Storage tanks are the containers/vessels which are used for storing the fluid. A group of tanks together is called ’Tank Farms’. The preferred design standard for Atmospheric storage tanks is API 650. The use of tanks is common in all kinds of plants. However, Petroleum and Water industries are the largest users of tanks.
Storage tanks are manufactured in different shapes, sizes, and capacities. Cylindrical tanks are the most common ones. Spherical tanks are used for storing LPG. Proper arrangement of tanks and pipes is required to optimize space and cost. Broadly, Storage tanks are used to
- store feed products prior to processing.
- hold partially processed products before further processing.
- collect and hold finished products prior to delivery to market.
A) Process Plant
- Refineries
- Petrochemicals
- Specialty chemicals
B) Terminals
Types of Tanks in Process plant
Based on the type of products to be stored, shapes, sizes, and potential to fire storage tanks can be grouped into various types like
- Cone roof tanks: Low-pressure tanks for storing petroleum, water, food products, chemicals, and petrochemical products.
- Floating roof tanks: The roof floats depending on the volume of stored products. Mostly used in oil refineries, such types of tanks reduce fire hazards.
- Low-temperature storage tanks: Usually store cryogenic fluids line liquefied ammonia, propane, methane, etc.
- Horizontal pressure tanks or Bullet tanks: Elliptical or hemispherical high-pressure tanks.
- Hortonsphere pressure tanks: Store large quantities of fluids under pressure.
- Underground Tanks for drain collection of the plant at atmospheric pressure.
- FRP Tanks for corrosive fluids at atmospheric pressure.
Click here to know more about atmospheric storage tanks
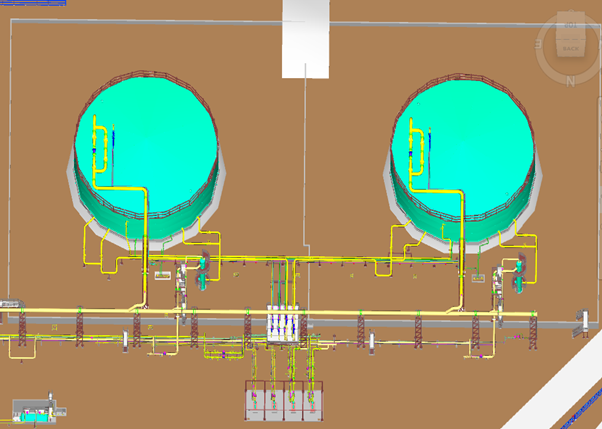
The design of the tank farm and tank farm piping layout should take into consideration the following guidelines
- Local rules and regulations.
- Client specifications.
- Maintenance and operation requirements.
- OISD 118, 117, 117
- NFPA 30
- API 2030, etc.
Tank Farm Layout Consideration
The main considerations for tank farm layout are
- The storage tanks shall be located at a lower elevation, wherever possible.
- The storage tanks should be located downwind of process units.
- All process units and diked (diked) enclosures of storage tanks shall be planned in separate blocks with roads all around for access and safety.
- Provide a minimum of two-way access to enter the storage tank area. Preferably roads shall be provided all around the dike. Also, vehicular access is to be provided inside the dike for maintenance purposes.
- Due to the risk of failure of storage tanks, an Earthen / RCC Wall(Dike) must be provided around the tank in order to hold the liquid.
- A staircase shall be provided to enter in storage tank area from the outside dike.
- The tank farm should be secured by fencing & access gates shall be provided.
Relative location for Area Layout
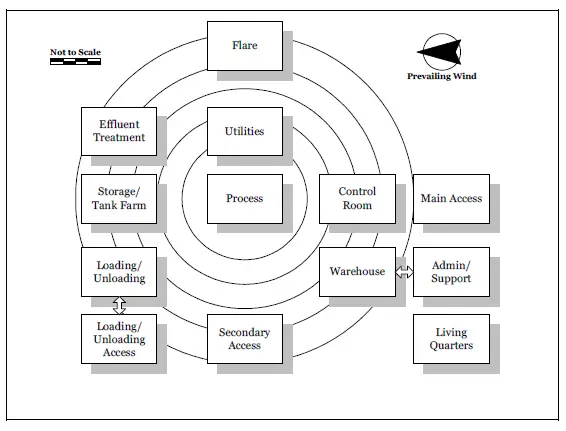
Tank Farm Layout (Dike Enclosures)
- Tanks shall be arranged in a maximum of two rows. Tanks having 47,700 cu.m capacity and above shall be laid in a single row.
- The minimum distance between the tank shell and the inside toe of the dike wall shall not be less than half the height of the tank.
- The Dike enclosure for the petroleum class shall be able to contain the complete contents of the largest tank in the dike.
- Height of Dike(H): 1m<H<2m (Click here to learn about the tank dike wall height calculation)
Width of Dike(W): Minimum 0.6m (Earthen dike); No specific (RCC dike)
The separation distance between the nearest tanks located in separate dikes shall not be less than the diameter of the larger of the two tanks or 30 meters, whichever is more.
In a diked enclosure where more than one tank is located, the intermediate dike is provided. The height of the intermediate dike wall should be 450 mm if concrete and 600 mm if earthen.
Types of Dike
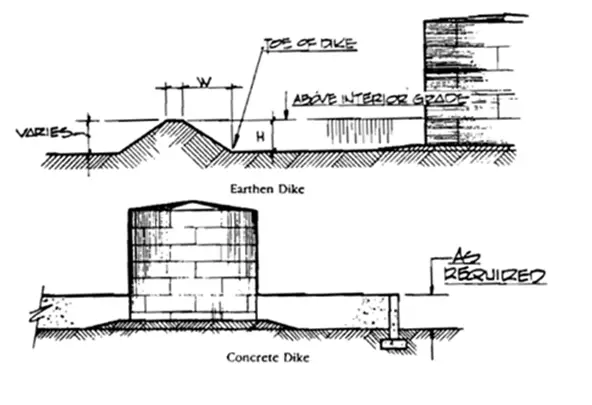
Tank Foundation Height
For fixing the tank foundation height, discuss with the Process and Mechanical team, the Net Positive Suction head requirement (NPSH) of the pump, especially for crude oil service.
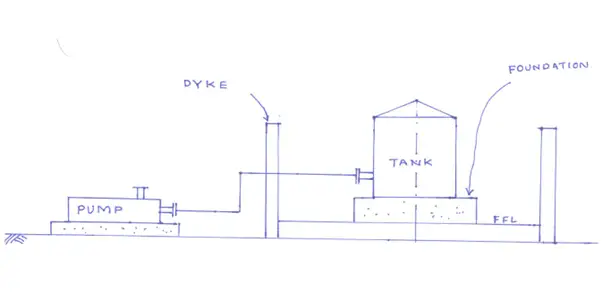
Sleeve Details in a Dike or Bund Wall
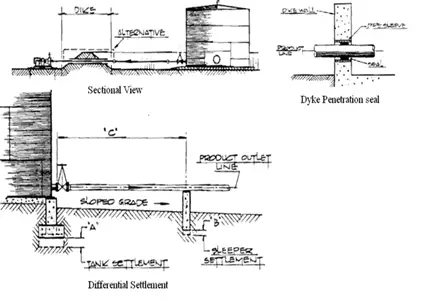
For locating tanks with respect to other tanks & equipment or vice versa, Refer to the minimum separation distance as mentioned in the company standard.
Tank Nozzle Orientation
Nozzle orientation shall be standardized for ease of operation & following points are to be noted:
- The nozzle on the roof is to be oriented such that under no circumstances operator step on the roof.
- Group the nozzles in one plane, so that operator movement on the roof is minimum.
- Instrument nozzles on the roof & shell shall be planned such that they are in the silent zone & do not experience fluid turbulence.
- The dip hatch nozzle is to be oriented such that there is no product spillage on the staircase & operating area.
- For Spiral stairways orientation, show the start point & endpoint of the platform. Also, provide a mid-landing platform base on tank height.
- Nozzles & platforms on the tank roof shall be marked separately in the nozzle orientation drawing. For more details about the tank-nozzle orientation, Click here
Tank Piping Layout
The optimum tank piping arrangement in a tank farm is the most direct route between two points allowing for normal line expansion and stresses. Usually, the following guidelines are followed while designing tank piping layout:
- Piping located in a diked enclosure should not pass through any other diked enclosure directly.
- The number of piping in the tank dike shall be kept minimum and routed directly outside the dike to Sleeper/Pipe rack.
- Pumps and associated piping shall be located outside the dike wall.
- A pipe may only be routed through bund walls if it cannot be passed over the Dike walls (eg. Suction line). Pipe passing through the dike shall be sleeved and sealed.
- Access platforms shall be provided for valve operation & for the instrument.
- The pump shall be provided in a curbed area with proper provision for draining.
- No piping shall be routed in the dropout(Maintenance)area.
- The tank outlet line to the Pump suction nozzle is a gravity flow line. Pump suction piping from the tank shall be as short as possible.
- A pipe connected to tanks shall be sufficiently flexible.
- Analyze the pipelines connected to the tank as per stress criteria given on a stress analysis basis.
- Blanket gas(Fuel gas) & Vent gas line (Big bore size) can be routed & supported over the tank roof. Support location & load of such lines shall be marked in the tank vendor drawing. So the vendor will take care load for the design of the raft and will provide support cleat at the required location. Again need to discuss with the vendor for the high load if any.
Supporting Tank Piping
In general, the following rules can be considered for supporting pipes connected to storage tanks:
- The tank Inlet & Outlet line can be supported either from the tank shell or the Tank foundation. If the support is taken from the tank foundation, this information shall be sent to the Civil department during the initial stage of the project & to the Tank vendor for providing vessel cleat.
- Spring support or a Teflon pad may be introduced as the first support from the tank as per stress analysis based on tank settlement.
- Keep the first support from the tank as far as possible. Group the lines for combined support.
Tank Farm & Piping
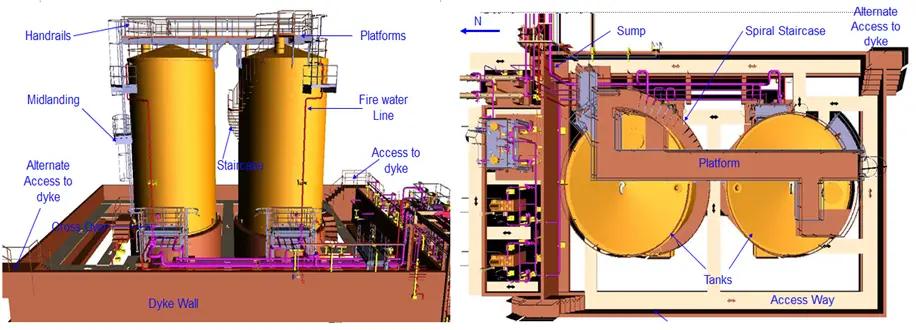
Fire Fighting for Tanks
The following firefighting requirements should be considered for tank and tank piping arrangements:
- A fire in one part/section of the plant can endanger another section of the plant.
- If a fire breaks out, it must be controlled/extinguished as quickly as possible to minimize the loss of life and property and to prevent the further spread of fire.
- Foam systems & water spray systems are often provided as part of the fire protection system.
- Permanent fire hydrants and monitors alternatively are used.
- Locate hydrant & monitor along the road for easy access and for operation.
Online Course on Tank Farm Piping Layout and Stress Analysis
If you are hungry to learn more about the tank farm piping layout and stress analysis procedure using Caesar II then the following online course will be ideal for you. The online Tank Piping course is designed by a highly experienced PMP-certified piping engineer who has worked with some of the renowned MNCs of the Oil and Gas design industries. So, what are you waiting for!! Simply click here to check the topics covered and then join the course at the cheapest price.
Few more Useful Resources for You.
Considerations for Storage Tanks Nozzles Orientation.
A Brief Presentation on Storage Tanks
Various Types of Atmospheric Storage Tanks
Tank Settlement for Piping Stress Analysis
An article on Tank Bulging effect or bulging effect of tank shells
An article on Tank Pad Foundation
Storage Tank design using software TANK and re-rating with API 620 & API 579
EMERGENCY VENTS FOR STORAGE TANK: A PRESENTATION
Modeling Piping Connection to Storage Tank
The Basic design of High-Pressure Storage Tanks to store liquefied petroleum gas (LPG)
Thanks my email address is hindshawo@gmail.com
I do the same thing in Uganda
I would to be in touch with you please
Hi anup sir,
Iam graduated in mechanical engineer and working as a process designer and I have an interest to become an piping engineer. So, I request you to give me a suggestion to become an piping engineer.
Pls can you share with me detail drawing of a dike. But earthen and concrete type.
in which standard I find the distance between the tanks
Thanks sirjee for your Tanks & Piping Blog.
So many times I read your blog on LinkedIn.
HI THERE;
I knew that the gas line from the top of storage tank to flame arrestor should not have flanges or valves for safety reasons I thought. IS THAT CORRCT. thanks
Hi Anup
This is amazing page, THK very much for your information & Data.
Do you have any experience about deformation of floating roof of storage tanks during construction? especially lower deck of floating roof.
Regards
M. Tavakoli
Sir what is the method for round/curve piping about tank or ring header by using E3D Software.
How to bend the pipe at any angle by piping component?