As the name implies, plastic pipes are made of plastic materials. Due to its many advantages, plastic pipes are the ideal choice in many piping and plumbing solutions. In fighting corrosion, plastic pipes are an important alternative.
Corrosion (deterioration of materials under the influence of an environment) is a big problem in all operating Process Plants. Many of the failures reported in Plants are because of Corrosion. Hence given a choice one would be tempted to dispense away with Steel altogether as a material of construction for piping used. Unfortunately, it is not practical to undermine the usefulness of Steel in sustaining the Pressure and Temperature conditions normally foreseen in any Process Plant. That brings the concept of composite piping constructed from highly Chemical Resistant Polymer Compounds as the base material, reinforced with suitable fibrous materials such as Glass which provides it the requisite strength.
Advantages of Plastic Pipes
Plastic piping offers various advantages as listed below:
- Economic.
- Easy Installation.
- an ideal choice for low-temperature services.
- Lightweight, and easy to handle.
- Low Support load.
- Rust and corrosion-resistant.
- Smooth surface so less frictional loss.
- Chemical resistant.
Applications of Plastic Pipes
Due to its inherent benefits, Plastic pipes are widely used in the water and food industry for transferring drinking water, wastewater, irrigation, chilled water systems, chemicals, heating fluid, cooling fluids, foodstuffs, etc.
Types of Plastic Piping
Depending on plastic piping materials, basically, 3 types of Synthetic Polymer Components have found acceptance in industrial use.
- Thermoplastic piping
- Thermosets and
- Composite Plastic piping
Thermoplastic Piping Materials
The Thermoplastics are Polymer Compounds, which are normally available in crystal form. On the application of heat and pressure, these crystals attain the requisite level of flowability to be able to attain the desired shape by a molding process. On re-heating, the plastic material can once again undergo the transformation from solid to a flowable state which allows their reprocessing into the desired shape.
Some of the commonly used Thermoplastic materials are as follows:
- Polyethylene or PE
- Polypropylene or PP
- Polystyrene
- Polyvinyl Chloride or PVC
- Fluoro-Plastics
By and large, thermoplastics are structurally weak materials and have limited temperature endurance.
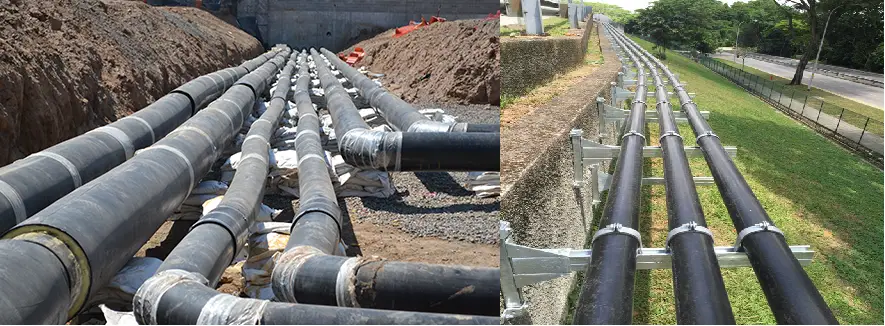
Thermoset Piping Materials
Thermosetting Plastics are Polymer compounds (resins), which are normally available in liquid form at ambient temperature. With the addition of a Catalyst and an Accelerator, these Resins undergo a chemical transformation into a rigid product that sets into the required shape by the curing process.
Some of the commonly used Thermosetting Plastics are as follows:
- Epoxies
- Furans
- Phenolic
- Polyesters – Bisphenol, Isophthalic, Halogenated
- Polyurethane
- Vinyl esters
Even though Thermosetting Plastics are relatively superior to Thermoplastics in terms of structural strength and temperature endurance, still in their virgin form they find limited use in industrial applications.
Composite Plastic Piping Materials
It is evident from the foregoing discussion that both Thermoplastics and Thermosetting Plastics in their virgin form lack the ability to sustain the level of mechanical loading normally encountered in Industrial applications. An attempt to strike an appropriate balance between the two desired properties of the material (i.e. Mechanical Strength and Corrosion Resistance) therefore has always remained a desirable objective. This brought forward the concept of Composite Plastics wherein a reasonable degree of mechanical strength is imparted to the base Polymer which in itself is adequately resistant to Chemical Corrosion, by way of reinforcing it with a suitable reinforcing material.
Most of the commercially available composite materials in the Reinforced Plastic category use a combination of Thermosetting Plastic Resins (e.g. Polyester, Epoxy, Vinyl Ester, etc.) and Fiberglass or Synthetic Fibres as reinforcing material. In order to provide ultra-superior chemical resistance, it is also possible to manufacture a composite material using Thermoplastic Material (e.g. PVC, PVDF, PP, etc.) as a baseliner over which the layers of Thermosetting Resins and Fiberglass are applied to attain the required mechanical strength.
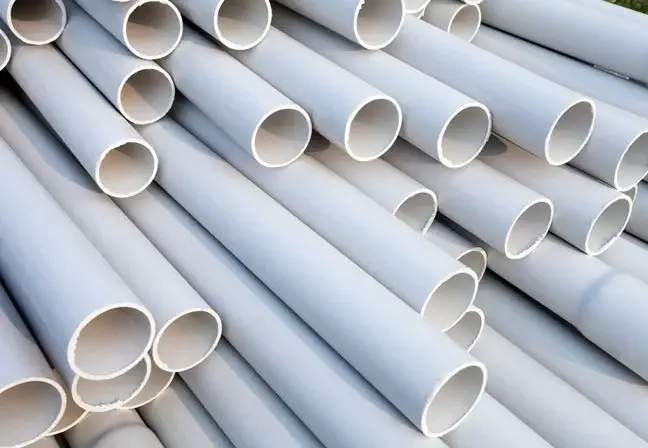
Composite plastic Piping Manufacturing Process
Composite plastics pipes are commonly produced by one of the following methods:
Custom Contact molding
It is a manual/ semi-automated process in which the composite sections are manufactured by application of various layers of resin and Glass Fibers (in various forms such as surface mat, roving mat, chop-strand mat, etc.) either by Hand Lay-up or by Spray Lay-up method.
Filament Winding
It is a fully automatic process in which automatic control over winding angle ( 0 to 90 degrees) and winding pressure can be exercised to obtain the varying degree of Hoop – Axial ratio and Glass – Resin percentage composition. Normally a winding angle of 54 3/ 4 Degrees provides a 2:1 Hoop–Axial ratio which is a condition of optimum internal pressure requirement. By increasing the winding pressure the Glass – Resin proportion could be varied from 80 % – 20 % to 60% – 40 %. A composite section of high Glass content will result in high strength and low chemical resistance and vice versa.
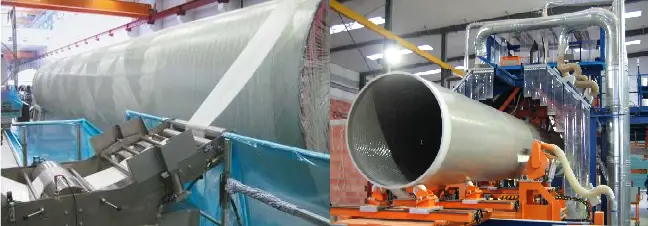
Pultrusion
As the name implies this is a sort of extrusion process by pulling the filaments through a resin bathtub and subsequently passing it through an extruding die and then through an atmosphere of controlled elevated temperature. The above process is commonly used for manufacturing rolled sections such as Angles, Channels, I Beams, etc.
Resin Transfer Molding
The above process is used for specialized applications for the manufacture of sandwich structures with certain core materials.
Plastic Piping System Design Considerations
The Plastic Piping System consists of Piping Profile fabricated from plain end pipe, plain and flanged end Fittings (i.e. Elbows and Reducers), and stub-in branch connections. The Flanged Joints are Stub Ends with loose Backing Flanges. In the case of Flanged Tapping Long Stub Flanges are recommended to be used in place of pipe stub-in and Short Stub Flanges. The pipe-to-pipe and pipe-to-fittings joints are laminated joints. Accessories for Piping System include Soft Rubber/ CAF Gaskets and Full Threaded Fasteners with Washers. The major considerations for the plastic piping system are listed below:
1. Owing to weak mechanical properties a minimum of NS 2” line size is recommended for Plastic Piping. However, tapping of small size (i.e. smaller than NS 2”) is permitted for drain/ vent, etc. provided the branch connection is adequately supported.
2. Owing to its large Coefficient of Thermal Expansion Plastic Pipelines exhibit a high tendency to grow under moderate temperatures. This may result in a sizable deflection of the branches and the corners of the Piping Profile. It shall, therefore, be ensured that the branch connections are not overstressed, either by providing adequate flexibility on the branch piping or by fixing the branch points by external means to disallow its deflection.
3. If free movement of the corners of the piping profile can be allowed (i.e. e.g. not being hindered by any other external item) then it is preferable to leave the profile to grow freely. However, if the growth of the profile has any adverse effect on the system stability (e.g. supports falling off from the external structure) it may be appropriate to restrict the growth of the sides of the profile by providing fixed supports at various locations as per Plastic Piping Support recommendations.
4. Unlike Steel, bellows are not used on Plastic Piping. The thermal stress behavior is addressed either by providing in-built flexibility in the system or by arresting the axial growth of the pipe runs within the pipe length itself. In case the later method is employed, the pipe may have to be guided at close intervals to avoid failure due to buckling.
5. Owing to its weak nature, the plastic piping shall not be supported by line contact between the pipe surface and the external structure taking the load. Hence as a general rule Clamp and Shoe type supports shall be employed on Plastic Piping System.
6. All concentrated loads (e.g. On-line Valves, Instruments, etc.) shall be directly supported to ensure that the load is transferred to the grade/ external structure without stressing the piping.
7. All the valves employed on Plastic Piping shall be provided a Fixed Type Support to ensure that the Piping is not overstressed in case of jamming of the Valve handwheel while operating.
8. Due to the excess thickness of the Plastic Pipe (as compared to Steel) it is likely to obstruct the opening of the flap of the Sandwich type Butterfly/ Wafer Check Valve into the pipe. In order to address the above issue, the Spacer Rings (made of the same or equivalent material as a pipe) will be employed across the valve. The above Spacer Ring is procured as a Special Part.
9. The Plastic Piping System shall be installed with permanent supports in place. The erection of Plastic Piping with temporary supports is not acceptable.
10. The pipes shall not be stretched in order to match the terminal ends
11. The Flange Joints shall be tightened to the specified Torque Value only by employing Torque Wrench.
12. As far as possible the Piping profile shall be prefabricated in the Vendors shop at the site, leaving only a few field joints for final fit-up.
13. In the case of FRP Piping with Thermoplastic Liner, the Field Weld will always be located at the convenient height/ location to allow down-hand welding/ jointing.
Few more related articles for you.
A short article on GRP Pipe for beginners
Basic Principles for an aboveground GRP piping system
Stress Analysis of Plastic Piping System
An Article on HYDROSTATIC FIELD TEST of GRP / GRE lines
Stress Analysis of GRP / GRE / FRP piping system using Caesar II
Stress Analysis of GRP / GRE / FRP Piping using START-PROF
Buried GRP/FRP pipe Laying and Installation Procedure
I found it interesting when you talked about plastic piping and how they come with anti-corrosion perks.