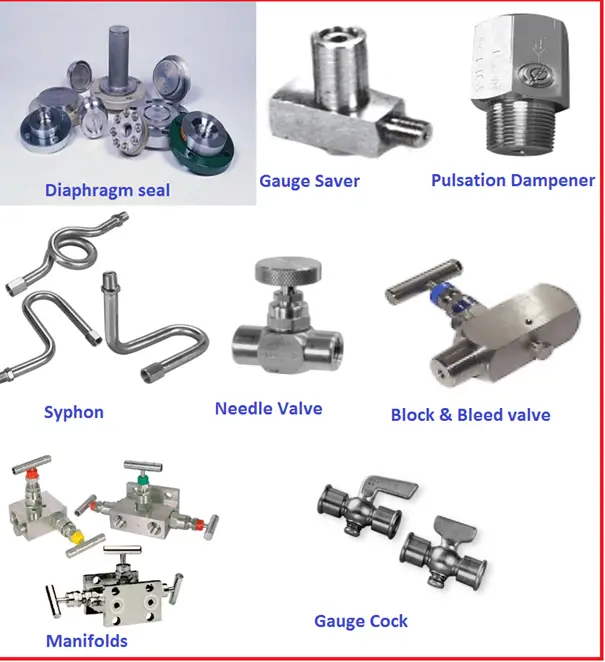
Selection of Pressure Gauges
To ensure accurate measurements and safe operation, the selection of a pressure gauge must be appropriate. However, selecting a pressure gauge is not straightforward as various designs of pressure gauges are available. The selection process depends on various parameters like:
- Specific Application for the pressure gauge.
- Type of Pressure Gauge
- Accuracy required
- Dial size
- Mounting Options
- Operating pressure ranges
- Pressure Connection
- Environmental Conditions
- Material Compatibility
Few more resources for you.
Understanding Pressure and Temperature in the context of Pressure Vessel Design
Pressure Tests of Piping systems-Hydrotest Vs Pneumatic Test
Temperature Measurement by Filled Thermal Systems
FUNDAMENTALS OF TEMPERATURE: An article
Few Points for High Temperature and High-Pressure Piping