Valve selection is the process of choosing the appropriate valve for a specific application based on various factors such as the type of fluid or gas being handled, the operating conditions, and the required performance characteristics.
Valves are mechanical devices used to regulate the flow of fluids or gases in a piping system, and proper valve selection is crucial to ensure the safe and efficient operation of the system. The selection of a valve should take into consideration several factors, including the flow rate, pressure, temperature, and chemical compatibility of the fluid or gas being handled, as well as the required level of control or regulation.
The type of valve selected can also affect the performance of the system, as different valves have different characteristics, such as flow capacity, pressure drop, and shut-off capability. Common valve types include ball valves, globe valves, gate valves, butterfly valves, and check valves, each with its unique features and benefits.
In addition to considering the fluid or gas properties and operating conditions, valve selection may also involve evaluating factors such as cost, reliability, ease of maintenance, and compatibility with other system components. Working with a qualified valve supplier or engineer can help ensure that the appropriate valve is selected for the specific application and that it meets all necessary safety and performance standards.
Valves are important mechanical (sometimes electro-mechanical) devices that help in controlling the fluid flow through pipes or tubes. Selecting the right kind of economic valve for a specified fluid service requires many considerations. This article provides guidelines for the selection of normal-type valves. (Special-type valves are not covered in this article).
It should be recognized that Valve Selection is a very extensive and complex subject and it is not possible to select only one type based on this article. The valve selected to work under the same conditions will differ from one client to another. It is necessary to compare the cost and come to an agreement with the client.
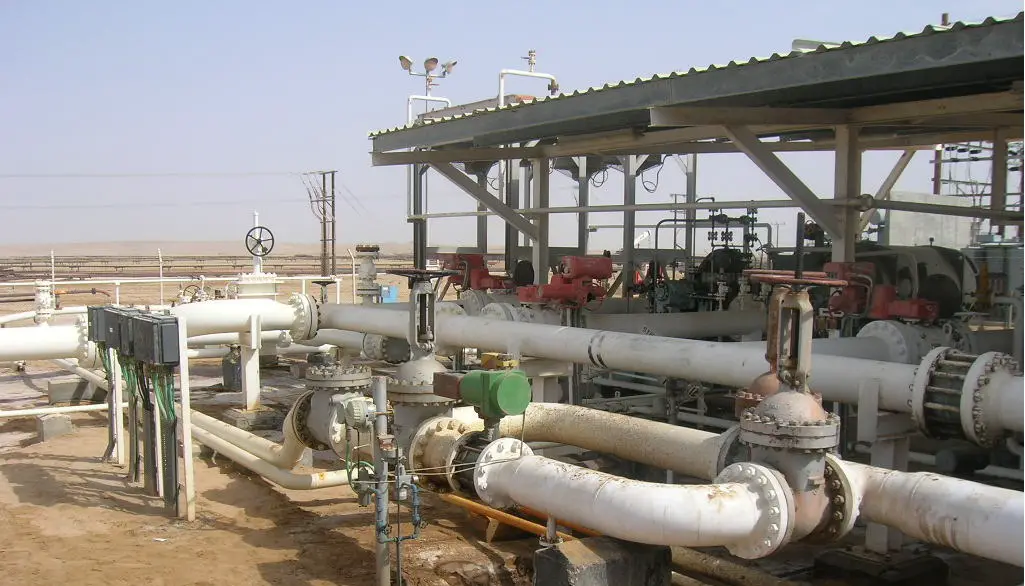
Criteria for Valve Selection
The selection of valve type requires an understanding of the following.
- Valve Function
- Service Characteristics
- Cost of Valve
Valve Selection Based on Valve Function
There are two basic principles by which valves are constructed.
(1) The first principle is developed in three ways:
- Moving the stopper by direct thrust onto the orifice seating. This obturating movement is the basis of globe valves.
- Rotating the stopper. This is the basis for plug valves or ball valves.
- Sliding the stopper across the face of the orifice seating. This is the basis of gate valves.
(2) The second principle, squeezing action, is the basis of all diaphragm valves.
These are shown in the following Figure (Fig. 2)
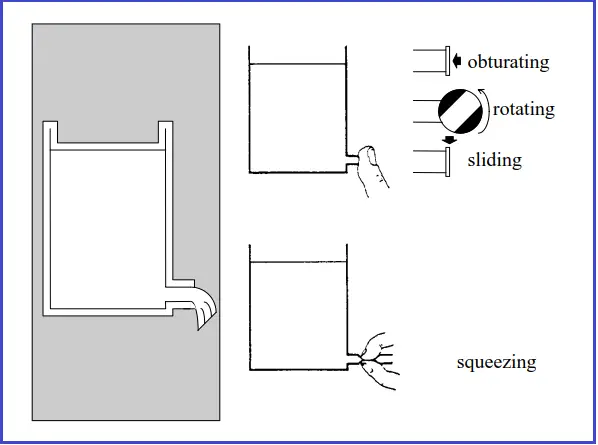
(3) Each of the four-valve motivations has its own advantages and disadvantages, as listed in the following table (Fig. 3).
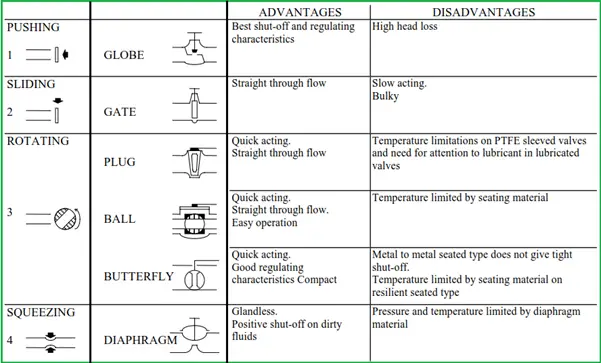
To summarize, there are four basic valve types, each type having its own individual characteristics and offering its own particular advantages or disadvantages.
For this reason, many modifications and variations of the basic type are made by valve manufacturers. An appraisal of the chief characteristics of the above four basic valve types is given in the following paragraphs
Globe Valve Selection Criteria
The globe valve is used for flow regulation or as a block valve where resistance to flow is not critical and positive closing action is required. They have a tortuous configuration which is typical of the closing method and results in higher resistance to flow compared with other valves.
Gate Valve Selection
Gate valves are used for on/off operation on hydrocarbon, general process, and utility services for all temperature ranges.
They have straight-through configurations which are typical of the sliding method, therefore, minimum resistance to flow.
The disadvantages are that they have the slowest action of all valves because the gate has to be moved a distance greater than the bore of the valve, which also means that the valve is of necessity bulky in height.
Selection of Plug valve
Plug valves have a quarter-turn operation, plugs are tapered or parallel plugs, and are suitable for most on-off clean processes and utility services, including non-abrasive slurries.
They have straight-through configurations typical of the sliding method.
The disadvantages of the basic plug cock are two-fold.
Firstly, its quick action can lead to a water hammer on hydraulic installation when it is closed too rapidly, and secondly, it is difficult to combine tight shut-off with ease of operation.
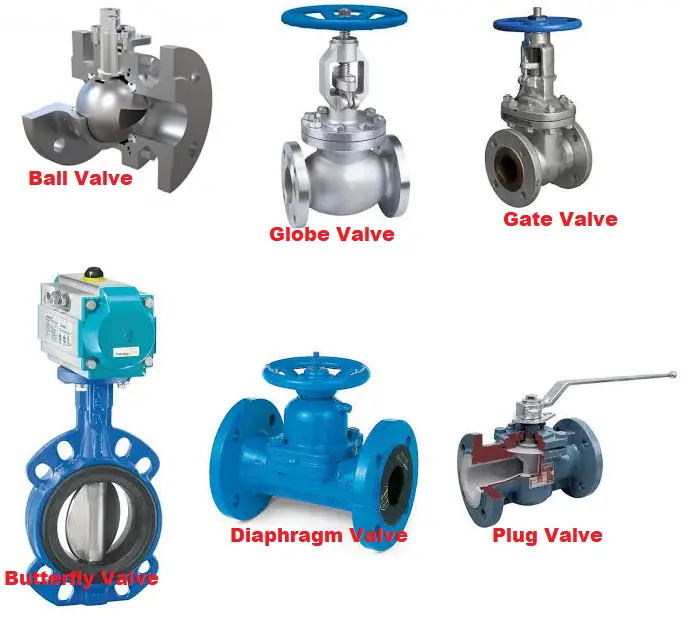
Ball Valve Selection Guidelines
A low torque quarter-turn valve, with a low resistance to flow, is suitable for many on-off utility and process services.
It has a straight-through configuration typical of the sliding method of closure.
Butterfly Valve Selection Procedure
A low torque, quarter-turn, rotary action valve with a straight-through flow configuration in which the disc is turned through 90 degrees, close to open position, in axial turning bearings and is used as a control or block valve. It is of compact design and may be obtained with or without flanges and linings. The seating arrangement may be soft (use of body lining, trapped ‘O’ ring, etc.) or metal to metal.
When to Select the Diaphragm Valve
Diaphragm valves have straight-through flow or weir configurations employing the flexing method and may be used for low-pressure chemical plant processes on-off or regulating the operation of most gases and liquids, e.g. slurries, viscous fluids, and fluids that are chemically aggressive.
The inherent disadvantage is that the diaphragm has to be made from an elastomeric material, usually either a natural or synthetic rubber, and this limits the application of the valve with respect to both temperature and pressure. Also, because of the stresses induced in the diaphragm, the valve has a shorter working life than other valve types.
Typical Valve Types
Typical valve types for various operating functions are given in the following table.
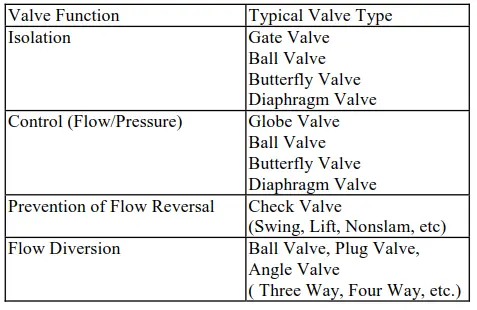
Valve Selection based on Service Characteristics
Valve selection is dependent on the characteristics of the services as follows.
- Fluid type
- Fluid characteristics
- Pressure and temperature limitations
- Operation and maintenance requirements
1. Fluid Type:
The fluid being handled should be classified as follows,
- Liquid (including Two-Phase)
- Gas
- Steam
- Slurry
- Solids
2. Fluid Characteristics:
The characteristics and condition of fluids and slurries require careful identification since these are often the most significant factors in selecting the correct type of valve.
Clean fluids generally permit a wide choice of valve types, for dirty fluids the choice is often restricted and may require a specific type of valve.
The fluid is divided into the following characteristics.
(1) Clean Service
(2) Dirty Service
- Dirty service involves fluids with suspended solids that may seriously impair the performance of the valve unless the correct type of design is selected. This type of service is often of major significance since many valves are very sensitive to the presence of solids. Dirty service is further classified as abrasive or sandy.
- Abrasive Service is a term used to identify the presence of abrasive particulate found in piping systems and includes the presence of pipe rust, scale, welding slag, sand and grit which are damaging to many valves. These materials can damage seating surfaces and clog working clearances in valves often resulting in excessive force required to operate valves, sticking, jamming, and leakage through the valves.
- Sandy service is a term identifying severe abrasive and erosive conditions and is used in oilfield production to identify the production of formation sand with reservoir crude oil or gas.
(3) Slurry Service
- Slurry service involves liquids with substantial solids in suspension.
- Slurries vary widely in nature and concentration of solids, and hard abrasive solids of high concentration can cause severe abrasion, erosion, and clogging of components.
- Soft, non-abrasive solids can cause clogging of components.
- In certain chemical processes, polymerization may block the cavities, preventing valve operation.
(4) Solids
- There are many other conditions where solids may be present in the form of hard granules, crystals, soft fibers, or powders.
- The transporting media may be liquid or gas. Air or fluidized bed systems may be used for some particulate. Specialized valves are available for many of these services but development work may sometimes be necessary.
(5) Hazardous & Flammable Service
- Hazardous and flammable material is normally specified in Fire Service Law and/or the Client’s specifications.
- Toxic substances such as chlorine, hydrofluoric acid, hydrogen sulfide, CO, phenol, etc.
- Highly corrosive fluids such as acids and caustic alkalis.
(6) Corrosive Service
- Corrosive service is a term generally used to identify clean or dirty fluids containing corrosive constituents that, depending on concentration, pressure, and temperature, may cause corrosion of metallic components. Corrosive fluids include sulfuric acid, acetic acid, hydrofluoric acid (HFA), wet acid gas (wet CO2), sour gas (wet H2S), and chlorides. Many chemicals are highly corrosive.
- The choice of suitable corrosion-resistant materials for valve pressure retaining components (boy bonnet) and trim is necessary to avoid corrosion that can impair the integrity or performance of the valve.
(7) Viscous Service
- Viscous service is a term that generally identifies a wide range of dirty or clean fluids with pronounced thickness and adhesive properties that, for the range of operating conditions(pressure, temperature, and flow) may require high operating torques and cause a sluggish response affecting seating. Fluids include high-viscosity oils (lube and heavy fuel oil) and non-newtonian fluids e.g. wax crude, gels, and pastes.
- The choice of valves for viscous service can vary depending on fluid properties. Special attention should be given to the check valves where a sluggish response may cause operating difficulties and even hazardous conditions.
(8) Fouling Service
- Fouling or scaling service involve liquids that form a deposit on surfaces. Such deposits may vary widely in nature, with varying hardness, the strength of adhesion, and rates of build-up. Valves for these services require careful selection, particularly where thick, hard, strongly adhesive coatings occur. The temperature of the fluid may be a vital factor and in some cases, valves may need tracing or be steam jacketed or of purged design.
(9) Solidifying Service
- Solidifying service is a general term used to identify fluids that will change from liquid to solid unless maintained at the correct conditions of temperature, pressure, and flow. It is a term generally associated with fluids such as liquid sulfur and phthalic anhydride where valves of steam-jacketed design may be required or heavy fuel oil where valves often require tracing to maintain temperature and operability.
3. Pressure and Temperature Limitation:
- Valves are normally allocated a rating according to the maximum operating pressure and temperature or the ratings of the piping system and flanges.
- The temperature also limits the materials used in the valve construction, particularly the internals, trims, seals, rings, or lubricants.
- These are normally defined in the “Piping Material Specification”.
4. Operation and Maintenance Requirements:
Operation and maintenance requirements can influence selection and design. Consideration should be given to:
- Fire Resistance: There may be a requirement for valves having non-metallic (soft) seating to include ‘fire-safe’ features so that in the event of the soft seat and/or seals being damaged or destroyed by fire the valve will still be operational and any leakage will be within the acceptable limits laid down by a particular standard or specification.
- Operability
- Leak tightness (internal and external)
- Maintainability
- Storage and commissioning
- Pipeline requirements (e.g. ability to pass cleaning pigs)
Valve Selection Considering the Cost of Valves
The costs of valve types cannot be simply compared because they vary depending on the countries where they are produced, vendors, and the balance of demand and supply.
In most cases, clients call for stress relieving, annealing, radiographic inspection, etc. of the valves, which affects the cost of the valves. Therefore, it is necessary to ask the Procurement Division to inquire about suitable vendors regarding these valves, based on the service conditions and the client’s requirements, after they are defined.
After a draft of the P&ID is issued, the personnel in charge of the preparation of the P&ID should cooperate closely with the piping design engineers in charge, during the in-house review period of the P&ID, and should determine the valve types and prepare piping material specifications in parallel.
- Generally, gate valves are less expensive than globe valves of the same specification. However, the cost of 1-1/2″ or smaller-dia. malleable gate valves are higher than that globe valves.
- Class 150 Gr.304SS TFE-seat 4” or smaller-dia. ball valves are less expensive than gate and globe valves.
- Class 150 cast iron/malleable iron TFE-seat 2″-4″ ball valves are less expensive than gate and globe valves whose rating and material are the same.
- In recent years, domestic vendors have developed and distributed light and inexpensive 2″ or smaller wafer-type ball valves, which should be positively adopted in chemical plants.
- The cost of soft-seat butterfly valves, applied in the range of approximately 10 kg/cm and 80°C or lower, is the lowest compared with other types of valves.
Metal-seat butterfly valves could be used in the same applicable range as general gate valves if the same material is used for the metal seat. Also, as Class 600 and 900 butterfly valves have been developed and distributed, they should be positively applied to process lines. If the butterfly valves are throttled in use, care should be taken to avoid cavitation.
Few more Valve Related useful Resources for you…
A brief article on Valve Inspection & Testing
Ball Valve Design Features: A Literature
Details about control valves
An article on ROTARY SELECTOR VALVE (RSV) and MULTI PHASE FLOW METER (MPFM)
A short presentation on Control Valve Sizing
Routing Of Flare And Relief Valve Piping: An article
Nonstandard Valve Model for Pipe Stress Analysis: Angular, 3-way, 4-way, with Actuator
Modeling Relief Valve (Pressure Safety Valve) Thrust force
Valves are one of the important mechanical (sometimes electro-mechanical) device that helps in controlling the fluid flow through pipes or tubes. Selecting the right kind of economic valve for a specified fluid service requires many considerations. This article provides guidelines for the selection of normal type valves.
Excellent
You are doing very well. Your reserchs are indepth and educating.
My comment on the pressure/temperature limits for the valves matchig the piping matrial class is that it is verry difficult to achieve this dueto the wode range of temperature specified for PMC. Eg -20C to 300C.
The seals in the trim like O-ring will be almost immppssible to get one suitable for such range. So the operating maximum/minmum temp. for the system can be used for the valves.
Thanks.
Hello. I have a question. What is Wake frequency calculation and how calculated this calculation?
Very Informative, especially for non-piping engineers.