Applications of Buried Piping
The piping that is in contact with soil or runs below grade level is called buried or underground piping. In the oil and gas industry, we find frequent use of buried piping mainly for cross-country pipelines where security and safety justify the pipelines to be underground. Here security means the difficulty of sabotage and intentional damage to an underground pipeline. Safety means the safety of the environment and the surrounding population centers due to accidental damage to the underground pipeline.
The firefighting system network piping mostly runs below ground with certain sections above-ground. Above-ground pipelines are also intermittently buried in roads and railway crossings. Other major applications include Cooling water lines inside process plants, Oily Water Sewer lines, Contaminated Rain Water Sewer from the process catchment area, Sanitary systems, Equipment drainage to slop tank, Closed Blow-Down system, Storm Water, Liquid Effluent to the Effluent Treatment Plant, etc.
However, note that Piping should not be buried or installed underground if it can be reasonably avoided.
A basic understanding of the concepts of buried piping installation along with routine process design calculations related to piping such as pressure drop, velocity and erosion/corrosion limits for various pipe metallurgies are always advantageous for engineers. This article will provide some important guidance on buried or underground pipe installation.
Underground Piping in Process Piping
In the process piping industry, underground piping falls into one of the following two categories:
- Process lines &
- Drain lines (Closed Process drains and Open Gravity Drains).
All underground pipes are buried with a minimum cover of 500 -1000 mm on top of the pipe known as the minimum depth of cover. The actual depth of cover may vary depending on pipe stress analysis requirements, rail/road calculation, etc. In practice, the more depth of cover the better it is, but the same will increase project installation cost. So, an optimized depth of cover is decided by buried piping stress analysis.
Underground Pipe Types
Based on the application and service fluid, different types of underground piping systems are found. Some of those underground pipe types are:
- Underground Process pipes
- Underground Process and gravity drain pipes
- Contaminated and Uncontaminated stormwater.
- Chemical sewers
- Oily water service
- Firewater systems
- Solvent collection systems
- Sanitary sewers
- Combined sewers
- Blowdown systems
- Pump-out Systems
- Potable water systems
- Underground cooling water systems
Information required for designing an underground piping system
The major data or information required for designing underground piping systems are:
- Plot plan
- Topographic data
- Piping specification
- Soil investigation report/soil data
- Underground specification
- Types of the underground system
- General arrangement drawings
- Piping studies
- Site data
- Rainfall in the region
- Firewater requirements
- Frost depth
- Local codes and regulations.
- Invert elevations of lines at the process battery limit.
- Electrical and instrument conduit routings if applicable
- Client specifications
- Paving details
- Pipe Trench details
- Foundation size and plans
- Road limits, etc.
Underground Piping Materials
Different underground piping materials that are widely popular in the buried piping industry are:
Material | Uses in Underground Piping |
Carbon Steel | closed-drain systems, cooling water, and firewater |
Stainless steel | closed drains—chemical and corrosive service |
Concrete pipe | surface drainage, and for 15″ and larger pipes |
Glass Pipe | floor drains in process plants, mainly acid service |
Fiberglass-reinforced plastic pipe | corrosive service, low-temperature and -pressure systems |
PVC | corrosive service |
Cast iron | stormwater and oily water drains (hub and spigot fittings) |
Vitrified clay pipe | gravity drain systems |
Ductile iron | Process water |
Codes and Standards for underground Pipeworks
There are a number of underground piping standards that provide guidelines for the design, fabrication, and installation of buried piping systems. Some of the most common underground piping standards are:
- ASTM D2321
- ASTM A74
- ASTM A120
- SAS 236
- DIN 1230
- SAS 14
- ASTM D3034
- ASTM D1785
- ASTM C700
- ASTM A746
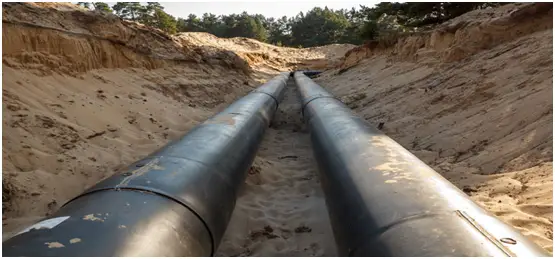
Over the past few years, underground firewater piping has gained popularity because of the following:
When untreated water comes in contact with above-ground carbon steel or lined carbon steel pipes, it becomes a source of corrosion and undermines the integrity of the firewater system. For this reason, corrosion-resistant HDPE or GRE plastic piping systems are more frequently used in recent times.
Although plastic piping possesses higher corrosion resistance to untreated water, it has much lower mechanical strength compared to carbon steel pipes considering forces such as impact and vibration.
So, to maintain the mechanical integrity of the plastic pipe, It is a logical option to bury the firewater plastic pipe and running across the installation.
Another option is to use exotic metallurgies (Stainless steel / Cupro-Nickel etc.) for firewater networks but that is not an economical choice. At the same time, common austenitic stainless steels are susceptible to chloride stress corrosion cracking in a water environment with high chloride content.
Problems Associated with Buried Piping
The main problems with underground piping are
- Even after applying mitigating measures such as external coating and cathodic protection, Buried Steel pipes are subjected to external corrosion.
- Draining, and cleaning buried pipes is difficult compared to an aboveground pipe.
- Leak detection and repair of buried pipes is a difficult and expensive exercise. Modern underground pipeline leak detection systems are available in recent times but they are very expensive to install.
- Buried pipes are subjected to mechanical damage when soil excavation work is being carried out in close vicinity.
- Buried pipes carrying hot fluids and subject to thermal expansion can cause pipe deformation and/or partial/total removal of the external protective coating is applied.
Corrosion Protection of Buried Pipes
All buried steel piping with the possible exception of cast iron piping should be protected from soil corrosion with a suitable external coating.
Following is the list of the most commonly used acceptable coatings and wrappings with approximate pipe surface temperature limitations:
- Fusion Bonded Epoxy (< 93°C)
- Liquid epoxies (< 107°C)
- Extruded Plastic (< 82°C)
- Tape Wraps (< 60°C) (higher temperatures applicable in case of high-temperature thermosetting tape)
- Coal Tar Enamels (< 60°C)
Tape wrap is often selected when small quantities of buried piping require protection because it is relatively inexpensive and easy to apply in the field. However, it has very low reliability with poor performance in water- and oil-saturated soils, and in cyclic temperature service. It requires proper pipe surface preparation and is easily applied improperly.
Protection for the coated pipe at weld joints and tie-ins is provided by field-applied fusion bonded epoxy, shrink sleeves of polyethylene, heat-cured liquid epoxy, or tape wrap.
Aside from the type of coating selected, proper application of the coating and maintenance of its integrity are required for the proper installation of a protected line. Because success or failure cannot be determined for an extended time after installation, usually years, attention should be paid to:
- Proper surface preparation for the type of coating used
- Coating Application as per the specified consistency and thickness
- Proper Care during laying and handling to avoid coating damage
- Proper cleaning, priming, and field coating of joints and pipe fittings
- Thorough Inspection of the applied coating for any damage and proper repair
- Finally, Backfilling and compacting to prevent contact with any material that could damage the coating
Cathodic Protection
Cathodic protection (CP) can be roughly defined as retarding or preventing the corrosion of a metal by imposing an electrical current flowing to the metal through an electrolyte. In the case of buried piping, the pipe is the metal and the soil is the electrolyte.
Cathodic protection is often used with coatings to protect piping. Regardless of the care used in coating and installing buried lines, there will often be small pinholes in the coating. A cathodic protection system can protect against corrosion at these points and significantly extend the life of the piping.
Cathodic protection is normally applied to buried piping as a system. At every place, where the cathodically protected pipe leaves the soil (or water), it must be electrically isolated from the aboveground continuation of the line if the continuation is not part of the CP system. This must be done with an insulating flange gasket kit that uses electrically insulating bolt sleeves, nut washers, and a sealing gasket in a conventional flange makeup.
The major users of cathodic protection are Cross country steel pipelines and steel submarine piping.
Online Buried Pipe Stress Analysis course using caesar II
If you need to learn the buried piping stress analysis basics then click here and join the course
Few more useful resources for you..
Buried GRP/FRP pipe Laying and Installation Procedure
Basics for Stress Analysis of Underground Piping using Caesar II
Underground Piping Stress Analysis Procedure using Caesar II
What if Piping Continuation is Unknown? Part 2. Underground Piping
Various Analysis methods for Underground Piping Using Caesar II
Cathodic Protection Basic Principles and Practices
Amazing!
This information worth it. This article helps me to increase my knowledge to protect the buried pipelines from erosion.
Such a wonderful and informative site you have here.
As a piping engineer who is active in both Construction and Engineering departments, I am learning so much from your web site.
Congrats and keep up the amazing work.
What is the standard “Refinery Plant” underground utility piping layout? Depths? Sizes? for:
1- Sewer System
2- Portable Water Piping
3- Electrical Cables
4- Telecommunication Cables
very helpful in understanding the problem of under ground pipe .
Thank you for your kindness .
Thank you