Providing adequate clearances and access to process equipment, valves, and instruments are of utmost importance for the proper maintenance, operation, and safety of any plant. This present article can be used as a guideline for the preparation of plot plans and equipment layouts for various process plants, offsite, and utilities. This article covers general requirements for on-shore plant layout of process units, equipment, and general facilities, utility plant, and offsite areas. It gives basic considerations for plant clearances and access, equipment elevation, paving, grading, sewers, and other related items.
Plant Clearances and access for the operation and maintenance of proprietary equipment shall be in accordance with the manufacturer’s or equipment vendor’s drawings/operating guidelines or manual.
Considerations during Plant Layout Design
While designing the plant layout, the following guidelines need to be considered.
- Process units and other facilities shall be integrated within a common plant area only where independent operation and shutdown for planned maintenance of different facilities are not required.
- Where the process units and other facilities need to be separated from each other from an operations and maintenance point of view, they shall be located at sufficient distances apart from each other with separating spaces or roads. These shall be interconnected by pipe racks/pipe sleepers. It shall be noted that most of the time, these separating distances are governed by statutory / insurance rules.
- Layout and design shall be based on, and provide access for, maximum use of specific mobile equipment for normal planned maintenance work.
- Access ways for mobile handling equipment shall be normally 6m wide with 6m overhead clearance. Overhead clearances shall be finalized only after ascertaining the type of mobile equipment proposed to be used in the plant.
- Where inaccessible to mobile maintenance equipment, facilities such as davits and trolley beams shall be provided. Proper passages shall be planned for the movement of equipment to the workshop for carrying out repairs and for the provision of maintenance space.
- The plant layouts shall take into account the requirement of turning radii of mobile equipment and tanker lorries etc. Road-turning radii shall be suitable for the movement of proposed mobile equipment and tanker, lorries on the plant roads.
- It is essential that the layouts meet statutory and insurance requirements as well as other requirements noted therein.
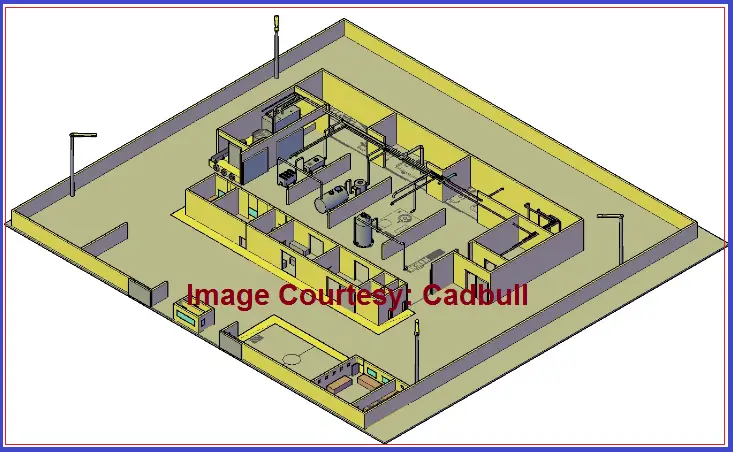
Plant Clearance and Access Consideration for proper Accessibility
Proper Access shall be provided to equipment, valves, and instruments requiring operational control or normal maintenance during plant operation, by operating passages or elevated walkways, platforms, and permanent ladders.
- Main operating or service levels are defined, as those areas during plant operation requiring plant personnel to be normally or intermittently present for substantial periods of time.
- Stairways shall be provided as a primary means of access to main operating or service levels in structures, buildings, or furnaces. Cage ladders are not acceptable as the primary means of access.
- Storage tanks shall also be provided with stairways where tank heights are more than approximately 6 m. It is preferred to provide independent staircases for lined storage tanks.
- Auxiliary service platforms are defined as those areas which, during plant operation do not require the presence of plant personnel except for short periods of time.
- Primary access to platforms attached to vessels, auxiliary service platforms in structures, furnaces, and storage tanks for platforms up to approximately 6 m (20 ft) high, shall be by vertical cage ladders.
- Auxiliary exists from platforms shall be by means of ladders. Such exists shall be required when platforms are longer than 7.5 m and shall be located so that no point on an operating platform is horizontally more than 22.5 m from a primary or auxiliary exit. The dead-end length of a platform shall not be greater than 7.5 m.
- The vertical rise of any stairway shall not exceed 4.5 m in a single flight at a maximum angle of 40° and shall provide a minimum clear headroom of 2.1 m.
- The vertical rise of ladders shall not exceed 5 m for a single run. Ladders that are located or extended more than 2.25 m above grade shall be provided with safety cages. Ladders that rise more than 5 m shall have an intermediate rest platform.
For equipment requiring operational control or normal maintenance during plant operation:-
Platforms or ladder access not less than those specified herein shall be furnished for equipment, located more than 3.6 m above grade and 2.1 m above another platform and include the following means of access:
- Where regular access is required, a minimum clear aisle width of 0.75 m and overhead clearance of 2.3 m shall be provided.
- Groups of valves at battery limits in elevated pipe racks and grade pipe sleepers shall be provided with permanent platform access. The type of valves (gate, plug, ball, etc.) shall be taken into account when locating such platforms.
Exceptions: Flanged nozzles on vessels, block valves in pipe racks (not requiring operation except for infrequent isolation) metal temperature measuring points in piping, and orifice flanges in lower pipe racks shall NOT be provided with permanent means of access.
Elevated platforms shall have sufficient space as defined herein for maintaining equipment; tall columns shall be provided with davits for removing covers, relief valves, blinds, etc. and the same shall be located such that these can be lowered safely to ground level.
Plant Layout Design Rules for Manual operation of valves
Valves requiring operation during plant operation or in an emergency shall be located as follows, otherwise, such valves shall be equipped with chain operators or extension stems:
- Horizontally installed valves 6″ (150 mm) and smaller – the bottom of the handwheel shall not be higher than 2.25 m or the maximum height to the centerline of the handwheel shall be 2.3 m above grade or platform, whichever governs.
- Horizontally installed valves 8″ (200 mm) and larger – maximum height to the centerline of the handwheel shall be 1.95m.
- The preferred height to the centerline of all valves shall be 1.5 m above grade or platform.
- Horizontally installed wrench-operated plug, ball, or butterfly valves shall be positioned so that the wrench movement arc is no higher than 2.3 m above the grade or platform.
Equipment Clearance and Access Guidelines
Layout and Safety Design Rules for Furnaces and Fired Heaters
- Several furnaces in the same or different services and part of the same process unit or facility, together with associated close-coupled equipment, may be located in a single area and shall be segregated within that area only as required for operational and maintenance requirements.
- To avoid a hazard, a furnace and close coupled equipment or a furnace area shall be located not less than 15m and preferably upwind (prevailing) from other equipment containing flammable fluids, except as follows :
- The distance shall be measured from the outside of the nearest of furnace walls to the nearest point of the equipment considered.
- Not less than 15 m from air coolers, containing flammable fluids.
- Gas or liquid reforming furnaces, as used in ammonia and similar plants, may be located at a minimum distance from associated process equipment consistent with operating design and maintenance requirements.
- Reforming and desulphurizing furnaces may be located at a minimum distance from their reactors and feed/effluent exchangers, consistent with operating and maintenance requirements.
- Not less than 15m from switch rooms, un-pressurized control houses, and the compressor or pump house containing equipment in hydrocarbon service. These distance requirements shall generally be governed by statutory / TAC regulations.
- Furnaces shall be located at a maximum practical distance from process equipment containing liquefied petroleum gas or similar materials in accordance with applicable Tariff Advisory Committee (TAC) rules with a minimum distance of 15 m.
- Integral-type fired heaters such as start-up heaters shall be considered exceptions.
- Fired furnaces of the following types that are used only for planned intermittent and start-up service may be located at a minimum practical distance from the equipment which they serve and not less than 6 m from other equipment, including air coolers containing flammable fluids.
- Furnaces having welded coils and no header boxes.
- Furnaces with header boxes facing away from other equipment.
- Vertical cylindrical furnaces.
- Areas for tube pulling shall be as shown on the plot plan and may extend over roads that are peripheral to the unit and not required for access to other plot areas.
- Furnaces shall be provided with platforms for operation and access as follows:-
- Platforms for maintenance of soot blowers and dampers.
- Platforms for burner operation when inaccessible from grade or in accordance with client requirements.
- Platforms for access / observation doors except that when the doors are located less than 3.6 m above grade or another platform, access shall be by ladder only.
- Platforms for header boxes containing removable plug fittings.
- Platforms for decoking / swing elbow connections.
Plant Clearance and Access Considerations for Heat Exchangers, Air Coolers & Cooling Towers
Shell and tube heat exchangers at grade shall generally not be stacked more than two units high, with a maximum bundle weight of ten tonnes.
Permanent steel or reinforced concrete structures with monorail beams shall be provided for supporting bundles during pulling and lowering to grade if any of the following conditions apply :
- When specified available mobile equipment is not suitable.
- Shells stacked more than two units high.
For Shell centreline, more than 3.6 m above grade and Bundle weight exceeds ten tonnes
- Platforms shall only be supplied where required for operation.
- Although platforms shall not be provided for access to exchanger’s heads, the layout shall be arranged to facilitate maintenance.
- Bundle removal of elevated air coolers may be over adjacent equipment where suitable cranes are available, otherwise, crane accessways shall be provided for removing bundles.
- Access shall be provided for the maintenance of fan drives and headers as appropriate.
- Proprietary plate type, double pipe, or multiple heat exchangers installed at grade will not be provided with handling or tube pulling facilities.
Air-cooled exchangers may be located at a grade above other equipment or structures, or above overhead pipe racks, subject to the effects of other equipment or structures on air cooler performance and as stated in the below paragraph
Air-cooled exchangers containing flammable fluids shall NOT be installed directly above control rooms, MCC rooms, transformers, and other major switchgear.
Water sprays shall be provided over equipment in the following services located directly beneath air-cooled air exchangers containing flammable fluids.
- Pumps handling flammable fluids with an operating temperature above the auto-ignition temperature or 260°C (560°F) whichever is less or,
- Pumps handling light hydrocarbons with a vapor pressure greater than 3.5 kg/cm² at 38°C (100°F) or with a discharge pressure in excess of 35 kg/cm² or
- Compressors in flammable vapor service.
Equipment adjacent to cooling towers should be located at a sufficient distance downwind as determined by each season’s prevailing winds from cooling towers, to minimize detrimental effects during fog-creating seasons.
The location of cooling towers with respect to roads should be considered carefully as the fog created under certain conditions of temperature and humidity presents a serious driving hazard. If necessary, roads should be provided on both sides of critically located cooling towers; public highways should be located at min. 45 m from cooling towers.
Reactors, Towers, and Vessels: Monorail beams shall be provided for charging reactors only when the use of a crane is not feasible.
Design Rules for Structure Clearance and Access
- Ladders shall generally be arranged for the side exit. Step-through ladders may be used for runs from grade up to a height of approximately 6 m or for elevated runs of approximately 3 m.
- Where ladders are not provided for access between platforms, intermediate steps shall be provided where the difference in elevation is more than 0.35 m.
- Handrailing shall enclose all stairways and platform areas where the clearance between the equipment and the edges of flooring is greater than 0.3 m. Toe plates only shall be provided around floor openings for permanent equipment where the clearance to the edge of the flooring is greater than 50 mm but less than 0.3 m. Handrails shall be provided at the periphery of tank roofs adjacent to access stairways and dip hatches.
- Sheds for pumps, compressors, and other equipment, if provided, shall be as follows.
- Where compressor sheds (or utility sheds) are provided they shall be open-sided steel frame structures, sheeted from roof eaves level down to a maximum height of 2.45 m above the compressor house floor level, with ventilation by means of natural draught.
- Where pump or equipment sheds are provided they shall be steel framed with sheeting as described in (a) above.
Compressor houses shall be provided with suitable facilities for handling the heaviest machine component during normal maintenance including the following (but excluding motor drivers):-
- A laydown area and suitable road access for this area shall be provided adjacent to the compressor house.
- The compressor house ground floor shall be designed to carry the internal parts of the machines, but not the top halves of casings, during maintenance.
The design of structures containing equipment shall not provide for the removal of equipment, not considered a normal maintenance requirement, except as follows :
- To provide access to mobile equipment.
- To provide clearance within the structure
- To provide for the removal of sections of the structure where specified.
- Facilities for breakdown maintenance of vital equipment, the failure of which would seriously affect plant certification and/or production, e.g. Standby Generators / Power units.
Layout rules for Pumps and Compressors
Where permitted by the equipment design, the provision shall be made to allow the removal of the pump internals or driver without dismantling the piping or removing the isolation valves. For this purpose, a flanged spool piece or strainer on the pump nozzle shall be considered satisfactory.
- Pump isolation valves shall be located in the pump area as close as feasible to the pump and operable from grade. Valve hand wheels shall be oriented to leave clearance over a pump for maintenance and to permit operation without leaning over the pump.
- Pump / Compressor isolation valves shall be located near the equipment in such a fashion that no excessive loads are transferred to the Pump / Compressor nozzles.
In general, the drive ends of groups of similar pumps in process and utility plant areas shall line up. In offsite areas, the pump ends of the plinths of groups of pumps shall line up. Large pumps may be orientated parallel to a pipe rack or passage.
The alignment bellows for pumps shall not be mounted directly on pump nozzles. A flanged spool piece of sufficient length shall be installed and anchored between pump nozzles and the bellows.
Clearance and Spacing Rules for Buildings
Where practicable, central control rooms, MCC rooms, and substations shall serve several process units, utility plant, and offsite facility areas. Suitable isolation of utility supply shall be provided where required.
However, where impracticable, or as per the client’s operating philosophy, separate control/MCC rooms may be provided for utility and offsite areas.
Control rooms and switch rooms shall be located as follows:-
- In an area which shall be at a safe distance from the nearest normal source of flammable hazard (Safe distance as per statutory or TAC rules) or,
- When not located in a safe area shall be of pressurized design with the top of the air intake stack located in a safe area. In such cases, the construction may have to be blast-proof.
Design rules for Piping
- In general, process lines, utility headers, and instrument and electrical cables in process and utility plant areas shall be routed on overhead pipe racks at established elevations and in offsite areas on pipe sleepers at grade level.
- In general, lines to equipment in process and utility plant areas will be run overhead of maintenance and operating passages. However, short runs of pump suction and similar lines may be run at grade level where they do not obstruct maintenance access. Where the crossing of general walkways is unavoidable, walkover platforms shall be provided.
- Offsite pipe racks/sleepers shall normally be located adjacent to storage tank dykes and roads.
- Within dyked areas, lines shall be run by the most direct route, as limited by flexibility and tank settlement. Lines at grade serving tanks in a dyked area shall not pass through adjoining dyked areas.
Insulated lines passing through dykes shall be enclosed in sealed sleeves, and uninsulated lines shall be coated and wrapped. Insulated lines under road crossings, and all pressure lines beneath railroad crossings, shall be enclosed in sleeves unless they are run in culverts.
When located below grade, piping provided with protective heating and piping and services requiring inspection and servicing shall be in built-up trenches.
Cooling, potable, fire service, and similar water piping, shall generally be buried with the centerline of the pipe below the frost line, or be provided with means to prevent freezing.
Buried piping shall be provided with a protective covering of at least 0.3 m. In cases where heavy load traffic is expected, the minimum coverage may be 1.0 m with/without higher than the normal thickness of piping.
- At all changes in direction piping requiring frequent (at least once a week) cleaning shall be provided with flanged fittings or with five diameters (minimum) bends. The run of pipe between flanged cleanout points shall be limited to 12 m for cleaning from one end, and 24 m for cleaning from both ends.
- Lines that require occasional cleaning shall be provided with sufficient breakout flanges for dismantling.
- Piping from pressure-relieving devices such as safety valves that discharge to a closed system shall generally be arranged to drain to headers without pocketing of lines and accumulation of condensates at the safety valves.
- The flare headers outside process unit areas shall be elevated and self-draining to the flare knockout drum. Flare auxiliaries, such as the ignitor station and steam injection control valve, shall be located near the drum. The line between the flare and the drum shall drain to the drum.
- Where practicable piping shall be designed to accommodate expansion without using such devices, such as expansion bellows, cold springing, etc. Line spacing may be based on anticipated line movements under normal operating conditions, if practicable.
Rules regarding Height for Atmospheric Discharge
- The top of stacks and continuously operating vents discharging hazardous vapors shall be at least 3 m above any platform or flat building roof, within a horizontal radius of 21 m from the stack or vent. This vertical clearance may be reduced by the same distance that a platform or building roof exceeds 21 m. However, the height shall be governed by State Pollution Control Board regulations and the HAZOP/hazard studies.
- The top of the outlet piping from relief valves and intermittent vents discharging hazardous vapors to the atmosphere shall be at least 3 m above any platform of a flat building roof within a radius of 15 m. This vertical clearance may be reduced by the same distance that a platform or roof exceeds is 15 m from the outlet piping.
- The discharge of steam, air, or similar non-flammable vapors from relief valves and continuously operating vents, shall be located to prevent any hazard to personnel.
- Minor vents, controlled by an operator, may discharge to the atmosphere local to the equipment vented subject to restrictions as noted above.
Guidelines for Flares
The location of flares shall be determined in accordance with client requirements, and vendor recommendations and in reference to the limitations of the ‘Guide for Pressure Relief and Depressurising Systems’ – API – RP.521.
- It is desirable that the flare shall be positioned upwind of process units and tankages, to reduce risks of ignition of possible vapor leaks.
- The safety zone around the flare stack shall be decided based on an acceptable radiation level at grade. This zone shall be isolated by means of a fence.
Design Rules for Maintenance and Equipment Handling
- Handling facilities shall be limited to the handling of working parts of equipment that require frequent or routine service and which are inaccessible to the handling facilities assumed to be available at the plant. Such facilities shall not be designed to handle heavy parts which normally are unaffected, such as the bedplates of rotating machines, rotating equipment, the bodies of compressors, machinery, frames, etc.
- Special consideration must be made where major machines are involved (e.g. multi-case compressor trains) where heavy lifts are likely and laydown areas are required. Clear passages to workers are also required in such cases.
- The design and installation of monorail beams, overhead traveling cranes, and hoist trestles shall be based on lifting the parts to be handled and transporting them or lowering them to specified maintenance areas or to grade. From these points, they are expected to be removed by skids or hand trucks to other areas which are more suitable for maintenance.
Requirements for Paving, Surfacing, and Grading
Paving shall be provided as shown on the plot plan. Walkways to buildings only and the following areas shall be paved subject to client’s discussions, on a contract-to-contract basis.
- The areas below bottom oil-fired or combustible liquid-containing furnaces and under elevated structures support coke drums or catalyst-containing vessels.
- The areas around groups of two or more pumps are located outdoors, extending approximately 1.2 m beyond the pump foundations with bunds on all sides.
- The areas around process equipment :
- Drainage facilities shall be provided to recover spilled materials or drain to the chemical/effluent system.
- The areas around rail and road loading installations, additive and metering facilities, extending approximately 1.2 m around the facility with bund on all sides.
- Areas below pressurized spheres and bullets.
- Curbs, when required to retain spilled materials, shall normally extend from the bottom of the paving to a height sufficient to contain the full contents of the largest atmospheric tank in the area. Concrete surfaces normally exposed to acids or similar corrosive materials shall be provided with protective coatings such as acid/alkali-resistant tiling.
- All paving shall be sloped towards drainage points, the minimum slope shall be 1 in 125 and the maximum fall shall be 150 mm, except for floors of control rooms, operator houses, and MCC room which shall be laid level. High points of paving shall generally be coincident with the finished floor elevation applicable to the area under consideration.
- The type and surfacing of roads and access ways for maintenance vehicles access shall be as shown on the plot plan.
- Unpaved areas within the battery limits of utility plant and process unit areas, administration and parking areas, shall be graded and surfaced with a minimum of 50 mm of gravel, crushed stone, or other suitable material.
- Offsite areas such as tank farms inside bund walls, pipe racks, and areas alongside roads, will not normally be surfaced except where required for maintenance or as specified in statutory regulations.
- Finished grade elevation of different plant areas or within the battery limits of an area, may be varied and established to permit adequate drainage.
- Roads shall be ramped over piping at the intersection with grade-level pipe sleepers, if possible. If not, suitable culverts shall be provided for the passage of pipes.
Design Considerations for Pipe Trenches and Pits
- In general, pipe trenches shall have concrete or brick side walls, open tops covered with grating or plate, and bottoms surfaced with crushed stone.
- Paving with acid-resistant titles shall be furnished in acid or similar corrosive services, and shall be sloped for drainage, with a drainage sump at the lowest point.
- The following items shall be considered :
- Firestops shall be provided where trenches cross-unit battery limits, or to maintain separate areas, such as totally enclosed buildings, furnaces, or grouped equipment.
- Pipe trenches located near fired heaters or any sources of ignition shall be backfilled with sand and be provided with sealed covers.
- The minimum width of pipe trenches shall be 450 mm. A minimum clearance of 100 mm shall be provided between the outside of the pipe, flange or insulation, and walls, and 50 mm to the high point trenches bottoms.
- Pipe trenches in paved areas shall be covered with plate or grating set flush with the top of the paving, and in unpaved areas shall be covered with a steel plate set 50 mm above the high point of adjacent grade. Trenches inside buildings shall be covered with MS / CI grating set flush with the floor. Trenches subject to vehicle traffic shall be provided with removable reinforced concrete covers set flush with the surface.
- Where provided, pits shall have concrete/brick walls. Floor surfacing of pits shall be concrete. Pits shall have a sump for the collection of drainage. The pit floor shall slope towards the sump.
- Access to pits shall be by ladders or ladder rungs cast into the walls. Stairways shall be provided for pits containing equipment such as vessels, pumps, and exchangers. Auxiliary exit ladders shall be provided if any point on the pit floor is more than 7.5 m from a main or auxiliary exit.
- Open pits shall be provided with handrailing and 150 mm high curbs above the grade level.
- Closed pits shall be provided with suitable removable covers set flush with paving in paved areas or 50 mm above grade in unpaved areas. Sealed covers, with a vent, piped to a safe location shall be provided for pits located near fired furnaces or similar sources of ignition.
Few more resources for you…
Piping Design and Layout
Piping Stress Analysis
Piping Materials
Piping Interface
Further Studies
- https://pipingdesigners.com/contents/tips-tools-training/section-8-equipment-piping/11-section-8a-general-guidelines-for-equipment-and-piping-location-spacing-distances-and-clearances
- https://books.google.com.om/books?id=jC6dDwAAQBAJ&pg=PA416&lpg=PA416&dq=A+Guide+to+Plant+Clearances+and+Access&source=bl&ots=YptxZxu6no&sig=ACfU3U2x0OlXqitmkpD8YN7bK0ufJd8BkQ&hl=en&sa=X&ved=2ahUKEwjAt5nmr5LnAhUSyYUKHU7wBicQ6AEwDXoECAoQAQ#v=onepage&q=A%20Guide%20to%20Plant%20Clearances%20and%20Access&f=false