What is ASME B31.3?
ASME B31.3 is part three of the overarching ASME B31 Code for Pressure Piping and it applies to pipe systems that transport chemicals, petroleum products, fluidized solids, refrigerants, cryogenic fluids, and gas, steam, air, and water. ASME B31.3, also an American National Standard prescribes guidelines for materials and components, design, fabrication, assembly, erection, examination, allowable stress, acceptance criteria, and testing of process piping to aid numerous groups which include the owner of the piping installation, as well as the designer, owner’s inspector, and manufacturer, fabricator, and erector.
Major Changes in ASME B31.3-2018
Most of you must be aware that ASME B31.3-2018 which revises the 2016 edition of the same standard for process piping has been published in the month of August 2019 with the date of issuance as 30th August 2019. This code will be universally applicable after six months from the date of issuance i.e from March 2020 onwards. In addition to the many clarifications, and updated references to codes and standards, there are few substantive changes made to the latest edition of this standard, a few of which are mentioned below:
Changes with Respect to the Scope of B31.3
1. The scope of the ASME B31.3 has been revised in the 2018 edition as compared to the earlier 2016 edition. Now the latest code specifically mentions that the piping for onshore and offshore petroleum and natural gas production facilities, ore processing, food and beverage processing facilities, etc are included in the scope.
Specific Permission of Owner
2. Added specific permission for the owner to designate a representative to carry out selected responsibilities required by this Code, and noted that the owner retains ultimate responsibility for the actions of the representatives.
New Appendix W
3. New appendix W related to “High-Cycle Fatigue Assessment of Piping Systems” is added in the recent edition of the Code. The method is intended to be used when the number of significant stress cycles exceeds 100,000.
A significant stress cycle is defined as a cycle with computed stress ranges greater than 20.7 MPa (3.0 Ksi) for ferritic and austenitic steels. For other materials. or corrosive environments, all cycles shall be considered significant unless otherwise documented in the engineering design. The existing rules provide an acceptable method of evaluating piping systems for fatigue when the number of significant stress cycles is less than or equal to 100,000. The piping cyclic loadings may be due to thermal expansion, anchor motion, vibration, inertial loads, wave motion, or other sources.
Additional Piping Vibration Sources
4. External vortex shedding (e.g., wind), Acoustically Induced Vibration (AIV), etc are added additionally as piping vibration sources against which the piping system must be designed and supported compared to the earlier edition of B31.3.
Basis Of Design Stress
5. Basis of Design stress values in clause 302.3.2 is revised from 2016 values.
Weld Joint Stress Reduction Factor
6. Weld joint strength reduction factor, W, was included as an allowance for pressure and temperature variations. A new row for Carbon Steel was added in Table 302.3.5, “Weld Joint Strength Reduction Factor, W.
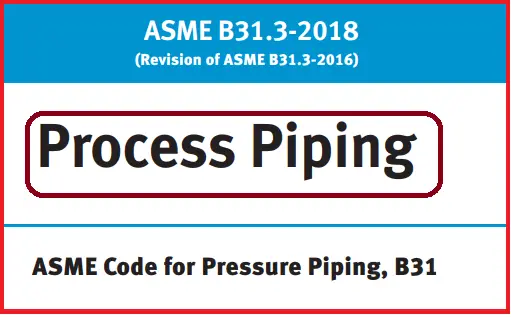
Elevated Temperature Fluid Service
7. For Elevated Temperature Fluid Service the allowable stress for occasional loads of short duration, e.g., surge, extreme wind, or earthquake, has been modified with respect to B31.3-2016, and now it may be taken as the lowest of a, b or c:
- the weld strength reduction factor times 90% of the yield strength at the metal temperature for the occasional condition being considered
- four times the basic allowable stress provided in Appendix A of the code
- for occasional loads that exceed 10 h over the life of the piping system, the stress resulting in a 20% creep usage factor in accordance with Appendix V of the code.
Flange Design
8. The new edition permits to design of flanges following ASME BPVC, Section VIII, Division 2, 4.16 (Design Rules for Flanged Joints) or in accordance with ASME BPVC, Section VIII, Division 1, Mandatory Appendix 2 (Rules for Bolted Flange Connections with Ring Type Gaskets) using the allowable stresses and temperature limits of this Code. For flange design, the reference of code ASME BPVC, Section VIII, Division 2, 4.16 as an acceptable way to design flanges for B31.3 applications is newly added. The Division 2 procedure considers pressure, gasket seating, externally applied axial forces, and net-section bending moments.
Stress Intensification
9. Added specific references to ASME B31J-2017 as a resource for stress intensification and flexibility factors as an alternative to Appendix D.
Heat Treatment for Structural Elements
10. Added explicit language requiring heat treatment for structural attachments welded directly to pressure-containing materials when the piping is required to be heat treated.
11. Added a definition for readily accessible: those surfaces that can be examined from not more than 600 mm (24 in.) and at an angle not less than 30 degrees to the surface to be examined. Increased visual examination required for normal fluid service welds from 5% random to 100%.
Fatigue Analysis for High-Pressure Fluid Service
12. A fatigue analysis is required for all piping systems in Chapter IX High-Pressure Fluid Service. In previous editions, this analysis was permitted to be performed in accordance with the BPV Code, Section VIII, Division 2, or Division 3. Division 2’s fatigue analysis involves using a standard S/N curve to determine the design fatigue life. Division 3 also allows an S/N curve approach, but only if it can be shown that the piping component will fail in a leak-before-burst mode. Otherwise, a more rigorous fracture mechanics evaluation is required. The Division 3 S/N analysis contains several requirements that are not included in Division 2, such as surface finish and means stress corrections. Because the Division 2 approach is less precise than the Division 3 approach, wherever possible, Division 2 was eliminated as an option for the required Chapter IX fatigue analysis. Text on fatigue analysis for unlisted high-pressure piping components was added.
13. Rules for the use of piping components not listed in Table 326.1, “Component Standards,” were altered.
14. The scope of Chapter IX, “High-Pressure Piping,” was revised in its entirety.
15. Table C-6M, “Moduli of Elasticity for Metals (SI Units),” was added.
16. Examples of rounding for piping that has been placed in service were added as new section F300.1.4.
17. General statements were added in Appendix F, “Guidance and Precautionary Considerations.”
18. Appendix Z, “Preparation of Technical Inquiries,” was revised in its entirety.
Users should note that only a portion of the changes to ASME B31.3-2018 is included in the above list. Readers are requested to highlight other major changes in the comments section.
Learn the ASME B31.3 code changes in different years:
What’s new in ASME B31.3-2020? ASME B31.3 2020 vs 2018
Changes in the 2018 Edition of ASME B31.3 2018 with respect to the 2016 edition.
14 major changes in ASME B 31.3-2016 with respect to its earlier edition (ASME B31.3-2014)
Substantive Changes to 2014 Edition of ASME B 31.3
Major Stress-related differences in Between 2012 edition and 2010 edition of ASME B31.3.